The health of an industrial plant’s equipment depends on the quality of its oil. That’s why it’s important to take regular oil samples, so you can identify any problems early on and prevent them from causing expensive damage. But there are a few dos and don’ts of oil sampling that every maintenance technician should know. In this blog post, we will outline the basics of oil sampling, including how to take a sample and what to look for when analyzing it. We also provide some tips on avoiding common mistakes made during this process.
The Criticality of Oil Sampling
The lifespan of your equipment can be increased by routinely sampling your lubricant for analysis. Just as your doctor would order bloodwork to determine the quality of your health, lubricant analysis is necessary to determine the condition of your lubricants and asset health. It offers insightful data on what is happening inside the machinery, allowing for the early detection of problems to prevent costly breakdowns.
That’s the importance of lubricant analysis, but why is oil sampling so critical? The quality of the sample has the greatest impact on the accuracy of oil analysis results.
The results will be more accurate if you know when and how to properly take a sample from your equipment. Get the most out of your oil analysis program by following the dos and don’ts for oil sampling listed below.
Oil Sampling Dos
Do Check Machine Temperature Before Sampling
The goal of oil analysis is to capture a snapshot of the lubricant under normal operating conditions. When you sample lubricants when your equipment is not running, you won’t get an accurate snapshot. Not only will the lubricant not be at the right temperature, but also it will be stagnant, with contaminants settling to the bottom. The system must be circulating to identify contaminants in the system, and where they came from, otherwise, your sample might not be able to identify them. It is best to collect lubricant samples from a system that has run for at least 30 minutes. When the machine is warm, oil sampling will provide a good representation of the entire system.
Do Consider Your Oil Sampling Collection Point
You should always collect samples upstream from filters and downstream from components under monitoring. Filters remove contaminants and wear particles from lubricants. Oil analysis reports may not identify your wear metals if your oil sampling point is right after a filter.
Do Create Regular Oil Sampling Intervals
In order to analyze your lubricant analysis data and identify trends or abnormalities, you need a regular oil sampling interval. This also helps you establish a baseline to determine what’s normal. The original equipment manufacturer will usually have an interval recommendation. Maintain an oil sampling schedule for all your critical assets, whether it’s 500 hours, 10,000 miles, monthly, quarterly, or annually.
Do Make Sure You Complete the Lab Paperwork
One of the most frequent oil sampling mistakes is taking the time and effort to correctly collect a sample, but failing to complete the paperwork before submitting the sample to the lab. Do your best to make it a practice to double-check that every piece of information has been entered, and your sample is properly labeled before sending it off.
Oil Sampling Don’ts
Don’t Sample from Drain Plugs
Equipment drain plugs are generally located at the lowest point, resulting in a large collection of sediment. Samples from drain plugs do not accurately represent the entire system because of these high sediment concentrations. Unless you have no other option, avoid oil sampling from drain plugs. Whenever possible, opt for an oil sample port, a pump, or a dip-stick tube.
If that is your only possible sampling point, you can thoroughly clean the drain plug and surrounding area to minimize contamination. Then, remove the plug and let the lubricant flow for several seconds. Next, catch the lubricant flow midstream with your oil sampling container.
Don’t Allow Untrained Technicians to Collect Samples
If you task two different people with oil sampling from the same asset, they likely perform the task in two different ways. As much as possible, assign one individual to manage the sample collection process to reduce variability. However, that’s not always realistic with employee turnover or simply a busy maintenance team. So, you must also create a written procedure for sample collection and train your technicians to always sample from the same location and under the same conditions every time.
Don’t Wait to Send Your Sample
As soon as you have your sample and all the paperwork is completed, get it to the lab as soon as possible. Don’t let it end up in the backseat of a company vehicle, forgotten in the lube room, or left sitting on a maintenance manager’s desk. It may get lost or forgotten for weeks, delaying your discovery of any equipment issues it could alert you of. A prompt analysis gives you time to take action before unplanned downtime or costly repairs occur.
Don’t Be Afraid to Ask Questions
When your lab sends you results, there is often a section explaining the results, the condition of your lubricant, and what it may mean for your machine. But, if anything is unclear, contact the lab for support or clarification. They are often happy to help.
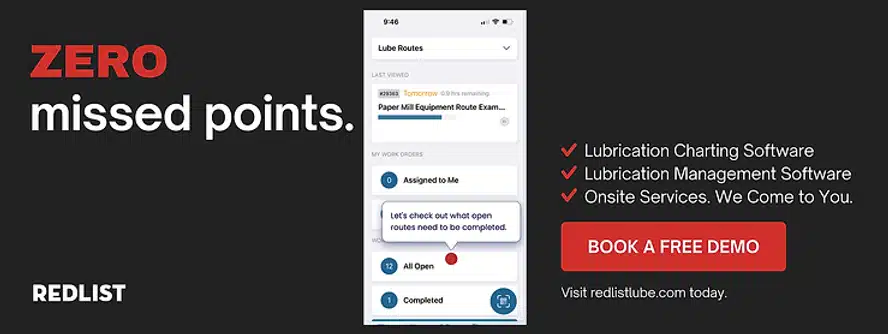
The Bottom Line on Oil Sampling
If you want accurate results, you must be accurate and consistent with your sampling. That’s why it’s essential to create oil sampling procedures according to best practices. Then, train your employees and provide supporting materials for them to follow the procedures every time. One of the key ways to do this is with lubrication management software. It provides a digital checklist that can include instructions, photos, videos, digital forms, and more for each lubrication task, all accessible on a mobile device. The final step is continuous improvement. If you notice unusual results, talk to your technicians about the sample and refine the process.