Redlist has worked with countless maintenance teams from various industries, and we have encountered similar challenges in all these industries. In the area of lubrication maintenance and management, in particular, some problems and issues are common regardless of the industry type and company size. In this article, you will learn about common lubrication issues and why they happen. Also, we share the best ways to diagnose and resolve them so you can avoid equipment failure and downtime.
Issue #1: Non-Transferable Process
Lubrication processes and programs are non-transferable when there are no systems in place to train new technicians to replace the existing ones. This issue often happens in established facilities as well as new ones.
In established facilities, most experts that manage lubrication have held their positions for decades and are nearing retirement. In all the years of their service, they were not given a chance to train a successor skilled enough to replace them. Additionally, the system neglected the need for documenting procedures. At the very least, this documentation could be used for training new technicians.
In newer facilities, the focus is on the growth of the company. Thus, recording lubrication programs and their processes to make these transferable is at the bottom of the priority list.
This issue is apparent when the lubrication process cannot proceed without one particular technician. If this person is not present, his team is incapable of carrying out standard procedures, making fundamental decisions, or fixing minor problems. Another sign of this issue is if new hires do not go through a formal training procedure but through a ‘watch-what-I-do’ method.
Solution: Documentation
The critical step to resolving the issue of a non-transferable lubrication process is documentation. In established facilities, this process can start by working with the individuals who are at the heart of the lubrication process. Interviewing them and writing down their process steps is a start, but it will not be enough. You should be able to record the nuances of their tasks, which may take time and repeated observation of them doing their duties. Visual records like photos and videos will also help. Furthermore, take note of how these experts evaluate their machines by every look, sound, and odor.
In newer facilities, documentation may require the development of a new process. But once these procedures and programs are established, documentation and execution will encounter no issues. If you have the resources, assign at least two personnel to become the experts on all things lubrication and machine-related. You can further ensure the transferability of your process by letting these experts train technicians as apprentices or future successors.
However, some facilities document their process only to find they missed an important detail. Here is a quick list of everything you should include in your process documentation:
- How lubricants are applied
- Lubrication System, Tools, and Asset Cleaning
- Lubricant Storage
- Waste Disposal
It is critical to document standard procedures based on regulations, not simply your procedure if it is not up to code. Implement these standard procedures if your current ones are incorrect or not advisable. Documentation is also a chance for you to evaluate your current processes and improve on them.
Issue #2: Overgreasing
Some of the lubrication technicians we’ve worked with believe that more is better. But in the case of lubrication, more can be harmful. Overgreasing or applying lubricants above recommended levels can promote contamination and increase operating temperatures. These effects further result in premature wear and failure of bearings and machine parts.
Lubricant applicators or grease guns are precision instruments that require proper use and maintenance. You must have these instruments regularly calibrated to release appropriate amounts every time they are used. If misused, these applicators can release harmful amounts into bearings and other sensitive machine parts.
Overgreasing is best observed by visual inspection. Examining lubricant usage can also give you an idea if your consumption is beyond the expected requirements of your machines. Furthermore, interviewing your technicians on their methods can help diagnose if your facility is guilty of overgreasing.
Solution: Standardization
Every machine should have a set greasing requirement. The ideal solution for overgreasing is to have a standard amount and application frequency for every machine.
You must also have your greasing guns checked for accuracy. If you can, try to have a single grease gun model for easy standardization and use. Then, follow best practices for calibration and labeling. Additionally, training your technicians on proper greasing will help implement these standards more effectively.
Issue #3: Inaccurate Oil Analysis
Often, lubrication management relies on analytical tests without thoroughly understanding their purpose and methods. Oil analysis is incredibly helpful in monitoring oil and machine conditions, but many tests are commonly misused. Also, oil analysis can become inaccurate due to incorrect sampling points and other methods.
In most facilities we’ve worked with, oil samples for testing come from a drain port or by drop-tube technique. Oil from drain ports produces inaccurate oil analysis results because it frequently contains huge amounts of contaminants. However, drop-tube sampling is unreliable and involves turning the machine off, resulting in downtime.
