Lubrication failure is almost inevitable when it comes to machinery. Even with the best practices in place, certain factors can cause these failures and result in costly repairs and downtime. Understanding what causes lubrication failure not only allows maintenance managers and technicians to recognize the warning signs sooner but also puts the necessary measures into action ahead of time. By taking proactive steps and properly maintaining lubrication systems, you can prevent unanticipated failures. Here we’ll discuss potential causes of lubrication failure so that you have a better idea of effective preventive measures.
Common Causes of Lubrication Failure
There are numerous potential failure causes in machines that need a lubricating film. Surface deterioration brought on by a contaminant is typically the most frequent. Surface wear mechanisms come in a variety of forms, the bulk of which are brought on by a particle contacting a bearing, rolling element, gear face, or pump component’s surface. However, we’ll break down that and the other potential lubrication issues below.
Adhesive Wear
When the lubricating film thins out, metal-on-metal contact occurs. The result is adhesive wear, which means that asperities on the surface basically cold weld together. Then, as the equipment continues to operate, shearing occurs and creates abrasive debris. Adhesive wear can result from excessive load, low speed, or reductions in fluid viscosity.
Abrasive Wear
In the area between two moving surfaces, abrasive particles enter, embed themselves in one of the surfaces, and cut material from the other surface. You might think that the most dangerous abrasive particles are the biggest ones, but that’s not accurate. In fact, particles that are equal to or slightly bigger than the space between the two surfaces inflict the most harm. Alternatively, smaller particles will float through the system, and larger particles won’t be able to enter.
The worst thing about abrasive wear is that it will only get worse if you don’t address it. This is because abrasive wear particles can get work-hardened. Simply put, that means the material becomes harder than the parent surface and grows increasingly more abrasive. If you don’t remove these particles with filtration or other methods, they will recirculate and create further wear. Eventually, this will lead to early component failure in the system.
Erosive Wear
The easiest way to explain erosive wear is to compare it to erosion in nature. When a constant stream of water flows over rocks, it creates erosive wear. It is a gradual process that can make a big impact over time. When it comes to erosive wear in a lubricating system, surfaces that experience a high flow of particles are most susceptible. This is especially common in metering valves due to the high-velocity flow. Denting and eventual fatigue of the surface are both effects of erosive particles.
Fatigue
When particles get stuck between two moving surfaces, they put a constant strain on the surfaces. At first, the surfaces will have dents that begin to crack. Next, the cracks expand, which ultimately leads to the failure of the surface and the formation of a spall.
Water Contamination Failure
While all of the causes of lubrication failure up to this point have been particles, some causes are non-particle contaminants. The most common of which is water. The effects of water creep up on you gradually, yet it can cause catastrophic results. Frequently, rust is the most typical consequence. The oxygen in water can cause metal surfaces to oxidize. In most cases, the metal oxides of iron or iron alloys do not possess the same level of physical integrity as their original state, and as a result, they fail.
The presence of excess water is the real cause of many failures that are incorrectly attributed to lubricants. The following is a list of some of the equipment-related consequences that water can create:
- Erosive Wear and Etching
- Hydrogen Embrittlement
- Corrosion and Rust
- Oil Film Loss
- Hard Water Deposits
- Bearing Oxidation
- Filter Blocking or Freezing
- Reduced Component Life
Air Related Failure
Although air is present in the vast majority of lubricating oil systems, it is crucial to understand the different types and their impact on lubrication. The four phases of air in lubricating systems are:
Free Air
Free air is trapped in a system and may have minor contact with the lubricant. When you start equipment and don’t properly bleed the lines, free air can enter into circulating oils. This can be a contributing factor to additional air problems.
Dissolved Air
You cannot easily extract dissolved air from the system. Dissolved air is an issue when temperatures quickly rise or when pressure suddenly drops. There is as much as 12% dissolved air in petroleum oils.
Entrained Air
Dissolved air transforms into tiny bubbles during system startup or overheating. If the bubbles have a diameter of less than 1 mm, they will remain in the liquid phase of the oil. This is entrained air. Air entrainment is handled differently than foam and is typically a separate issue. It can cause many lubrication issues, including pump cavitation, erratic hydraulics, vibration, oxidation, low viscosity, low oil pressure, and more.
Foam
All of this air contamination builds up to create foam. Foam is simply a collection of tightly packed bubbles covered by a thin coating of oil that collects on the surface of the oil. In most cases, foam isn’t harmful to lubrication. However, it can cause issues with oil level control, safety or environmental hazards with oil overflow, or even create airlocks. If foam grows so severe that it gets sucked into the lubricating system and lubricates your equipment, then you absolutely must address it.
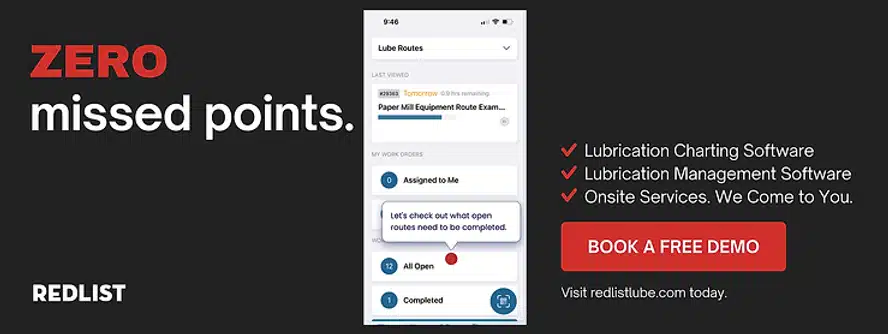
Minimizing Contamination Leads to Lubrication Success
Most lubrication failures are due to contamination. In fact, studies have found that over 75% of wear-related failures were caused by particle contaminants. The majority of particles originate as airborne dirt, which then enters lubricant and fuel reservoirs before being carried to bearings, bushings, seals, valves, and other machine components. There, they become the key components of abrasion, erosion, and fatigue failures. The contaminants also induce lubricant degradation, hence lowering the lubricant’s lifespan and diminishing its lubricating capacity. With machine clearances measured in thousandths of an inch, it doesn’t take much contamination to wreak havoc on delicate components. Even particles as small as 10 microns might disturb the lubrication coating and cause major wear. However, using filters and reservoir air breathers to decrease water and particulate contamination is a tried and true method for lubrication success.