For managers and technicians involved in maintenance or lubrication, oil contamination is one of the most concerning aspects that can cause operational downtime. Unfortunately, it’s not always clear where oil contamination originates from. By understanding the various sources of contaminants that enter lubrication systems and how to reduce their presence, you can keep your equipment running efficiently and ensure long-term success for your business. In this blog post, we’ll explore these different sources to help you better understand them and create processes so you don’t have to worry about oil contamination impacting performance any longer.
Why You Must Take Preventive Measures Against Oil Contamination
ontaminants, once present in the lubricant, greatly speed up the rate of wear. Furthermore, abrasive wear can set off a domino effect in lubricated machinery. Bearings and other sensitive components can be impacted even by a very small amount of oil contamination. Even particles 5 microns in size or smaller can damage the lubrication coating and significantly increase wear. Therefore, avoiding oil contamination is essential for the long-term performance of your machinery.
How Do Contaminants Enter Lubrication Systems?
Prevention starts with understanding. So, you must comprehend the potential sources of contamination as well as their entry points into the system. Many people mistakenly believe that contaminants are only transferred through ingress points such as breathers, seals, hatches, ports, or other inlets and come only from external sources. In fact, not all oil contamination comes from outside sources, and not all contamination is preventable. We’ll get into that more below.
The 3 Main Sources of Oil Contamination
Contaminants from Human Contact
It is rare to have a lubricating system or equipment that never has human contact. Routine and preventive maintenance tasks mean human interactions are essential for the long-term health of your machine. But, they can also result in the introduction of oil contamination. In certain instances, the fluid reservoir may be exposed to weld spatter, sealants, dirt, or other external components that might cause severe fluid contamination.
However, not all human interaction is bad. Having your maintenance and lubrication technicians follow lubrication best practices can actually help minimize oil contamination. For example, new lubricant is frequently not clean and contains contaminants. So, when a technician performs a top-up or an oil change, they can reduce the introduction of contaminants by filtering the oil first.
Contaminants from Outside Sources
Particles can enter a system from the external environment in numerous ways. In addition to defective seal design or deteriorated seal materials, operational and environmental factors can cause contamination ingress.
The most typical entry points for external oil contamination include:
- As impurities deteriorate the seal materials over time, seals in hydraulic systems leak, both internally and externally.
- Breathers are a possible entry point for dust, silt, moisture, or other contaminants.
- Damaged shaft seal points.
- Gaps in the hatches or ports can serve as an entry point for air and particles even when a system has a breather.
Contaminants from Inside the System
For starters, wear debris from your equipment will build up in the lubricant over time. Additionally, some lubricant components can develop into contaminants as the additive package breaks down, from cross-contamination at oil top-ups, or as they interact with water contamination. These particles may produce oxidation insolubles and sludge.
The most frequent internal oil contamination sources include:
- The thermal breakdown of hydrocarbons can lead to the formation of soot.
- The ingression of water can lead to rust, causing corrosion and the formation of iron oxides.
- Fibers can be produced in the system by aging seals, hoses, filters, or other components, and these fibers can act as a source of contamination.
- Friction between system components can lead to wear and the development of particles and contaminants when the fluid’s lubrication properties deteriorate.
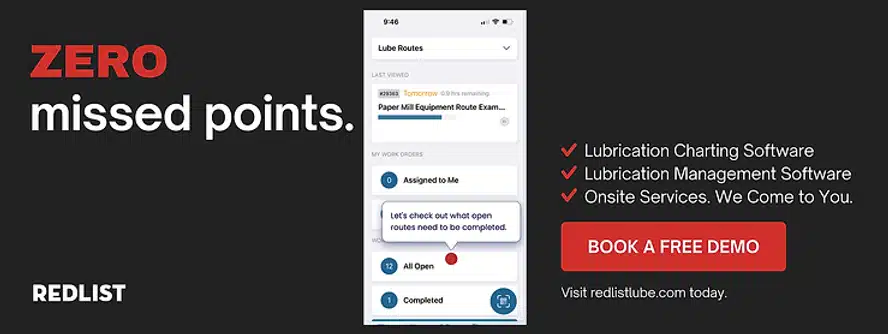
The Most Successful Method of Preventing Contamination
Contamination Control: Prevention and Removal
Both approaches must be taken into account for a successful contamination management strategy because neither is sufficient on its own. However, since the removal of contaminants necessitates machine downtime, preventing contaminants from entering your system is far simpler and less expensive compared to removing them.
Oil Analysis: The Best Protection Against Contamination
How do you know if your prevention measures are working? When do you need to remove contaminants? And, how do you determine when it is time for an oil change? The answer to all of these questions is actually quite straightforward. You do so by developing a comprehensive oil sample and analysis program to monitor the state of the lubricants and the general health of the machine. When you are certain that oil contamination from external particulates is under control, oil analysis and condition monitoring equipment that detects a high level of pollutants may serve as an early warning indication of abnormal wear.