Maintaining your business’s equipment is essential for ensuring that it continues to run smoothly and efficiently. However, crafting a maintenance strategy is not a cut-and-dried process. Not only do you have to sort through manufacturer-recommended maintenance, but also there is a growing list of maintenance types and tips to go with them. How do you balance reactive maintenance and preventive maintenance? What are usage-based and condition-based maintenance? Furthermore, what is routine maintenance? How do prescriptive maintenance and autonomous maintenance apply to your company? You may not even know where to start, so we recommend starting with information. Once you have a basic understanding of the various types of maintenance and strategies, you can determine what is right for you.
What is Routine Maintenance?
Routine maintenance tasks fall under the preventive maintenance category. Preventive maintenance is maintenance or inspections that you do on a recurring schedule to prevent equipment breakdown. The recommended standard to strike a balance between preventive and reactive maintenance is 80% preventive and 20% reactive. Reactive maintenance includes unplanned maintenance tasks that you perform in response to equipment breakdowns or issues. So, routine maintenance is an essential part of finding the balance in your maintenance plan. You may perform these routine maintenance tasks daily, weekly, monthly, or even annually. In fact, routine maintenance is typically simple or easy tasks that make them a great candidate for autonomous maintenance. By performing routine maintenance, you can catch small problems before they turn into big ones, and keep your equipment running at its best.
Types of Routine Maintenance
There are several tasks included in routine maintenance, including:
- Regular Inspections
- Changing Filters
- Cleaning Equipment
- Lubricating Components
- Adjusting Equipment
- Changing the Oil
- Topping Up Fluids
- Replacing Parts on a Scheduled Basis
- Inspecting and Testing Safety Equipment
Even though routine maintenance is planned, it isn’t limited to a time-based schedule. If you take oil changes as an example, you don’t change a vehicle’s oil every month. Instead, you decide when to change the oil based on the actual usage of the vehicle. So, a routine maintenance oil change would be on a usage-based schedule. If you have consistent data about your company’s vehicle usage, you can determine the approximate date that a vehicle will be due for an oil change based on its average daily miles driven.
Why Is It Important?
The biggest benefit of routine maintenance is the reduction of equipment downtime. If you don’t know your business’s cost of equipment downtime, it is generally in the thousands of dollars per hour. Between the cost of lost production and the expenses associated with repairs, it adds up quickly. Even if your equipment doesn’t reach a point of failure, it may slow down production when it isn’t operating at its best. Therefore, a routine maintenance plan for each of your assets will increase reliability, production, safety, and profitability.
Asset Lubrication Case Study
A wood production company noticed a trend that they were replacing a bearing per week due to lubrication issues. Lubrication is a routine maintenance task, which means it is a relatively simple task. However, when you have over 500 assets with 1200 components and 2300 lubrication tasks, this easy routine maintenance task can slip through the cracks. Without a lubrication plan in place, assets were regularly missed. The resulting bearing failures cost the company about $12,000 per hour in lost production and up to $20,000 in repairs. After implementing Redlist’s Enterprise Asset Maintenance (EAM) software, the company has successfully completed 100% of its lubrication routes. This one change to their routine maintenance increased their production, asset reliability, and saves them an estimated $480,000 per year.
Equipment Inspection Case Study
Another company implemented Redlist because their lift trucks would break down, costing them $5,000 per hour in lost production. So, they wanted a routine way to recognize problems before they reach equipment failure. They set up Redlist’s forms tool to support regular daily and monthly inspections of all mobile assets and safety equipment. The digital inspection reports even trigger automatic repair notifications to improve the speed of maintenance. Since using Redlist, the company achieved its objective of reducing equipment downtime and saving $5,000 per hour of production.
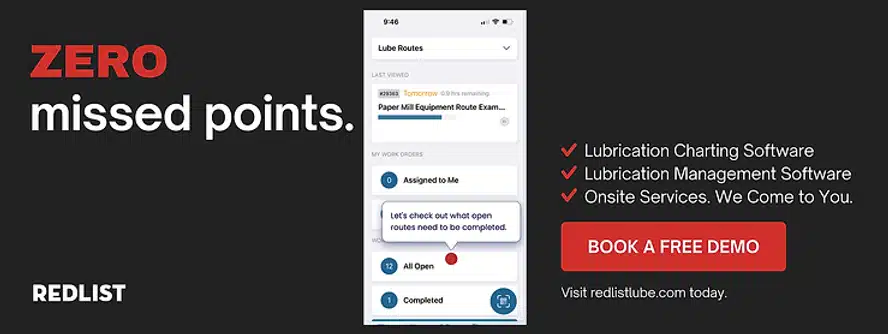
Make the Most of Your Maintenance with Redlist
Routine maintenance is an essential part of keeping your assets running efficiently and preventing costly equipment downtime. By scheduling regular preventive maintenance tasks with EAM software, you can ensure that your business runs smoothly and safely. Our team at Redlist would be happy to help you create a custom routine maintenance plan for your business. Schedule a demo today to learn more about how we can help you save money and increase production.