If you’re a maintenance manager or technician, then you likely know how important it is to lubricate your equipment. One of the most common tools for lubricating machines is the grease gun. This blog post will cover some grease gun tips and tricks for maintaining, cleaning, storing, and using a grease gun. So if you’re ready to learn more about grease guns, keep reading!
Why are Grease Guns so Important?
There are many lubrication tasks you can perform by hand. But, a grease gun will make it easier, cleaner, and faster for your lubrication technicians. They are especially important when lubricating machinery or parts in tight spaces. Manual lubrication without a grease gun can be messy. It can even waste more lubricant, increasing your maintenance costs. Using a grease gun provides more control over the amount of lubricant you apply to equipment. Furthermore, maintaining and cleaning your grease guns will keep your lubricants clean. Lubricant contamination is a major issue! It can cause increased component wear and equipment breakdown. So, preventing contamination at every stage is critical.
Storage
Hang your clean grease gun horizontally in a clean, fireproof cabinet.
You should always disengage the grease gun plunger and store it horizontally. This will extend the life of your grease gun and any lubricant if there is a tube inside. If you don’t disengage the plunger or store it vertically, two things can happen. Your grease gun will wear out faster and pump an inconsistent amount of lubricant. This is because improper storage overexerts the spring and plunger. Additionally, the impact of storage on lubricant quality is about the even distribution of oil and thickener in the tube. Otherwise, if the base oil separates and the tube is vertical, you will end up pumping only thickener the next time you use the grease gun.
Control the temperature and humidity of your lube room.
While this doesn’t create a direct impact on your grease gun, you will probably store your grease guns in your lube room. You must keep the lube room cool and dry to:
- Extend the life of your lubricants
- Prevent oxidation
- Avoid oil contamination
If you don’t maintain a good storage environment, your lubricants won’t reach their expected shelf life.
Start a label or color-coded system for lubricants and grease guns.
Not all lubricants work with each other or with every machine. That’s why it is crucial to label or color-code your:
- Lubricants
- Grease guns
- Containers
- Fittings
- Even your assets
This prevents cross-contamination of lubricants. Also, it ensures technicians use the right lubricant every time.
Refill
Inspect your grease gun before every use.
The last thing you want is to clean and refill your grease gun, only to discover that it doesn’t work. So, inspect all parts before you use them to save yourself that time.
Clean the plunger and exterior of the grease gun before refilling.
This is especially important if you buy your lubricant in kegs. If your grease gun or plunger is dirty when you refill from the keg, you run the risk of adding contaminants to your lubricant. Also, always clean with a lint-free cloth or towel. Lint left behind is as much of a contaminant as the dirt or debris you’re wiping off.
When refilling from bulk storage, close the lid immediately.
If you’re not actively refilling your grease gun, your lubricant should not be open to the environment. With kegs, that means closing the lid immediately. This is a vital best practice to keep your lubricants clean.
Usage
Calibrate each individual grease gun before first use and every 12 months.
Your lubrication management should run on precise amounts and frequencies. So, your technicians need to know the volume per pump of each grease gun. You can’t assume that all grease guns pump the same volume, especially if they haven’t always been stored properly. To calibrate, you’ll need a postal scale that you can gradually pump ten strokes of lubricant onto. Then, take the weight and divide it by ten. That is your average volume per pump, and you should keep that measurement handy. The best way to do this is to place a label on the grease gun with the date of calibration and the volume per pump.
Don’t use your grease guns interchangeably.
For the same reasons that you need a label or color-coded system, you should not use a grease gun with many different lubricants. This can have a negative impact on your assets and the function of your lubricants.
Pump slowly when lubricating.
If you pump quickly, you are less likely to notice unusual or significant back pressure. This is an important signal of either a blockage or over-lubrication. A good rule of thumb is to take three to five seconds with every pump. Also, never force lubricant into equipment if you feel back pressure! Grease guns can deliver pressure up to 15,000 psi (pounds per square inch). Continuing to pump when back pressure is present can break seals and cause a much bigger problem than a simple lubricant blockage.
Grease Gun Tips: Cleaning
Wipe all fittings and components with a clean cloth.
Using a lint-free cloth, start with wiping the grease gun fittings, followed by the rest of the parts.
Avoid setting your grease gun down in dirty areas.
Spaces with a large amount of dust or debris in the air will get your clean grease gun dirty. Avoid dirty or dusty surfaces. But, if you can’t avoid it, check your grease gun immediately before use for one more cleaning. The ultimate priority is to prevent the introduction of contaminants to your equipment.
Clean with water and an anti-grease mixture.
Grease guns are built for use with grease and oil, but that means they tend to get messy. A dry cloth or water by itself won’t clean your grease gun. So, a mixture of water and an anti-grease solution is necessary for cleaning.
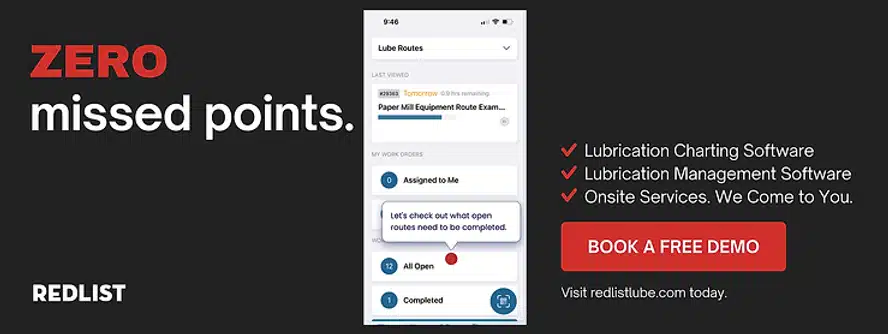
An Essential Piece of Lubrication Management
Grease guns are a valuable and necessary tool for any lubrication technician. They provide precision lubrication to critical equipment, which keeps the machines running smoothly. Better lubrication means higher production, reduced downtime, lower wear rates for components, and better asset health and reliability. Treating these lubrication tools with care will help you maintain their effectiveness while keeping your lubricants clean as well.