The industrial lubricants that you use in your machinery are important for keeping your equipment running smoothly. However, if you don’t filter this oil regularly, it can become dirty and actually cause damage to your equipment. There are a variety of benefits that come with implementing an industrial oil filtration system. You can extend the life of your equipment, reduce wear and tear, prevent costly repairs, ensure optimal performance, and maximize equipment efficiency. In this blog post, we’ll discuss why you need to filter industrial oil and how doing so can help protect your machinery.
Industrial Oil Filtration Systems Reduce Contamination
Even if you follow every best practice for your lubrication management, you will still end up with contaminated lubricant. As components wear down over time, small metal particles are released into the lubricant. This is a contaminant that if left unchecked will increase the wear rate of the equipment and possibly lead to premature failure. So, with contamination being impossible to prevent completely, you have to implement some kind of industrial oil filtration system.
Up to 70% of premature equipment failures are due to lubricant contamination. Filtering new lubricant and keeping it clean can help prevent this in your facility.
An Essential for Modern Equipment and Machinery
The benefits of modern technology are that lubricants are more durable, equipment is more compact and efficient, and lubricated systems are more tightly sealed. Base oils and additives can now handle higher pressure and temperatures and go longer between changes. Furthermore, equipment manufacturers reduce the size of oil reservoirs, pumps, and filters in their effort to lower equipment weight or increase efficiency. All of these advances in machinery and lubricants are excellent for cost savings, reducing environmental impact, and increasing productivity.
But, the downside? This means you have less lubricant working in more extreme conditions for a longer time than ever before. The longer you use your oil, the more the contamination builds up. In the past, companies may have gotten by without industrial oil filtration, but not anymore. Filtration is critical to the function of your lubricants and the health of your assets.
Different Types of Industrial Oil Filtration Systems
The best industrial oil filtration option for you will depend on the size of your organization. Some options for smaller operations:
- Lubricant distributor collects drums or totes back to their facility to filter.
- Filter Carts
- Centrifugation
- Vacuum Dehydration
- Multi-Stage Filtration
If your company uses a massive amount of lubricant, an industrial oil filtration company can come to your site with a lubricant testing lab, filtration panel, tanks, and multiple filtration options. Alternatively, companies that want regular filtration can invest in their own filtration equipment. This is a bigger investment that may make sense for you if you can save millions by extending the life of your equipment.
Tips for Your Industrial Oil Filtration System
Filter New Lubricant
If you buy your lubricant in very large bulk quantities, it still needs filtration but less so than smaller amounts. The issue with smaller amounts is that empty drums or 300-gallon totes don’t have an ISO (International Organization for Standardization) code for cleanliness. So, your “new” lubricant may be contaminated the moment your distributor puts it in a drum or tote. A shocking thing to consider is that new lubricant is oftentimes dirtier from a particle perspective than the lubricant in your machines and doesn’t meet OEM (original equipment manufacturer) cleanliness standards.
Flush Old Systems
While you can catch dust, dirt, and wear debris with industrial oil filtration, there are some other contaminants to consider. High-velocity flushing or special filtration techniques will remove oxidation products that leave varnish on equipment components and pipes. This varnish accumulates with time leading to sludge, which could cause other problems down the line. Additionally, contaminants can get trapped in these varnish deposits, further increasing the need for cleaning.
You may think that draining and changing out the lubricant would be a sufficient solution, but it typically isn’t. Even if you successfully drained 90% of the lubricant, you still have 10% that is highly contaminated. Furthermore, when you add new lubricant the contaminated 10% uses up most of the new detergents, dispersants, anti-wear, anti-foam, and anti-corrosion additives. That’s not even considering the downtime necessary to drain and change the lubricant, plus the cost of all new lubricant. So, flushing your equipment is an excellent way to remove years of these deposits. It may be an investment of time and money, but it is worth it.
Flush New Systems
Just as you wouldn’t expect a new lubricant to need filtering, you may not think a new piece of equipment needs cleaning. However, new machinery often has metal shavings from manufacturing, wear debris from pipe threading, soldering or welding debris, and of course dirt and dust from sitting in a manufacturer’s warehouse. If you install the equipment and put fresh lubricant in straight away, all of these contaminants remain in the system. So, a proper flush before first use will make sure you get a clean start.
Consider Filter Size
Small particles can make a big impact! Check your filters for the size of particles they will filter out. A lot of industrial oil filtration focuses on 10 microns and larger. But, your equipment may be better suited for filtering down to 3 microns. It all depends on how sensitive your assets are and what level of particles they can tolerate.
Minimize Lubricant Handling
The more your lubricant is handled, the greater your risk of contamination. If you can transport lubricant to equipment through pipes and valves, that reduces potential contaminant exposure. However, that is not feasible for all businesses. The next best thing is to ensure that your hand pumps and buckets are clean and labeled to avoid cross-contamination with other lubricants. When you pair minimal handling with industrial oil filtration, you are well on your way to optimizing your lubrication management.
Implement Lubricant Analysis
A critical point in any maintenance strategy is monitoring and continuous improvement. Lubricant analysis, whether it is from in-line sensors or sending samples to a lab, is the main way to confirm your industrial oil filtration system is working effectively. When you integrate lubricant analysis with lubrication management software, you can have real-time data on the quality of your lubricants. Furthermore, you can set contaminant thresholds that trigger automatic alerts to your maintenance manager and lubrication technicians for immediate attention. Not only does this allow you to track the progress of your lubrication management, but it also helps you catch issues sooner rather than later.
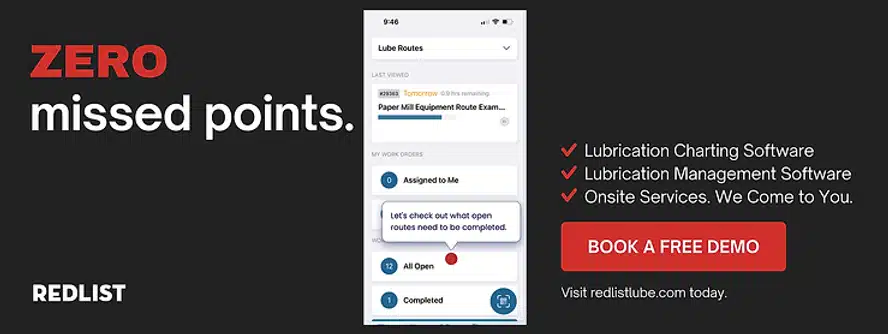
Find What Works for You
With so many variables to take into account, finding an optimal level of cleanliness for your system can be tricky. You have to consider your lubricant type, equipment clearances, condition, and the level of monitoring and prevention that fits your budget. It will pay off in the long run in reduced downtime, increased productivity, improved operating efficiency, and lower maintenance expenses. However, one thing is clear: The more contaminants are in your lubricant, the worse it gets. Simple dirt and dust accelerate component wear rates, adding wear debris to your lubricant, which continues the cycle of increasing wear. Industrial oil filtration is your key to putting an end to this vicious cycle.