Lubricants are a crucial part of any machinery, and there are various types on the market. One of the most important factors to consider when picking a lubricant is viscosity. Viscosity describes how thick or thin the liquid is. Additionally, monitoring changes in viscosity helps you track lubricant conditions. Thus, you can identify potential equipment issues before failure. Here, we’ll cover everything you need to know about high vs. low viscosity lubricants.
What is Oil Viscosity?
Viscosity is defined as a fluid’s resistance to flow. The higher a fluid’s viscosity, the greater its resistance to flow. For example, honey has a higher viscosity than water.
Before going further, there are some critical concepts of viscosity to define. These are:
- Viscosity Index (VI)
- Two types of viscosity measurements
- Dynamic Viscosity (DV)
- Kinematic Viscosity (KV)
Viscosity Index (VI)
Fluid flow relies on temperature. Heat causes an increase in the internal frictional relationships among fluid molecules. And this increase results in changes in the way a fluid moves. In higher temperatures, fluids experience thinning or become less viscous. In lower temperatures, fluids thicken or become more viscous.
A fluid’s viscosity index describes how resistant it is to changes in temperature. High Viscosity Index lubricants will experience less thinning or thickening when temperatures change. If your machine and its components function in a wide range of temperatures, you need a lubricant with a high VI. A high VI ensures lubricant stability and effective lubrication.
Dynamic Viscosity (DV) or Absolute Viscosity
Dynamic viscosity, or DV, is absolute viscosity. It is the viscosity measurement independent of density. Absolute viscosity is the internal resistance to flow under an applied force. It is the ratio of the shear stress to the shear rate of the fluid.
Shear stress refers to the force applied parallel to the surface of the fluid. The shear rate refers to the rate of deformation of the fluid resulting from the applied force. The unit of absolute viscosity is expressed in pascal seconds (Pa·s) or centipoise (cP).
Absolute viscosity is an important property of fluids. A wide range of applications, such as in the design of pumps, pipelines, and lubrication systems, use absolute viscosity. Also, it is an important parameter in fluid dynamics. It can model fluid flow and predict behavior under different conditions.
Kinematic Viscosity (KV)
A fluid’s KV or kinematic viscosity describes the viscosity of a fluid in relation to its density. Two fluids can have the same DV but have different KV if they have varying densities.
Understanding viscosity measurements help you choose the right lubricant for your operating conditions. For lubricants used in high-speed and high-pressure systems, DV values are the ideal basis for viscosity. Under these conditions, there is a negligible gravitational force but very high external forces. These forces cause changes in lubricant viscosity and other lubricating characteristics.
How Do You Measure Viscosity?
Different types of viscometers can measure DV and KV. A viscometer is an instrument that measures the viscosity or the resistance of a fluid to flow. Industries such as oil and gas, food and beverage, pharmaceuticals, and many others that need the measurement of viscosity use a viscometer. Viscometers are important tools for quality control and process optimization in many industries. There are various types of viscometers available, each with its own specific function. Some of the common types of viscometers include:
- Rotational Viscometers
- Capillary Viscometers
- Falling Ball Viscometers
A rotational viscometer measures DV by rotating a probe into a fluid and measuring the resistance the probe experiences as it turns. A capillary tube measures KV by pouring fluid into it and measuring the time it takes to flow naturally by the force of gravity.
High Viscosity Fluids as Lubricants
When it comes to lubrication, high viscosity fluids are perfect for heavy-duty applications. These applications involve high loads and high temperatures. Heavy-duty engine oils, gear oils, and greases are all lubricants in this category.
Low Viscosity Fluids as Lubricants
Low viscosity fluids are suitable as lubricants in systems involving lower loads and lower temperatures. Engine oils for passenger cars and light trucks are typical examples of low viscosity lubricants. Furthermore, low viscosity lubricants tend to evaporate more quickly.
Why is Viscosity Important to Lubrication?
Most machinery or equipment used in an industrial setting is more on the heavy-duty side. Thus, you rarely use low viscosity lubricants in industrial settings. Low viscosity lubricants are less effective at reducing component wear in high loads and high temperatures. They underperform when it comes to building enough film strength under these conditions.
Viscosity affects:
- How well the lubricant will cling to surfaces
- The success of lubrication
- And how long it will last
In this case, the higher the viscosity, the thicker the oil, and the better it will lubricate. The lower the viscosity, the thinner the oil, and the less it will lubricate.
Also, viscosity is an excellent indicator of asset health. If your lubricant viscosity changes suddenly, you can run through all the potential root causes of viscosity changes. Or, if your lubricant viscosity remains steady, that’s a good sign that none of those issues are present.
The Danger of Low Viscosity
Although seldom used in industrial settings, low viscosity lubricants are cost-effective. These types of lubricants can be valuable for light-duty applications. But they can become even less viscous over time and with prolonged use. Thus, you must look into the viscosity index of these lubricants, not only their viscosity.
Low viscosity can result in increased wear and tear on machinery. This leads to reduced efficiency and higher maintenance costs. In some cases, lubricant degradation can cause expensive or dangerous unexpected failures. So, it is crucial to watch lubricant viscosity levels even for low viscosity lubricants.