Diagnose inaccurate oil analysis by evaluating the results and double-checking them with an actual inspection. If oil analysis results and actual inspections do not correspond, it’s time to reconsider your sampling points and methods.
Solution: Assessment & Revision
The remedy to inaccurate oil analysis is to assess the methods and revise the source of inaccuracy. You may need to consult a technical expert on oil analysis and lubrication testing.
Every facility is unique in its process and machine. Yours may require a different sampling point, equipment, or method from other facilities. Oil analysis experts can help you identify the appropriate sampling details for accurate oil analysis results.
The revision of your sampling process may require outfitting your current components, re-assigning your sampling points, and installing additional sampling hardware. In addition, formal training or retraining of the personnel who perform oil sampling may also be required.
Issue #4: No Labeling System
Any efficient lubrication program must have a labeling system that facilitates correct procedures, prevents cross-contamination, and reduces miscommunications. A labeling system also promotes the health and safety of not only the lubrication personnel but also all the individuals in a facility. Establishing a labeling system is essential if you plan to integrate your current lubrication program into a digitized lubrication management software like Redlist.
The facilities we’ve encountered without a labeling system in place have a disorganized lubrication management program. In addition, their lubrication personnel and technicians are unfamiliar with their designated materials, tools, area, and machine signages.
The lack of a labeling system is apparent as soon as you enter a facility. Someone with zero knowledge and experience in lubrication should be able to identify lubrication-related inventory and processes just by reading labels in your facility.
Solution: Labeling
The solution is obvious with this issue. A labeling system requires some time to develop and more time to integrate into your work culture. The key is to have consistency and persistence.
Issue #5: Ineffective Anti-contamination Accessories
The final common lubrication issue on our list is the use of accessories like breathers and dust caps that are not effective. These anti-contamination accessories should prevent surface damage to machines by preventing the entry of microscopic particles into the oil and other dust-sensitive parts of the machine.
Many facilities use low-quality original equipment manufacturer (OEM) versions of products for their accessories. Untested, these versions can appear sufficient. However, they often have substandard materials and, thus, substandard effectiveness. An OEM breather, for example, can have a missing layer of filter that should trap smaller contaminating particles. Breathers are also designed to prevent moisture contamination, and an OEM version may not be up to the task.
To determine if ineffective anti-contamination accessories are one of your lubrication issues, you can perform a contamination risk analysis. You can also evaluate the effectiveness of your current accessories and have a third-party test their quality.
Solution: Replacement
If your current accessories are ineffective in preventing contamination, the only way to resolve this issue is to replace them. Select the appropriate breather or dust caps based on their effectiveness and with consideration to your environment and operating conditions. When hindered by the high cost of high-quality accessories, consider the contamination costs resulting from low-quality products.
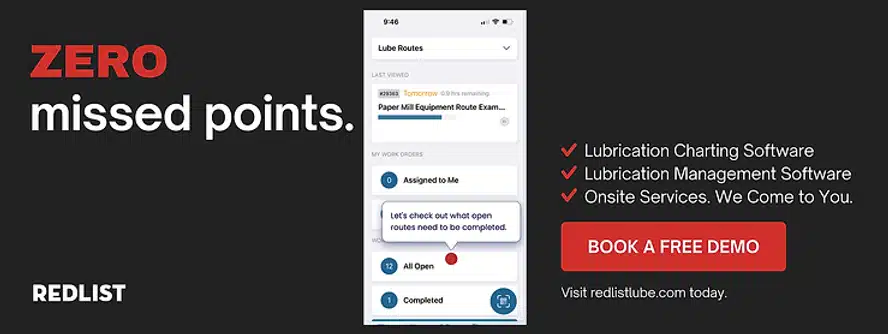
Ultimate Lubrication Solution with Redlist
A lubrication management software like Redlist is a valuable tool when diagnosing and resolving the lubrication issues listed above. As mentioned, every industry encounters these issues, and Redlist has been consistently successful in helping our clients tackle them. With minimum effort and time, Redlist lets you implement your strategies, manage your lubrication systems, and fix your lubrication management downtime. This can help you solve common lubrication issues and more. Schedule a demo with us today to learn more about using software to optimize your lubrication management!