One of the most important aspects of lubrication is making sure that the lubricants used are free from contaminants. Oil contamination can severely damage equipment, so it’s important to take steps to prevent them from entering the system in the first place. In this blog post, we’ll discuss some of the ways you can prevent contaminants from entering your lubricating oils.
Why is it Vital to Prevent Oil Contamination?
Oil contamination can lead to serious problems in industry operations. Contaminants like dirt and water can degrade oil’s ability to perform. This in turn can reduce the efficiency of engines and machines, decreasing both their performance and life span. In addition, oil contaminated by foreign particles can clog valves, pumps, and filters, resulting in extensive damage within a system. Therefore, industrial operations need to prevent oil contaminants from entering the system before they become a problem. By doing so, you may avoid costly repairs and extended downtime.
Not All Oil Contamination is Preventable
One of the primary goals of lubrication is for lubricant to clean the systems you use it in. That includes getting rid of any contamination that may have entered from the outside or produced inside the machinery. As a result, the oil will lose some of its properties due to contamination. It is an inherent and unavoidable part of carrying out this crucial task. However, for the oil to be able to handle this function of cleaning the systems for the duration of its useful life, it is crucial to keep its levels of contamination as low as possible.
When it comes to contamination, lubricants are vulnerable at all points in the product’s life cycle, from manufacturing to disposal. Even though one of oil’s functions is to collect contaminants, excessive contamination can overwhelm its ability to do so. This can affect the oil’s useful life, the machine’s proper operation, and even increase the generation of wear particles. Therefore, it is equally important to prevent external contamination as it is to address unavoidable internal contamination.
Tips for Minimizing Oil Contamination
Examine Your Lubricant Selection
Considering that oil contamination is a threat at every stage, where do you begin with treating it? Start with choosing the best lubricant for your application. First, get the right kind of oil for each piece of equipment. But, also consider how well the oil handles your most common contaminants.
Additionally, you must remember that brand-new oil is not clean oil. Water or dust can enter during the mixing of the lubricant’s various components, which occurs during the production process. This type of oil contamination is common, so it’s crucial to be aware of the possibility. Once choosing the right oil, verify the new oil’s color and test some of its fundamental characteristics as soon as it arrives. If the oil does not meet the expected quality standards, the timing is crucial to be able to claim the manufacturer’s guarantee.
Follow Lubricant Storage Best Practices
Water or other contaminants could enter your lubricants due to their storage conditions. This occurs when oil drum caps expand and contract during storage, allowing water, dirt, and dust to penetrate through the gaps. As much as possible, store your lubricants in a dry, clean space that is protected from extreme weather conditions. However, there are measures you can take to easily prevent or minimize external contamination, even when logistical difficulties make it impossible to store oil drums in ideal storage conditions. It is possible, for example, to store drums leaning slightly instead of vertically to prevent water from collecting on the caps.
Keep Your Lubrication Tools Clean
In most cases, tools like hoses, pumps, or guns are employed to insert the lubricant rather than pouring it straight from the barrel. The cleanliness of all the components in this procedure is essential to prevent contamination. While it is great to have the proper specialized tools for each type of oil, you must also maintain meticulous cleanliness. If waste oil is left behind after use, it attracts dust and dirt. And, if it is not cleaned properly, it would be introduced into the equipment during the next use.
Minimize Contamination with Oil Changes
Just as you can introduce oil contamination when topping up oil, you can do the same when changing oil. To prevent dust from entering the machine, filtering the oil is typically a standard practice. But, an often overlooked part of the procedure is the conditions under which you add the new oil. At the time of replacement, the used oil has a high degree of oxidation, which negatively affects the useful life of the new oil. Therefore, you must extract as much of the old oil as possible before adding the new oil. Additionally, to avoid problems like faster oxidation and the production of solid waste that can clog filtering systems, you need to evaluate the compatibility of the fluids when the oil is changed and a new type is employed.
Implement Regular Lubricant Analysis
As was already said, one of the roles of oil in the process is to “pull” particle contaminants formed or introduced inside the machine out of the system to remove contamination. The existence of these particles may correspond to wear patterns that are typical during the operation, depending on their number and type. On the other side, they might be a sign of a machine that could be critically failing. Lubricant analysis and other condition monitoring techniques are crucial to gain clarity around your types of oil contamination and wear patterns.
With that data, you can make better decisions on preventive measures to improve asset condition. Also, it can even reduce cleaning and filtration costs by enabling you to optimize your systems according to your specific contaminating particles. You will also benefit from the prevention or reduction of downtime, as the data can act as an early diagnosis of a machine malfunction.
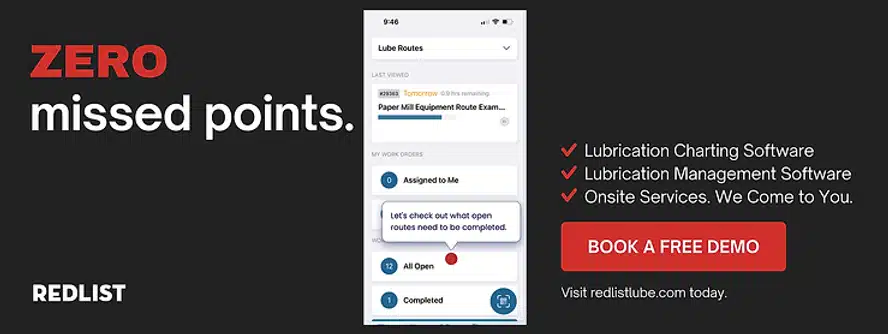
Daily Efforts Against Oil Contamination Make a Difference
Oil contamination can have serious consequences for equipment, including decreased performance, shortened life spans, and even failure. It is therefore vital to take measures to prevent oil contamination wherever possible. While not all forms of contamination are avoidable, there are a number of steps you can take to minimize the risk. By examining your lubricant selection and storage practices, keeping your tools clean, and implementing regular lubricant analysis, you can greatly reduce the likelihood of oil-related failures. Even small daily efforts make a big difference in preventing costly problems down the road.