While bearings are a small and relatively inexpensive component, their impact on the bottom line can be substantial. Bearing failures often occur without warning, leading to unplanned downtime while you troubleshoot the issue and repair the equipment. What makes it more complicated is that lubrication management is one of the key preventive measures for bearing failure. But, bad lubrication can also be the cause of bearing failure! So, it is important to understand this and other common causes of bearing failure in order to prevent them.
1. Lubrication Failure
The first thing to check after a bearing failure is your lubrication. Improper lubrication is at the root of 43% of mechanical failures, 70% of equipment failures, and 50% of roller bearing damage. However, bearing failures occur because of many different lubrication issues, not simply under lubrication. Your problem may be:
- Under lubrication – Leads to metal-on-metal contact and increased wear.
- Over lubrication – Increases friction, causing temperatures to increase.
- Inadequate viscosity at operating temperatures – Leads to insufficient oil film and the potential for metal-on-metal contact.
- Using the wrong or incompatible lubricants – Has the potential to cause a reaction that accelerates your bearing wear rate.
- Leaking seal – Lubrication escapes, leaving your machine under lubricated.
To fix it, check your seals and review your lubrication plan for the asset. In some cases, your lubrication is perfect on paper, but lubrication routes are unorganized and equipment is missed. Lubrication management software can help you optimize the implementation of your plan and provides insight into your lubrication data, even integrating with in-line sensors or lubricant analysis labs. One Redlist user was replacing a bearing per week caused by lubrication issues, costing $20,000 in repairs and $12,000 per hour in downtime. After setting up their lubrication strategy in Redlist, they realized an estimated savings of $480,000 per year. Read more about their experience optimizing their lubrication management.
2. Lubricant Contamination
Contaminated lubricant creates a neverending cycle of increased component wear. The contaminants cause your bearings to wear faster, which releases wear debris. This debris increases the contaminant particle count, further increasing wear. Following best practices for cleanliness, storage, and implementing filtration of all lubricants (even new oil) will reduce your contaminant level. Additionally, you can monitor contaminants in real-time with an in-line lubricant analysis sensor. This can provide you with some baseline information on the type and amount of contaminants in your lubricant to determine the best corrective action. Furthermore, storing bearings in a clean area in sealed packaging until use, as well as confirming the effectiveness of your bearing seals, can reduce the risk of contamination.
3. Corrosion
Water, condensation, acid, or even the degradation of lubricant can lead to corrosion of bearings. This can dilute your lubricant and increase component wear. There are many preventive measures for corrosion, including lubricant analysis, vibration analysis, proper storage of lubricants, and using adequate seals for harsh environments.
4. Insufficient Operating Clearance
A major factor in the life and performance of your bearings is internal clearance. If operating clearance doesn’t meet industry or application standards, friction will increase, heat will build up, lubricant viscosity changes, and the bearing may even lock up. Thus, to ensure smooth operation, you must confirm your bearings have an initial internal clearance that allows room for a reduction in clearance caused by mounting or other influences. Otherwise, you contribute to lubrication issues and increase your risk of equipment breakdown due to bearing failure.
5. Misalignment
Your equipment may continue to function with a minor misalignment, but it can contribute to higher operating temperatures. Additionally, significant misalignments cause excessive vibration, increase loads, and eventually bearing failure. The best prevention is regular inspections of shafts and housings, along with using precision-grade locknuts.
6. Poor Mounting and Fit
As you get deeper into this list of causes of bearing failure, you will likely notice a repeating list of outcomes. Improperly mounted bearings result in a tight fit that reduces clearance, increases friction, temperatures rise, and result in increased wear and bearing failure. As always, increased temperatures affect lubricant viscosity, which can further amplify your problems. You can prevent poor mounting and bearing fit by making sure all of your technicians are educated on and follow proper mounting instructions, as well as using the right materials.
7. Bearing Fatigue or Spalling
Bearing fatigue is typically a progressive failure that only gets worse with time. However, premature fatigue is often a sign of overloading your bearings. You solve normal fatigue by simply replacing the bearing. But, if your bearings are failing sooner than expected, look at all the factors from load to mounting and clearance. You may want to switch to a bearing with a longer life expectancy to better suit your needs.
8. Overheating
Any number of causes on this list can lead to an increase in operating temperatures. Yet, overheating is still worth mentioning on its own because it is essential to understand its impact. High temperatures reduce your lubricant’s efficiency, increase oxidation, and reduce the hardness of metal bearings. This can cause your bearings to seize, become deformed, and lead to bearing failure. The best preventive action is monitoring operating temperatures and implementing overload controls, heat paths, or adding additional cooling.
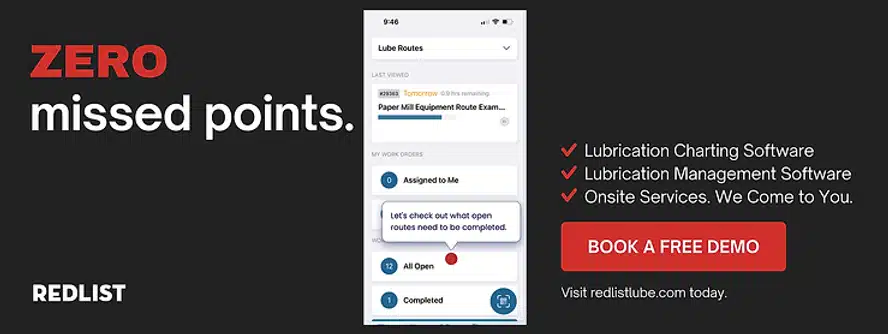
The Bottom Line on Bearing Failure
Root cause analysis after a bearing failure is a critical step of prevention. Also, your lubrication management and supporting best practices can prevent many of the bearing failure causes on this list. The bearing is a critical component in most applications. If you want to get the most life out of your machine, it’s important that you are aware of potential problems with bearings and how they can be prevented from happening. After all, prevention is better than cure. By following these recommendations, you can prevent your bearings from failing and save yourself money in the process.