If you’re like most business owners or maintenance managers, you’re always looking for ways to save money and cut costs. Unfortunately, many people overlook one of the biggest sources of potential savings: oil contamination prevention.
By implementing a few simple best practices, you can avoid costly machine engine repairs and keep your business running smoothly. In this blog post, we’ll discuss the dangers of oil contamination and the most common contaminants you’ll find. Read on to learn more!
Why is Oil Contamination Bad?
As it works, oil sometimes becomes contaminated. Contamination is bad for your machinery. It eventually lowers the oil’s efficacy. As your oil is less effective, it impacts the condition and function of your assets. This can lead to equipment breakdown, costly unplanned downtime, or even a critical machine failure.
Also, oil contamination can greatly increase maintenance costs. For example, if you buy premium oil but don’t keep it clean, you will end up buying more oil. This is due to the increased need for oil changes and breakdowns. Understanding and preventing oil contamination as much as possible just continues to improve your lubrication management plan and asset reliability.
Causes of Oil Contamination
Lubricant or oil contamination can come from either external factors or internal reactions or breakdown. Additionally, oil contamination can happen before you receive the oil! Tanker trucks, storage containers, dispensing, and even storage conditions can introduce contaminants to the oil. If you don’t filter, you will likely add these contaminants to your assets.
What Are the Main Types of Oil Contamination?
External Contamination
The first type of oil contamination is from external factors you can more easily control. They include things like dirt, dust, water, and cross-contamination with other lubricants. If you keep your machine or storage containers in a bad place, your oil has a greater risk of contamination.
For example, a space with high humidity is bad. So is one with extreme temperature changes or a lot of dust in the air. These conditions are bad for your oil. Simple actions, like changing the oil or sampling, can introduce these contaminants to your machine.
If you utilize dispensing containers or funnels that haven’t been well cleaned before use. Or if they are used for multiple different lubricants. You can cause oil contamination. If the oils get contaminated with other lubricants, they may react badly. They can make gunk that clogs your machine and causes breakdown.
Internal Contamination
Next, the second type of oil contamination is from internal factors. This oil contamination may be metal particles from surface damage. It may be contaminants from machine engine use. Or, it may be the result of oxidation or loss of additives over time. For example, the oil in a machine engine will be contaminated with soot from engine operation. Another example is water contamination from water-cooled equipment.
Typically, you cannot prevent or avoid internal oil contamination, as it’s a result of operating your machine. However, you can monitor contaminant levels. Do this to make sure you change the oil before the contaminants build up enough to hurt your machinery.
The Most Common Oil Contaminants
Abrasives
Out of all the possible oil contaminants, abrasives have the biggest impact on your assets. Abrasive oil contaminants include dust, dirt, and metal particles from engine wear. Dust and dirt can find their way into your oil at many points in the transport, storage, and dispensing process.
However, they can also come from unfiltered air entering the engine. The metal particles in oil come from two sources. First, normal engine usage creates wear on metal components. Second, abrasive oil contaminants can add wear. They can raise wear above the normal level and add more particles to your oil.
Water
On average, water is the second most common cause of oil contamination. It may be a byproduct of engine combustion at lower temperatures or from humidity during storage. Water in your oil can increase wear and cause corrosion of components. Also, it encourages the production of acidic gases that further increase corrosion.
Fuel
Another term for fuel contamination is fuel dilution. This means that fuel finds its way into your oil, diluting it. This decreases the oil film strength and actually leads to higher oil consumption, which impacts your maintenance budget. Furthermore, fuel dilution lowers the protective properties of oil and its additives by decreasing oil viscosity. That means your oil won’t provide as much protection from corrosion, further increasing component wear.
Coolant
If you have coolant in your oil, that’s a sign of other engine problems to address. A blown head gasket can often result in coolant contaminating your oil. Similar to fuel dilution, this causes oil viscosity to drop. In fact, the oil may thicken to the point of turning into sludge that can damage engine components.
The Ripple Effect of Oil Contamination on Business Operations
Oil contamination is not a mere maintenance hiccup; it’s a critical operational concern. Contaminated oil can lead to increased wear, energy inefficiency, equipment failure, and costly unplanned downtime, all of which can erode the profitability and reliability of businesses.
