When it comes to lubrication management, you may think contamination by particles can cause the most damage. Studies show that improving particle contamination by a single ISO cleanliness code can increase the life of sensitive components by 10 to 30%. Additionally, some organizations have successfully cut failure rates by up to 90% with advanced lubricant filtration to control fluid cleanliness. However, many organizations overlook that water in oil is a serious issue that can cause considerable damage to equipment. In this post, we’ll cover everything you need to know about water in oil, including the consequences and how to prevent it.
Understanding the Presence of Water in Oil
Water in oil typically shows up in one of the below states or phases.
Dissolved Water
The presence of individual water molecules scattered throughout the oil is a sign of dissolved water. A perfect example to understand dissolved water is humidity. You know the water is in the air because you can feel it, but you can’t see it. Dissolved water in oil is the same, as it is mixed in on a molecular level that you can’t see. This is why oil may have a high percentage of dissolved water without any outward signs of it being there.
Depending on the temperature and age of the oil, the majority of industrial oils can hold from 200 to 600 ppm (parts per million) of dissolved water, which is 0.02 to 0.06%. Older oils are able to hold three to four times more dissolved water than fresh oil. Although there is no immediate danger to your equipment, the presence of dissolved water can speed up oxidation.
Emulsified Water
Emulsified water occurs when the oil reaches saturation due to the water content reaching a point where it can no longer dissolve. This stage results in an emulsion, or suspension of water in oil, composed of microscopic droplets. Continuing with the weather example, this is comparable to fog. The air is completely saturated with moisture, resulting in the excess water appearing as small droplets suspended in the air as fog. However, when it comes to water in oil, this “fog” is better known as haze because the oil looks cloudy or hazy.
The ability of an oil to handle loads will drop significantly with emulsified water. Additionally, the oxidation process is considerably increased when temperature and pressure are applied to the lubricant. Emulsified water can cause premature degradation, rust, and internal corrosion.
Free Water
As more water enters the lubricant, the oil and water will separate. This results in three components:
- Free Water
- Free Oil
- Emulsified Water and Oil
You can think of free water as a rainy day because it is an excessive amount of water that is very noticeable. Free water resists mixing with oil, so it tends to settle to the bottom unless it bonds with an additive or other contaminants. These free water layers can be found on the bottom of tanks and sumps for mineral oils and synthetics with specific gravities less than 1.0.
What Forms of Water in Oil Do the Most Damage?
Free water and emulsified water are the two most harmful phases in a lubricating system. As far as damage to oil and equipment, emulsified water in oil is the most dangerous. In addition, emulsified water is mobilized along with the oil, which means it travels unrestricted to the far reaches of the machine. Unlike free water that settles to the bottom of the reservoir, emulsified water can do far more damage to your vitally sensitive frictional surfaces.
Examples of Water Contamination Damage
A journal bearing may experience excessive wear due to the incompressibility of water relative to oil. Journal bearings can lose 90% of their life expectancy with just 1% water in the oil!
The issue is significantly worse for rolling element bearings. For starters, water weakens the oil film. But, rolling element bearings operate under extreme temperatures and pressures. This means that water in oil in the load zone can cause sudden flash-vaporization, resulting in erosive wear.
Another issue with water and rolling element bearings is the separation of oxygen and hydrogen atoms of the water molecule under the high pressure of the load zone. The hydrogen ions generated by this process, which are very tiny, may soak onto the surface of the bearing raceway, leading to a condition known as hydrogen embrittlement. Due to this, the bearing material beneath the raceway’s surface starts to weaken or become brittle, making it more likely to crack. Pitting and spalls may emerge as these cracks reach the surface.
Is there an Acceptable Level of Water in Oil?
A common rule of thumb is to make sure that moisture levels stay far below the saturation point. This is because the effects of free and emulsified water are more detrimental than those of dissolved water. Depending on the kind of oil and temperature, this translates to 100 to 300 ppm or less for the majority of in-service oils. Even at this level, substantial damage is still capable of happening. In general, there is never too little water. Therefore, it is important to take all practical measures to minimize water contamination.
What Does Water Actually Do to a Lubricant?
Water not only directly damages machine parts, but it also has an impact on the aging process of lubricating oils. Particularly in the presence of catalytic metals like copper, lead, and tin, the inclusion of water in lubricating oil can cause the progress of oxidation to multiply tenfold and result in premature aging of the oil. In addition, several synthetic oils, including phosphate esters and dibasic esters, have been shown to react with water, causing the base stock to disintegrate and the production of acids.
Water contamination can affect more than just the base oil. Several additives, such as sulfurous anti-wear and extreme pressure additives and phenolic antioxidants, are hydrolyzed by water. This causes additive mortality and acidic byproducts to form. When these acidic byproducts are present, they can corrode components. Excess water in oil can wash away other additives such as demulsifying agents, dispersants, detergents, and rust inhibitors. As a result, sludge and sediment build-up, the filter plugs, and the demulsibility is poor.
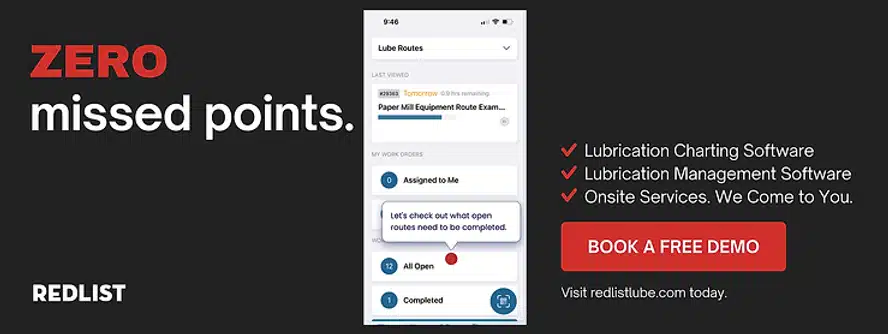
Reduce Water in Oil for Optimal Lubrication
If you look at the science of proper lubrication, water is generally a poor lubricant. Proper lubrication requires a film of oil to separate opposing friction surfaces. Pressure increases the viscosity of an oil film to maintain protection when pressure is applied. In contrast, water does not exhibit this tendency, and boundary lubrication occurs instead of full fluid film lubrication.
Even considering particle contamination, water is among the most destructive lubricant contaminants. Whenever it invades oil, machinery, or systems, it is helpful to know how it behaves to get your water levels under control. The first line of defense is inspection and early identification. The presence of any visual form of water should be taken seriously. Furthermore, an oil analysis program is an essential step to monitor water in oil and work on prevention.