If you’re responsible for the maintenance of machinery in your business, then you know how important it is to keep all the parts well-greased. But, what are the best practices for greasing bearings? In this blog post, we’ll discuss some tips and tricks for getting the job done right.
Why is Properly Greasing Bearings Important?
Bearings are an essential part of many machines and equipment. They help reduce wear and tear on the components and ensure that the machine operates smoothly. So, it is important to grease bearings regularly in order to keep them in good condition. This helps to protect surfaces from corrosion, seal against contaminants, and create a barrier between rolling contact and sliding surfaces. Lubrication also helps to provide heat transference, which is important for preventing bearing damage. Bearings that are properly lubricated will last longer and perform more efficiently than those that are not. As a result, greasing bearings on a regular basis is critical for maintaining the lifespan and performance of the bearings and your equipment.
You cannot overlook the importance of proper lubrication. Proper lubrication has been proven time and again to have a significant impact on bearing life. In fact, it’s an industry-wide understanding that at least 80% of bearing failures are linked to lubrication or contamination issues. Not enough lubricant and your bearings will experience higher friction and heat, leading to increased component wear, yet too much lubricant is also a problem. Additionally, contaminated lubricant will cause more friction between machine components over time. More friction from contaminants like dirt and debris will also increase component wear, and may lead to premature equipment failure.
Best Practices for Greasing Bearings
You understand the importance of greasing bearings, but is it as simple as using whatever lubricant you have available and pumping it in until you see grease overflowing somewhere? No. Actually, for the best results, there are many things to take into consideration.
Know Your Bearings
For starters, different bearings have a varied level of sensitivity to the type and amount of lubricant used. So, you should get to know your bearings and look into the manufacturer’s recommendations for the type, amount, and frequency of lubrication. For example, shielded bearings will be very sensitive to over-lubrication because they seal the lubricant in to keep dirt out. Additionally, rolling element bearings tend to be more sensitive to over-lubrication, especially compared to journal bearings.
Check Your Operating Temperature Before Choosing Your Lubricant
When greasing bearings, it is important to choose the best oil formulation for the application. You have to consider many factors, including speed, operating temperature, lubrication dispersal method, and potential environmental contaminants. All of those factors are important, but operating temperature is key! Operating temperature helps you determine the best viscosity of the oil or grease. If your viscosity is too high, when the temperature decreases, the lubricant will thicken. This causes an increase in torque and a reduction in operating speed. Alternatively, if your viscosity is too low, you won’t achieve a sufficient lube film layer and may end up with metal-to-metal contact. Therefore, it is crucial to select the appropriate oil formulation for each greasing job.
Don’t Over-Lubricate
When greasing bearings, it is important to use the appropriate amount of grease. Too little grease can cause the bearing to run dry, leading to metal-on-metal contact and premature wear. Conversely, too much grease can lead to problems such as heat build-up and leakages. This is the case with over-lubrication of shielded bearings. When the grease is sealed in and there is too much of it, the bearing has to work harder to function. This typically increases heat and pressure, changes the bearing fit, potentially breaks the seal allowing dirt in, and leads to unnecessary wear and potential breakdown.
Create a Lubrication Schedule
A greasing schedule should be put in place and adhered to. This will ensure that you apply an adequate amount of grease to the bearing surfaces on a regular basis. For example, you will need to grease bearings that operate in hot environments or carry heavy loads more often than those that operate in cooler environments or carry lighter loads. In addition, bearings in harsh environments will require more attention. Harsh environments include large amounts of dust and dirt, water, extreme vibration, and operating temperatures over 150 degrees Fahrenheit.
Furthermore, the type of oil used can also affect greasing frequency. Oils with lower viscosities will require more frequent greasing than oils with higher viscosities. Unsealed bearings may need lubrication with every use, while you may only need to grease enclosed bearings at a moderate operating temperature once per year. Ultimately, the goal is to maintain an adequate lubricant film to prevent metal-to-metal contact and minimize wear.
Prevent Lubricant Contamination
When greasing bearings, it is important to use clean lubricant. The human eye can only see particles down to 40 microns. However, particles smaller than 40 microns can cause excessive bearing wear by getting between the lubricated surfaces. Filtering your lubricant and storing it properly will help to ensure that it is clean. Also, using grease zerk caps will keep dust and dirt off the zerk between greasings. However, dust and dirt particles aren’t the only contaminants to avoid. Proper storage will reduce the presence of water in your lubricant. Additionally, sticking to the same lubricant when greasing bearings will ensure you don’t cross-contaminate with incompatible lubricants. Not all oils and greases are compatible, which means you can unknowingly cause a reaction that accelerates your bearing wear rate. By taking preventive measures, you can help to extend the life of your bearings.
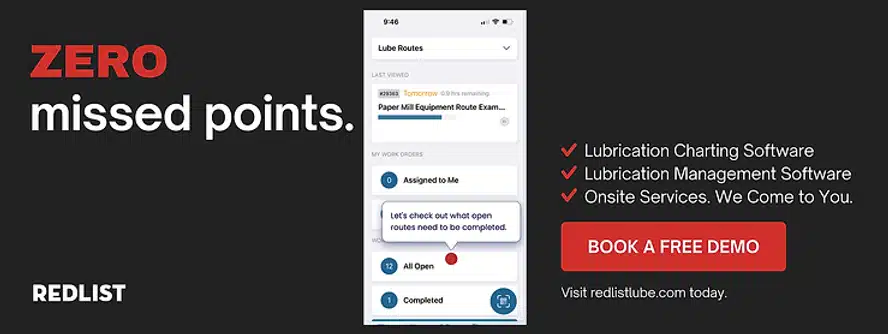
Greasing Bearings is Essential to Lubrication Management
Greasing bearings is a key way to lengthen their lifespan, prevent unscheduled downtime, and improve the health and reliability of your assets. The greasing process involves adding the right amount of fresh grease to clean, dry bearings. When done correctly, greasing can help protect bearings from contaminants, like water and dirt, that can cause wear and tear. By taking these factors into account, you can help ensure that your bearings receive the proper care and maintenance they need to function properly for years to come.