Proper lubrication is essential for the smooth operation of machinery, but manual lubrication can be a challenging task for many companies. Inefficient manual lubrication practices can result in machine failures, costly repairs, and production downtime. To address these issues, many companies are turning to lubrication management software as a solution. In this blog post, we will explore the benefits of using lubrication management software to solve manual lubrication issues and how it can help companies optimize their lubrication practices for improved equipment performance and reduced costs.
What is the Purpose of Lubrication Management?
Lubricating components that are sensitive to wear and tear ensures the flawless function of machines. When applied, oil or grease protects these components or machine parts by:
- Reducing friction or rubbing together of parts that result in wear.
- Absorbing shock and reducing impact when parts constantly move together.
- Protecting from corrosion by forming a thin layer over surfaces.
- Isolating from contamination that promotes surface damage.
- Flushing or washing out contaminants.
Ultimately, the goal of lubrication management is to delay or prevent failure, thus decreasing downtime, reducing facility costs, and increasing productivity.
The Trouble with Manual Lubrication
Traditionally, applying lubrication means using a grease gun and manually placing it on the machine’s components. Facility managers and operators used to consider manual lubrication adequate for maintaining their machines.
But in reality, manual lubrication systems cannot ensure that the correct amount of lubricant is applied at the proper time and location. Manual lubrication comes with risks that, if unaddressed, can result in more harm to the machine than good.
Risks Associated with Manual Lubrication
Maintenance programs using manual lubrication are rarely effective in achieving the purposes of lubrication. Manual lubrication has a high probability of failing through the following ways:
1. Downtime and Inefficient Implementation
Lubrication management aims to decrease downtime due to machine failure. But manual lubrication defeats this purpose because when you manually apply lubricants, you render the machine unusable. You would need to lock out your machine for the safety of the technician applying lubrication. In some cases, manual lubrication even requires stopping an entire operation.
In addition, manual lubrication is more expensive to implement because it requires more resources in terms of labor and materials. Manual lubrication also requires materials and tools preparation, breakdown and reinstallation of machine components, post-lubrication cleaning and startup, and other time-consuming steps. If your machines require regular lubrication, manual lubrication can get very expensive over time.
2. Insufficient or Excessive Lubrication
Manual lubrication is prone to applying inaccurate amounts of lubricant. Insufficient lubrication leads to excessive heating, which causes irreparable damage to the sensitive machine components.
Furthermore, it is a common practice of manual lubrication to apply grease or oil until the lubricant visibly leaks out of the machine. This practice results in excessive lubrication, which poses another type of threat to the healthy functioning of machines. Excessive lubrication promotes the increase of pressure and excessive heating. The leaking lubricants also harbor impurities and promote contamination.
Either way, insufficient and excessive lubrication can lead to high costs. Insufficient lubrication requires frequent reapplication, and excessive lubrication wastes a good amount of lubricant. Add these costs to the higher costs of maintenance and downtime and the loss in productivity resulting from these conditions.
3. Human Error and Safety
Manual lubrication depends on humans who perform these tasks. And with proper training and hours of experience, technicians are perfectly capable of performing manual lubrication tasks.
On the other hand, manual lubrication involves dangerous tasks, and it risks the health and safety of a human being. Lubricants are toxic, and exposure to them, chronic or acute, can cause a degree of damage to the health of technicians. Climbing into, under, or through machines also place technicians at risk for accidents and physical harm.
In addition, humans are easily affected by factors such as illness, hunger or thirst, mental or emotional stress, etc. Technicians experiencing these factors can fail to perform their duties or complete their tasks satisfactorily.
Automatic Lubrication is the Solution
Due to the above risks, many facilities are automating their application of lubricants. Many types and forms of modern lubricating systems do the efficient job of lubricating machines without the above risks involved.
Automatic lubrication systems provide continuous lubrication at accurate levels without the need to lock out a machine or stop operations. Humans are still involved in the lubrication process but only operate or initiate, monitor, and supervise the process. They do not need to access the actual lubrication tools or parts that need oiling or greasing. You and your team can monitor and oversee lubrication using lubrication management software. Automatic lubrication also eliminates unnecessary exposure to contamination.
But automatic lubrication is not foolproof; it also comes with a set of risks. Like all machines, automatic lubricating systems can also fail. Proper inspection, monitoring, and maintenance are required to keep them working flawlessly. It is also essential to regularly inspect and monitor the parts that are lubricated by these automatic systems. However, you can set up automated processes for these recurring maintenance and inspection tasks in your lubrication management software.
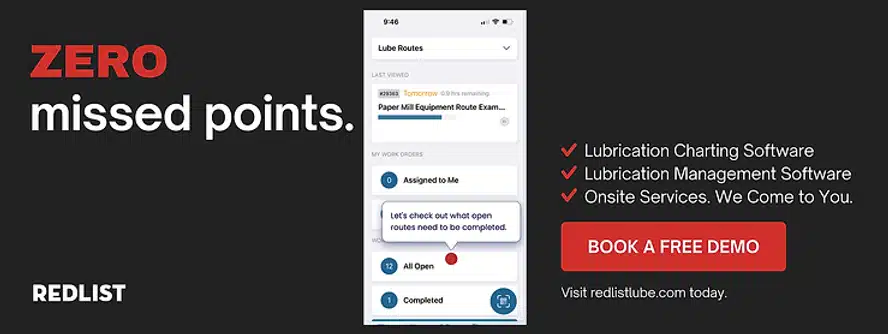
Lubrication Management Software for Risk-Free Lubrication
Simply automating your lubrication is not a guarantee of success. Automatic lubrication systems are only successful with suitable lubricants, regular and effective inspection, and optimized use.
Employing lubrication management software like Redlist is one of the best ways for you to optimize the use of your automatic lubricating systems. Redlist’s automated inspection and monitoring allow easy and real-time processing of data. Also, Redlist’s fast recording and zero-paper process lets you cover more inspections, saving labor costs and reducing downtime. Redlist is intuitive and user-friendly, so technicians can use the lubrication management software instantly with minimal training. Furthermore, Redlist’s computerized analysis and reporting provide valuable insights into the health and lubrication status of machines.
An automated lubrication system is an excellent solution to the risks that come with manual lubrication. And for the risks associated with automatic lubrication, you have Redlist.