When it comes to contamination, the best defense is a good offense. By properly protecting against lubricant contamination, you can help minimize the negative effects it can have on your equipment. In this blog post, we’ll discuss some of the best ways to protect your lubricant from contamination and keep your equipment running smoothly.
Why is it Important to Prevent Lubricant Contamination?
Lubricant contamination is one of the main reasons why industrial equipment breaks down. Today, lubricants can offer years of wear prevention if they are kept dry and clean. But, with contamination, you will find it challenging to go weeks or even months without needing to change the oil.
A few signs of critical lubricant contamination include:
- Visible Water and Dirt
- An Increase in Water and Particle Contamination on Lubricant Analysis Tests
- Regular or Increasing Bearing Failures
All of these issues mean you have a lubricant contamination problem to address.
Is Filtration Enough to Manage Lubricant Contamination?
When you think of managing lubricant contamination, the first thing that comes to mind for most people is filtration. Filters and desiccant breathers remove solid particles and water from the lubricant, which helps to keep it clean and free of foreign matter. By using a filter, you can extend the life of your lubricant and minimize the risk of damage due to contaminants. There are a variety of filters available on the market, so be sure to choose one that suits your specific needs.
However, filtration addresses the removal of contaminants, but it doesn’t solve the root cause. Where are these contaminants coming from? How are they entering your lubricant?
Failed Oil Seals
If you filter new oil, then you’re putting clean lubricant in your equipment. In this case, the most common source of contamination is a broken oil seal. The solution? Oil seals or bearing isolators that are the right fit and specification for your application. There are differences between bearing isolators. Choosing the right technology for the equipment class and modifying the design of the isolator can enhance performance.
How to Use Bearing Isolators for Protection Against Lubricant Contamination
Lubricant contamination can lead to a variety of problems in a plant or machine, from poor performance to component failure. One way to help protect against lubricant contamination is by using bearing isolators. Bearing isolators are devices that separate bearings from the rest of the machine, preventing contaminants from getting into the lubricant and causing damage.
Ensure the Bearing Isolator Works During Operation and Shutdown
You can improve your use of bearing isolators by understanding how bearing systems work. Most bearing isolators do a great job of preventing lubricant contamination during operation. This is thanks to centrifugal force from the rotation that helps expel any contaminants that enter the system. But, when the system shuts down, the force isn’t there, and contaminants can enter.
A typical bearing housing interacts with its surroundings by always attempting to maintain equilibrium. Due to its higher temperature and pressure than the atmospheric side, the housing vents to the atmosphere while it is in use. The temperature inside the housing drops after the shutdown. The bearing housing starts to create a vacuum because the cool air inside is denser than the warm air outside. This means that outside air enters until the system achieves equilibrium. Furthermore, moisture and dust enter the system with this external air.
Some bearing isolators include a design modification that keeps contaminants inside the isolator and reduces their energy to prevent this contamination under static conditions. After entering the bearing isolator, the energy breaks down as the moisture and dust are pushed through an axial throttling gap and a greater radial gap. This design allows the contaminants to collect in an internal condensate trap, which you can drain them out of. Even when the system is shut down, the contaminants never get to the lubrication.
Consider Isolators Specific to Your Equipment
Not all bearing isolators are the same. So, your equipment or your application may require a specific design. With a typical bearing isolator, the majority of rotating drives will work well. For instance, a lot of pump and motor setups work well with standard bearing isolators. But, that doesn’t mean it works for all equipment. If you’re having lubricant contamination issues, consider a bearing isolator design that is particular to your piece of equipment. This is especially important if the application is vital or specialized.
Flange-Mounted
Bearings installed on flanges assist in reducing axial load or pressure on the bearing. Because pushing the stator is neither advised nor feasible, a bearing isolator made for them must be modified.
Gearboxes
The majority of gearboxes are installed below the equipment they operate. The unfortunate result of this placement is that equipment leakage runs a high risk of contaminating the gearbox lubricant. Because of this, you may want a stronger seal for your gearboxes. Also, whichever gearbox lubrication method you use must keep water, dust, and other impurities out of the lubricant. You can enhance the lubrication system’s cleanliness by choosing an oil seal made especially for gearboxes.
Pillow Blocks
Many industries and applications use pillow block housings. Producers typically use labyrinth (LER/LOR) rings to seal the pillow block bearings, but these rings may not be sufficient for long-term operation and lubricant life. You can increase your equipment’s and lubricant’s lifespans with a new bearing isolator. These must, however, fit into the LER/LOR ring grooves that already exist. Since pillow block bearings must fit tightly, clean lubricant is crucial. If the original seal fails too soon, many end users choose to replace it with a bearing isolator made for pillow block bearings.
Steam Turbines
Power generation companies face a challenge when it comes to sealing steam turbines. Due to the extreme operating temperatures, steam may coalesce and enter the lubricant. Therefore, it is vital to select and install a bearing isolator specifically for turbines. As a result, it is often made up of two pieces and requires a tight fit to protect the bearings completely.
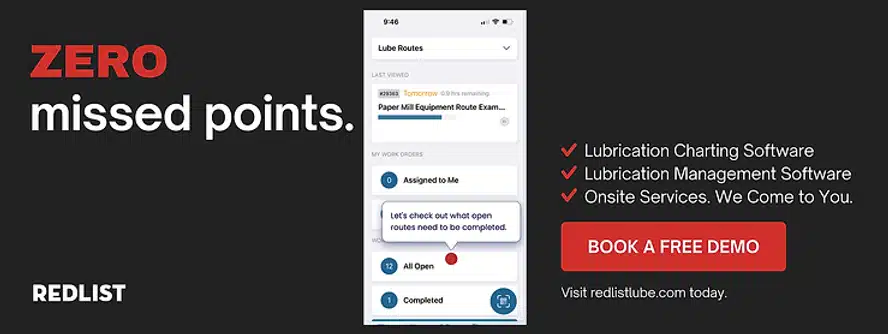
Minimize the Risk of Lubricant Contamination
While it is impossible to completely avoid lubricant contamination, using bearing isolators can help minimize the risks. By following the tips we’ve outlined in this blog post, you can install and use bearing isolators effectively to protect your equipment from damage caused by lubricant contamination.