Maintaining your equipment is essential for keeping your business running smoothly. If you want your assets to run like well-oiled machines, an oil analysis program is critical to your maintenance goals. By regularly testing your oil, you can catch small problems before they turn into big ones. This not only saves you time and money but also helps keep your equipment running safely and efficiently. In this blog post, we’ll explain oil analysis, the steps to an oil analysis program, some benefits, and success tips.
What is an Oil Analysis Program?
Oil analysis involves testing an oil sample to monitor contamination, condition, and component wear. However, a single oil test or oil analysis at irregular intervals will give you information, but you won’t have the full visibility that an oil analysis program provides. An oil analysis program means you’re performing oil analysis on a regular basis, as well as implementing corrective action. The three main things that oil analysis tests for are:
- The condition of your oil
- The types and levels of oil contamination
- The extent of component wear
Oil Analysis Program Benefits
Reduce Unplanned Downtime
As with any maintenance strategy, reducing unplanned downtime is a major benefit. Unplanned downtime means you’re spending money on an unexpected repair and you’re losing valuable production time. An oil analysis program helps reduce this by catching small problems early on. Early detection allows you to prevent small issues from becoming bigger and more expensive issues down the road. A perfect example is the cause of failure with hydraulic oils. On average, 80% of failures with assets using hydraulic oil are caused by oil contamination. An oil analysis program would catch that contamination early before it results in machine failure. Also, your oil analysis program will help you recognize trends that will help you better plan your preventive or routine maintenance.
Lower Maintenance Costs
An effective oil analysis program can help you save money on maintenance costs in the long run. Not only by preventing costly repairs and downtime, but also by extending the life of your oil and equipment. Oil analysis empowers your lubrication program by giving you data. Instead of changing oil at the OEM (original equipment manufacturer) recommended time, you can test your oil and change it based on your actual oil condition. This is especially beneficial for machines with high volumes of oil! You can lower your lubrication cost with the confidence that your asset is still being taken care of.
Improve Equipment Reliability
An MIT (the Massachusetts Institute of Technology) study discovered that machine failure is caused by surface degradation 70% of the time. Additionally, the study found that 79% of the surface wear can be reduced with proper lubrication to lower mechanical wear. While proper lubrication starts with simply having a lubrication plan, there is more to it. An oil analysis program is necessary to make sure your lubrication isn’t introducing more contaminants and increasing the wear rate of your asset. It’s an essential step to protect your equipment, ensure safe and reliable operation, and extend the life of your components.
Track Progress for Continuous Improvement
Your lubrication management plan is not a set it and forget it strategy. You absolutely need to be tracking progress and monitoring the impact of your plan and any corrective actions you implement. Your oil analysis program will give you real data to monitor, spot trends or red flags, and make the necessary adjustments. Furthermore, this data along with your maintenance metrics are a useful tool to demonstrate the value of your lubrication and oil analysis costs in the maintenance budget.
The Steps of an Oil Analysis Program
To get the most out of your oil analysis program, make sure you have a plan for all five of these steps:
- Collect – Sample your oil on a regular basis and follow best practices to collect a clean sample.
- Test – In-line oil analysis sensors can provide a regular feed of data, but lab testing will give you more in-depth results.
- Interpret – If your test results end up in a pile of papers, they aren’t doing you any good. Assign a team member to read the results and make note of any red flags.
- Identify – Determine corrective actions you can take based on the oil analysis red flags. Sometimes this requires research or a third-party expert who can explain why and where your contaminant levels are coming from.
- Correct – Simply put, do the work. Change the oil, improve your best practices, restore oil condition, or whatever else is needed.
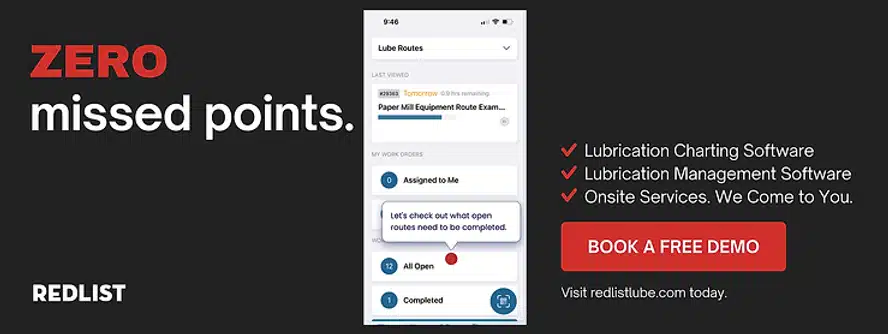
What is the Real Value of an Oil Analysis Program?
If you test your oil but don’t do steps three through five above, then you’re wasting your money. Testing your oil alone won’t improve the condition or purity of your oil. The real value of an oil analysis program comes from the action you take in response to the data. Oil tests give you insight into something you had no visibility into before, so put that to work for you. For example, a doctor may test your blood and diagnose you with high cholesterol. But, just getting the blood test won’t lower your cholesterol. You have to take action, whether that is with medicine, supplements, or changing your eating habits. The same goes for your oil analysis program. Take the data, make a plan, and reap the benefits of your investment in an oil analysis program. Additionally, there are plenty of industry professionals, including us, who would be happy to help you on your way to a successful lubrication management program.