Prevent Oil Contamination with a Lubrication Management Software from Redlist
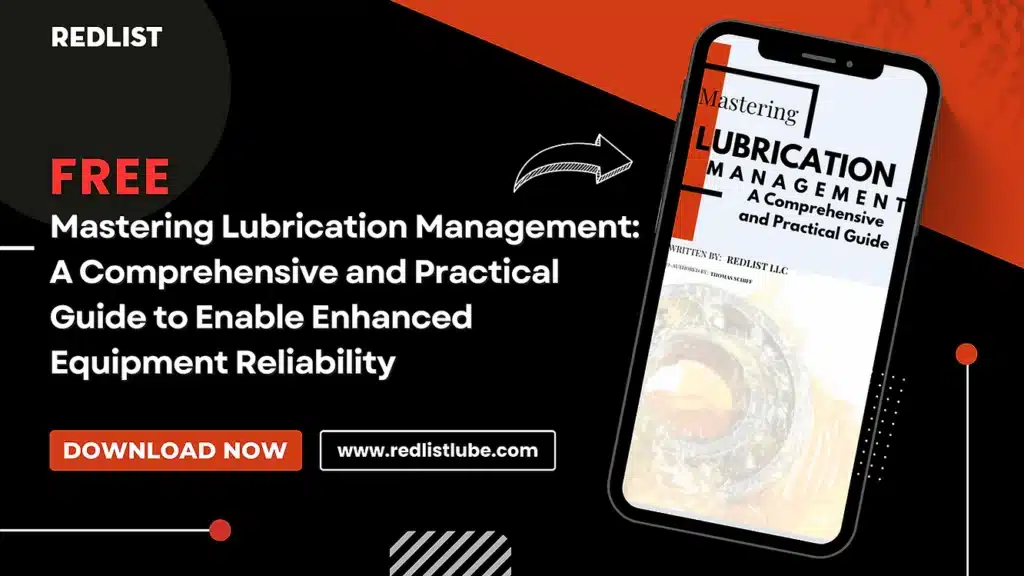
Redlist’s lubrication management software serves as a bulwark against the repercussions of oil contamination. By integrating Redlist into their maintenance strategy, businesses can:
- Detect and Diagnose Contamination Early: Utilize real-time monitoring and analysis to identify contamination signatures before they escalate.
- Tailor Lubrication Practices: Leverage data-driven insights to refine lubrication schedules and practices, ensuring optimal oil health.
- Streamline Contamination Control: Implement systemic contamination control measures based on actionable intelligence from the software.
- Enhance Preventive Maintenance: Transition from reactive to proactive maintenance, bolstering equipment longevity and reliability.
Growth Through Informed Lubrication Strategies
With Redlist, companies can transform the challenge of oil contamination into an opportunity for optimization. Our technology enables users to not just manage but excel in lubrication practices, fostering an ecosystem where efficiency and growth go hand in hand.
Empower Your Operations: Schedule Your Free Demo Today
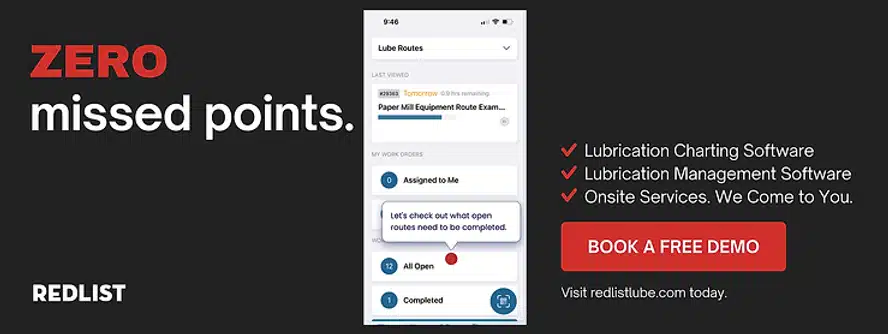
Don’t let oil contamination undermine your operational success. Discover the power of proactive lubrication management with Redlist. Book your free demo today and take a definitive step towards operational resilience and excellence.