Maintenance and lubrication technicians have long understood the benefits of using the right lubricants to help reduce wear and tear on equipment, lower operating costs, and extend the life of machinery. But what exactly are those benefits, and how do they impact a business’ total cost of ownership (TCO)? Well, a study by the International Lubricants Standardization and Approval Committee (ILSAC) found that lubricants can play a significant role in reducing TCO.
The study looked at factors such as energy consumption, wear and tear, and maintenance costs. According to ILSAC, proper lubrication can help reduce TCO by up to 30%.
In this post, we’ll explore how proper lubrication can help reduce TCO for businesses of all sizes.
What is TCO?
TCO is an acronym that stands for the total cost of ownership. It is a way of measuring the lifetime cost of owning and operating a particular asset. In order to reduce TCO, it is important to identify and eliminate as many sources of waste as possible. Lubricants can play a vital role in this process by helping to improve equipment reliability and reduce maintenance costs. Managing your maintenance schedule and lubrication systems proactively can lower your total cost of ownership.
Impact of Lubricants on TCO
You can increase the efficiency and productivity of equipment and reduce TCO with proper lubrication. Lubrication problems may be to blame for up to 75% of all equipment failures. This is despite the fact that lubricants only make up less than 5% of most organizations’ maintenance expenses. Surprisingly, a large number of businesses disregard the crucial contribution that lubricant application and selection make to TCO reduction. A recent survey discovered that 60% of businesses thought lubricants could only cut maintenance costs by 5% or less. However, in some industries, enhancing lubrication procedures can reduce the expense of maintenance and repairs by as much as 30%. In other words, organizations that do not include lubricants in their thorough TCO analyses may be losing money.
How to Reduce TCO with Lubricants
Automatic Lubrication
Automated lubrication systems provide lubricants in the right amounts, at the right times, and to the right locations. The result is optimal equipment performance and longevity. Additionally, they deliver a steady distribution, even in the most challenging conditions. However, damage may occur if you don’t regularly inspect and maintain the systems.
You can both optimize lubrication and lower TCO by implementing automatic lubrication. But for these systems, you need to follow a strict, regular inspection and maintenance routine. By spotting parts that you need to replace before a catastrophic breakdown takes place, these inspections can also prevent unplanned downtime.
Identify and Repair Leaks
Leaks, especially small ones, may be difficult to locate due to the intricacy of lubricating systems. Because of this, some businesses decide to simply replace lubricants more frequently to allow for leakage. Regrettably, this means higher lubricant costs and higher TCO. The price of lubricants can build up to hundreds of thousands of dollars, despite being relatively low compared to the cost of other components. It is vital that you identify and repair leaks as soon as possible.
Choose the Right Lubricants
Organizations frequently experience problems with lubrication management because they are unaware of the impact of higher-quality lubricants. This single change can extend the life of your equipment and lower costs. While it is essential to match the lubricant choice to the requirements of the equipment and the working environment, you must also look into higher-quality lubricants with longer service lives. In order to minimize contamination, you must also carefully handle and store lubricants.
The results of an industrial survey revealed that 46% of respondents had unplanned downtime events at their facility due to mistakes in the management and selection of lubricants. Of that group, 27% had downtime costs over $250,000 and over one in ten had downtime costs in excess of $1 million.
Purchasing subpar or ineffective lubricants may result in higher expenditures rather than cost savings. Making the right lubricant selection can reduce the expense of maintenance and component replacement, while also increasing operational effectiveness and ensuring that equipment performs appropriately. It’s all about finding the right balance between short-term and long-term savings for your facility.
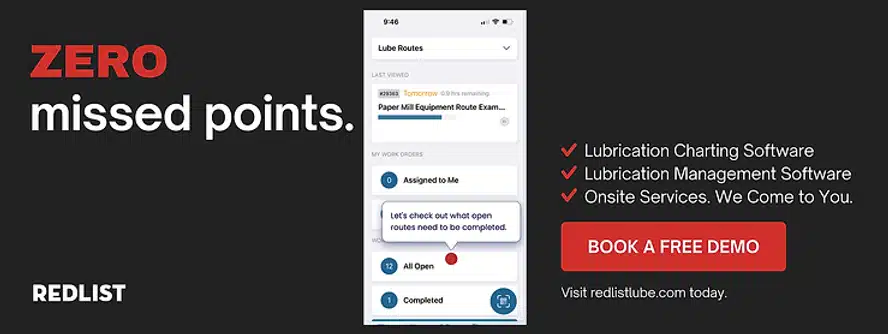
Now is the Time to Lower TCO
Sometimes the benefits of TCO programs are not immediately apparent. Industrial machinery is made to last and often has a tolerance for inadequate maintenance. This makes it challenging to immediately show the practical advantages of a TCO program. However, the key to optimizing TCO is to strike a balance between short- and long-term costs as well as long-term advantages. For a program to be successful, businesses must look ahead and understand that using higher-quality lubricants today and having a robust lubrication management and reliability program will lower maintenance costs over time.