The Danger of High Viscosity
While it may seem that high viscosity lubricants are better for everything, there is a limit. High viscosity lubricant will provide good lubrication at operating temperature. But, there are instances when heavy-duty machines experience low temperatures. These instances include during startup while the equipment is still warming up. Low temperatures can increase viscosity, causing excessive friction and harmful effects. In this case, you must choose a lubricant with a high VI that can resist too much thickening at low temperatures.
The Implications of Viscosity on Business Operations
Selecting the incorrect viscosity can lead to increased wear and tear, energy inefficiency, or even equipment failure, all of which can result in significant downtime and operational costs. For instance, lubricants with too high a viscosity may cause excessive energy consumption and heat generation, while those with too low a viscosity might fail to protect against friction and corrosion effectively.
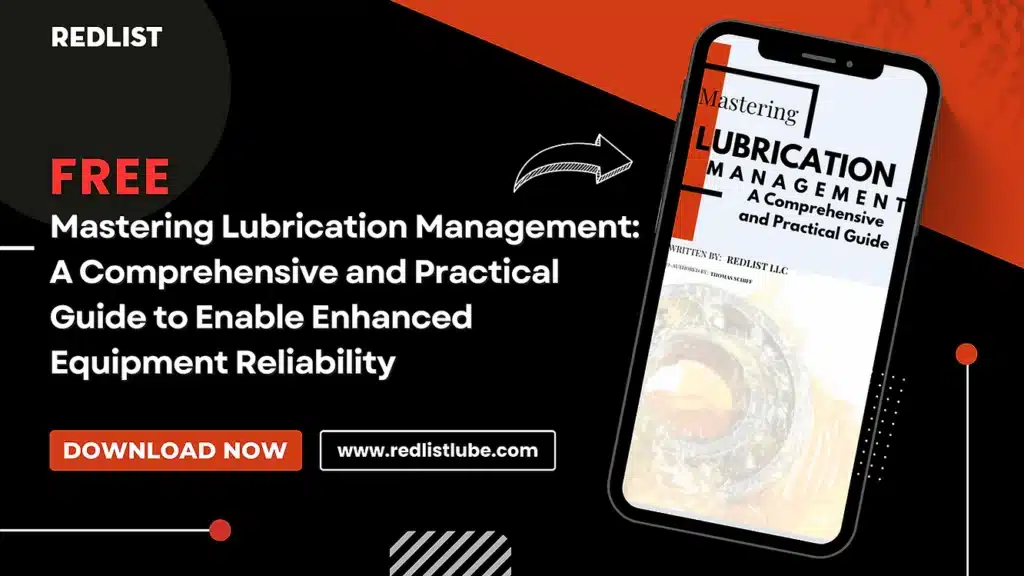
Leveraging Redlist’s Lubrication Management Software for Operational Excellence
Redlist’s lubrication management software becomes a powerful ally in this domain by providing a platform for:
- Real-time Monitoring: Tracking the viscosity levels of lubricants in machinery, alerting maintenance teams to any deviations that could indicate contamination, degradation, or incorrect product application.
- Education and Training: Offering resources and analytics to help teams understand the implications of viscosity choices and to train them in best practices for lubrication management.
- Selection Guidance: Assisting in selecting the appropriate lubricants for different machinery components based on manufacturer recommendations and industry standards
- Growth and Improvement: Analyzing historical lubrication data to identify trends, predict maintenance needs, and improve the overall lubrication program, thus contributing to business growth and sustainability.
Embracing Growth with Smart Lubrication Management Software
In the intricate world of industrial lubrication, the choice between high- and low-viscosity lubricants is not trivial. It requires a strategic approach underpinned by knowledge, vigilant monitoring, and the support of a lubrication management software like Redlist. By implementing a comprehensive lubrication strategy with an emphasis on preventive measures, businesses can ensure the longevity and reliability of their machinery, minimize downtime, and foster an environment of continuous improvement and growth.
Take Action: Book Your Free Demo Today!
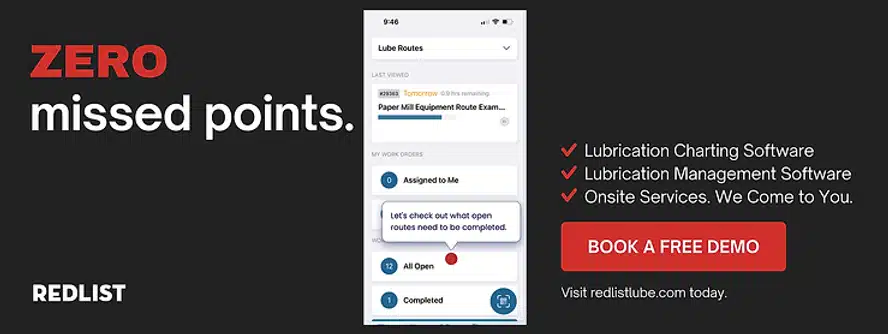
Don’t let viscosity variances be the chink in your operational armor. Discover how Redlist can revolutionize your lubrication strategy. Book a free demo today and take the first step towards lubrication excellence that drives growth and operational superiority.