If you’re a manager, maintenance technician, or lubrication technician, you know the importance of oil sampling. But did you know there are common mistakes people make when taking oil samples? In this blog post, we’ll discuss some of the most common mistakes and how to avoid them. By being aware of these mistakes, you can ensure that your oil analysis results are accurate and help keep your equipment running smoothly.
The Importance of Oil Sampling Best Practices
Getting accurate test results depends on how you collect and handle your oil samples. Contaminated oil samples will skew test results, which makes the information unreliable. Oil analysis plays a vital role in ensuring the health and longevity of machines. Moreover, accurate lubricant analysis provides critical information about the cleanliness, additive content, and wear degree of your lubricant. Furthermore, when you test your oil regularly, you can track trends over time to identify signs of imminent failure or damage.
Several studies have shown that improper lubrication causes:
- 43% of mechanical failures
- 54% of bearing failures
- 50% of roller bearing damage
- 70% of equipment failures
So, lubricant analysis is essential to maintaining proper lubrication and equipment reliability. But, for lubricant analysis to be effective, you must have accurate results.
Top Oil Sampling Mistakes
Keep these common mistakes in mind when handling and gathering a sample to ensure you are using proper oil sampling procedures.
Your Equipment Wasn’t Running
To truly determine lubricant condition and performance, you must analyze it under its operating conditions, or as close as possible. This is because your oil sample should represent the lubricant in the machine for accurate analysis. You cannot accurately capture the condition of a machine’s oil during operations if you collect a “cold” sample, such as while the machine is off, just starting up, or idle. Ideally, the equipment should be running and at its normal operating temperature.
Your Equipment Wasn’t at or Near Operating Temperature
In some cases, you cannot collect a sample while the machine is operating due to safety restrictions. There are still best practices to follow for a true oil sample, despite this restriction. A sample taken from equipment that is not operating at its normal temperature will not give accurate data, just as a sample taken from equipment that is not running will not give accurate data. You should run the system for at least an hour, and then take the sample within 15 minutes of the shutdown to avoid below-optimal temperatures.
Oil Sampling from the Bottom of Your Reservoir
An accurate analysis depends on the location of the oil sampling. Depending on the source of the sample, your testing results can vary significantly. Sediment and other debris often settle at the bottom of reservoirs, which does not necessarily represent what is running through your equipment. This oil analysis might lead to an inaccurate assessment of the machine’s condition. The data will be more accurate if a sample is taken from the reservoir near the gear set or return line.
Sampling “Downstream” from a Filter
Oil sampling in this location is another less-than-ideal option. Again, you may end up with skewed results from any sample taken downstream of a filter. As your filtration system does its job removing many large particles and contaminants, you won’t gain insight into the particles and contaminants in your lubricant. These samples do not accurately represent the quality of the oil in the pumping system and do not provide accurate data on debris.
Improper Storage of Samples
The maintenance of oil sampling hardware and containers is very important for preventing contamination of samples. Additionally, it is common to overlook sample lid placement best practices. The sample container’s lid should be snug, and, of course, the sample container should be clean. Contamination can occur by failing to lid the sample jar or by placing the lid incorrectly. Also, if your sample leaks, you may receive an inaccurate or delayed analysis.
Not Maintaining Oil Sampling Hardware
To obtain accurate results from testing, you must maintain your sampling hardware. It is as simple as flushing sample lines and thoroughly cleaning containers. These steps are essential for ensuring a clean oil sample and more accurate analysis. Furthermore, the use of damaged sampling equipment can lead to contamination. So, inspect your sampling equipment before each use.
Safe Oil Sampling
When sampling oil, keep these two main objectives in mind: Safety and reliability. The first objective is always safety. It includes both the safety of the sampling personnel and the safety of your equipment. Technicians must understand the tools and risks and always adhere to safety regulations, including the appropriate personal protective equipment (PPE).
Even with safety protocols, many oil sampling techniques are risky. Opening a system can be dangerous, and drain sampling can result in burns. Additionally, it is challenging to regulate the flow of oil leaving the machine when drain port sampling. This excessive oil loss can cause starvation and become a safety hazard to your equipment. Furthermore, it can expose equipment to particles, moisture, and water contamination.
Another common technique that is risky is drop tube sampling. It is exceedingly risky to place a plastic sampling tube into the live zone of operating machinery. Without extraordinary care, there is a good chance that the plastic tube will get stuck in the gears. Thus, it often requires equipment to be shut off. Yet, even after turning off the machinery, the system remains vulnerable to outside contamination.
Oil Sampling Valves
Installing oil sampling valves can help keep your employees and machinery safe. They prevent burns and lubricant contamination by sending lubricant to the sampling bottle safely and hygienically. Additionally, a variety of remote access methods are available, allowing sampling to be done away from all equipment dangers. Sampling valves are excellent for collecting samples without requiring equipment downtime and minimizing lubricant exposure to potential contaminants.
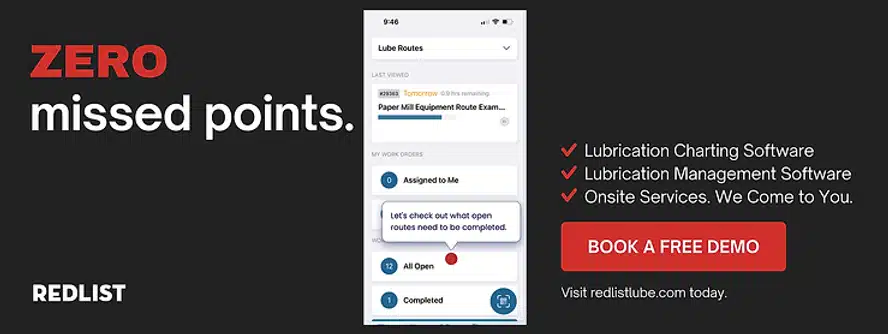
Better Oil Sampling Means Better Lubrication
A top-notch oil sample is the foundation of a world-class oil analysis program. A good oil sample will yield data that is more informative about the machine’s health. However, inconsistent oil samples mean the majority of businesses are not making the most of their oil analysis systems. They are making maintenance and lubrication decisions with skewed test results due to cross-contamination from incorrectly flushed lines, poor placement methods, and soiled or broken sample equipment. For the most effective lubricant analysis program, your oil analysis trends should depend on changes in the oil, not on which employee collected the sample. So, the simple goal is to perform it in the same manner and from the same place every time. Then, you will have the knowledge you need to increase reliability and minimize unplanned downtime.