If you’re not familiar with oil analysis, it’s a process of testing oil taken from machinery or other devices to detect and measure the level of contaminants in the oil. This information can help you troubleshoot problems and make decisions about when to retire equipment. But, how does oil analysis test for contamination in the first place? Let’s take a closer look.
What is Oil Analysis?
Oil analysis is the process of monitoring your lubricant’s condition, contamination, and component wear. You can perform some level of oil analysis in-house with in-line oil sensors. These sensors will provide a constant flow of data on the condition of your lubricant. However, they don’t offer the most in-depth results. If you want a more detailed analysis, you have to send oil samples to a lab for testing. There are several different tests that make up an oil analysis program. Most oil analysis labs offer tests individually or as part of a test package. This allows you to select the appropriate tests based on the type of lubricant, machinery failure modes, and common contaminants to monitor. Furthermore, many companies choose asset-specific tests, while others may go with a one-size-fits-all test package or asset-specific only for their most vital assets.
Benefits of Oil Analysis
Before you invest time and money into a regular testing program, it is important to understand all the benefits and your return on investment. When combined with a holistic approach to your lubrication management, oil analysis can help:
- Minimize the impact of contamination on your assets.
- Reduce unplanned downtime with early detection of problems and contamination.
- Lower maintenance costs by improving lubricant condition and extending its useful life.
- Increase equipment reliability by reducing component wear.
- Provide guidance for your preventive maintenance plan.
- Support the continuous improvement of your lubrication management with real asset health data.
The Consequences of Contaminated Lubricant
Early detection and minimizing the impact of contamination is a major part of oil analysis. Common contaminants include water, coolant, fuel, other lubricants, and abrasives such as dirt, dust, and wear particles. The problem with contamination is that it reduces the condition of your lubricant, which slowly but surely reduces its ability to do its job. Also, as your lubricant loses its effectiveness, it can affect the condition and function of your assets, leading to equipment breakdown.
Before investing in tests or sensors, it is important to take the necessary steps to optimize your lubrication management plan. If you’re not proactively implementing lubrication best practices and working to prevent contamination, then you won’t reap the full benefit of oil analysis. Basically, starting with oil analysis is like running before you learn to walk. First, “learn to walk” by optimizing your lubricant storage, filtering new lubricants before use, and charting and sticking to your lubrication routes. Then, you can “run” with an oil analysis program to identify the ongoing steps to make your lubrication management plan world-class.
What are the Different Oil Analysis Tests?
Generally speaking, you can group the long list of available oil analysis tests into three categories.
Condition of Lubricant Tests
- ICP (Inductively Coupled Plasma) Spectrometry
- Viscosity
- Oxidation
- Nitration
- Acid Number
- Base Number
- Varnish Potential
- RULER (Remaining Useful Life) Test
- RPVOT (Rotating Pressure Vessel Oxidation Test)
- Foam Test
- Demulsibility Test
- Rust Test
Contamination Tests
- ICP Spectrometry
- Percent Water by KF (Karl Fischer)
- ISO Particle Count
- OPC (Optical Particle Classification) Particle Count
- Soot Percentage
- Fuel Dilution Percentage
- Glycol Percentage
Component Wear Tests
- ICP Spectrometry
- Total Magnetic Iron
- Sediment with Photo
- Analytical Ferrography
- XRF (X-Ray Fluorescence) Spectrometry
- Filter Debris Analysis
- SEM (Scanning Electron Microscopy) Analysis
How to Test for the Most Common Contaminants
Abrasives
Abrasives like dirt, dust, and wear particles can cause the most damage to your equipment. ICP spectrometry, also known as ICP spectroscopy, is a great test for this purpose. It involves measuring concentration levels to determine the presence of contaminants, wear, and additive elements. Particle counting tests are also helpful. However, basic particle counting tests may not differentiate between dirt particles and wear particles. This is when it is helpful to understand the failure modes of your asset and what you should be testing for. For example, if an asset’s wear particles are not magnetic, a ferrous debris test using a magnet will not be effective or necessary.
Water
Water dilutes your lubricant and can cause rust, corrosion, and increased component wear. An oil analysis lab may perform FTIR (Fourier Transform Infrared) spectroscopy. Then, the lab would report the presence of water as a percentage volume or in parts per million (ppm).
Coolant
Oil analysis tests that provide an elemental analysis can identify coolant contamination. If potassium, sodium, or boron are present, that is an indication of coolant in your lubricant.
Fuel
With an asset that may be prone to fuel dilution of your lubricant, a gas chromatography (GC) test would be useful. It vaporizes the lubricant and measures what is released. This determines whether fuel is present or not.
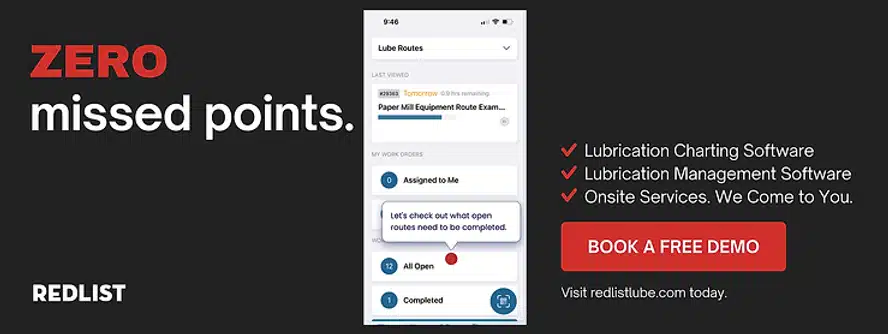
A Partner for Your Oil Analysis Program
Oil analysis can be very complex and time-consuming, but there are many experienced professionals to guide you along the way. If you aren’t sure about what oil analysis tests are appropriate for your assets, talk to your lab or a lubrication engineer. Additionally, if you’re reading this and considering oil analysis before making improvements to your lubrication management program, check out our other resources. There are many best practices and software support for your lubrication charting. Then, you can come back to oil analysis as a strategy for continuous improvement.