In today’s fast-paced and technology-driven world, it is essential for business owners, maintenance managers, and technicians to stay informed on the latest lubrication system developments. One such necessity is the introduction of dual lube oil system accumulators and their significance in proper machine operation and maintenance. Dual lube oil system accumulators bring a host of benefits that include better pressure control during start-ups; reduced wear and tear on moving parts; improved bearing life; less downtime due to component failures; lower operational costs; decreased environmental impact; and, overall better safety records within production facilities. You can experience all of these amazing results as well from the increased protection that these specialized components can provide. Read on to understand why implementing a properly configured dual lube oil system is beneficial for any facility!
Why are Dual Lube Oil System Accumulators Important?
You must place dual accumulators in essential equipment lube oil systems to effectively prevent unit low oil pressure trips during transient events. Even if you properly assemble a lube oil system, eventually certain events will cause a trip. For example, back pressure can cause the bypass valve response to change or the sensing line pulsation valve to clog. Additionally, electrical system changes can impact the start time of the auxiliary pump. The installation of two stainless steel accumulators can prevent low-pressure trips. Also, it will allow your technicians to inspect the system without taking the accumulator offline.
How Dual Lube Oil System Accumulators Can Help You
Prevent Temporary Disturbances
The primary function of an accumulator is to quickly correct temporary flow disruptions in the lube oil system. Keep in mind that temporary disruptions often last less than five seconds, most often lasting mere microseconds.
Reduce Valve Stem Friction, Noise, and Trips
Excessive valve stem friction contributes to control valve instability and unit trips. Also, if you hear squealing sounds during control valve operation, that may be a sign of low travel conditions. If you have a valve with this characteristic in a bypass function, it can be an alert that the unit has excessive flow. In your mind, you can think of control valves as simple flow meters. You can detect major flow variations by routinely monitoring the valve while the machine is in operation. Furthermore, to guarantee the least amount of valve stem friction, you must stroke control valves as frequently as practical.
Aid with Control Valve Sensing Lines
A common underlying cause of issues with lube oil systems is clogged or closed control valve sensing lines. A bypass valve won’t react to changes in system flow if a dead-ended sensing line is closed at its source, which could result in a unit shutdown. On the other hand, a valve sensing line with a bleed orifice back to the reservoir can have similar issues. Plugging the supply line closes the bypass valve, making it inoperable. This can even force the relief valve in a positive displacement pump system to open.
Dual Accumulator Variables
Because the reliability of your equipment is relying on your lube oil system accumulator, there are many variables to be mindful of. Some of these include:
- If your accumulator has bladders, you must inspect the bladder condition when the unit is turned off.
- If your accumulator is set up with a continuous charge (lines with nitrogen or air from a plant utility system), then you must be aware of diaphragm ruptures. This would introduce charge gas directly into your lube oil system, causing considerable damage and clogging.
- To avoid a pressure drop when bringing an accumulator online, install an orifice bypass line with a globe valve in parallel with the accumulator supply line.
- Properly sizing your accumulator to your needs. The rule of thumb is that accumulator capacity = internal volume – gas volume / liquid volume. This is usually 50% or less of the stated capacity.
- To guarantee that there is no liquid in pneumatic lines or air hydraulic lines, control valve sensing lines should always be supplied with bleeders. The system will typically become unstable when these fluids are present.
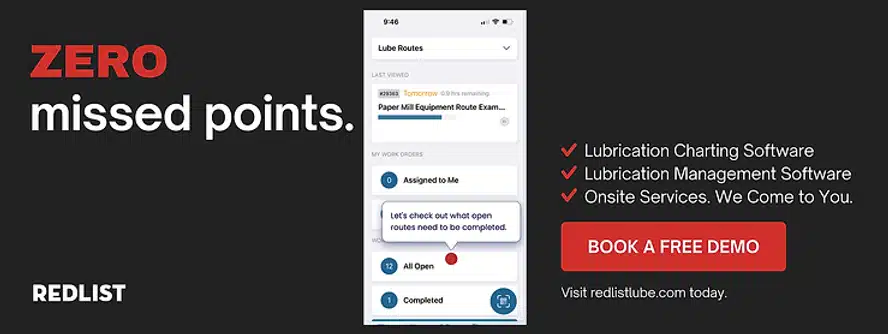
The Bottom Line on Dual Accumulators
Installing dual accumulators is recommended in order to guarantee that one accumulator is always online during monthly checks. Without accumulators, lube oil systems will eventually lead to critical unit trips, which expose you to large downtime losses. Facilities without accumulators in important lube oil systems frequently install them later, after unit trips that can easily justify the modification expenditures.