To operate efficiently, bearings must have a minimal level of friction. You can achieve this by maintaining the bearing’s lubrication and ensuring that the oil viscosity is correct for the environment in which you use it. If you’re involved in the lubrication management of your facility and equipment, then you likely already know the importance of viscosity to lubrication. But, having bearing friction and oil viscosity explained will give you an even better understanding to continuously improve your bearing lubrication. In this blog post, we will explore how friction and oil viscosity affects bearings, as well as offer some tips on how to optimize their performance.
Oil Viscosity Explained: What Does it Mean for Bearings?
Viscosity is a critical characteristic of a lubricant. When it comes to grease lubricants, the viscosity of the base oil is important. A fluid’s viscosity is its internal resistance to shear. A fluid moving under laminar conditions, without turbulence, has several microscopic layers. Imagine it like a stack of papers, with each sheet (or microscopic layer) moving slightly faster than the next. This is the case with most bearing lubrication scenarios. There is a cohesive force between the layers that the fluid must overcome as they move past each other. This cohesive force between each layer is what determines the fluid’s viscosity. However, viscosity and friction are analogous in fluids. Which leads to the question, why is friction in lubricants necessary for reducing bearing friction?
The Impact of the Right Oil Viscosity Explained
It is estimated that improper lubrication causes 43% of mechanical failures, 70% of equipment failures, and 50% of damage to roller bearings. In the absence of lubrication, sliding, meshing, or rolling surfaces experience significant friction, heat, and wear. This increases noise, accelerates component wear, and reduces equipment life.
Issues with Low Viscosity
You may experience issues with too high or too low of a viscosity. These are some problems that are often a result of low viscosity:
- Excessive wear resulting from loss of oil film.
- An increase in mechanical friction.
- Inefficient machine operation using excessive energy.
- Higher operating temperatures.
- Potential internal or external lubricant leakage.
- Greater sensitivity to particle contamination.
- Insufficient oil film at high loads, high temperatures, or during startup.
Issues with High Viscosity
Low viscosity isn’t the only problem. Too high a viscosity can result in:
- Lubricant oxidation, sludge, and varnish buildup from excessive heat generation.
- Inadequate oil flow, causing gas cavitation on pumps and bearings.
- Equipment lubrication starvation.
- Journal bearings with oil whips.
- Consumption of excessive energy to overcome fluid friction.
- Air detrainment or demulsibility problems.
- Bad cold-start pumpability.
Lubrication-Related Bearing Problems
Not only can the wrong viscosity cause bearing failure, but other bearing issues can cause viscosity changes. So, starting with the right lubricant and proper mounting and operation will help you stay out of this vicious cycle.
These are a few examples of lubrication-related bearing issues:
- Low viscosity at operating temperatures – This can cause metal-on-metal contact due to a lack of oil film.
- Inadequate clearance – The internal clearance of your bearings plays a large role in determining their life and performance. Unless the operating clearance meets industry or application standards, friction will increase. This results in heat generation, lubricant viscosity will change, and the bearing may even lock up.
- Improper mounting – When you don’t properly mount your bearings, you reduce your operating clearance. This increases friction, temperatures, and bearing wear. Furthermore, it may result in viscosity changes, causing even more problems.
Boundary Lubrication and Oil Viscosity Explained: Why is it a Problem?
Even the best-machined, finished, and cleaned bearing surfaces will have asperities (peaks) and valleys. Asperities of two bearing surfaces interfere with each other when they are in contact. You can significantly reduce friction and wear by properly lubricating bearings to separate surfaces, reducing or eliminating interference between their asperities.
During stationary (or slow movement) conditions, the pressure between surfaces squeezes out most of the lubrication. Despite the thin lubricating film remaining, significant contact still occurs between the two surfaces. This is known as boundary lubrication. When it comes to boundary lubrication, the interaction between the surfaces determines the friction, heat, and wear of the components. However, chemical reactions may also contribute to wear. The life and performance of bearings rely heavily on the amount of time spent in boundary lubrication conditions.
A thicker lubrication film begins to form between the bearing surfaces as velocity increases. As a result, the lubricant’s viscosity increases because the pressure on its film increases. This is known as the pressure-viscosity coefficient. However, there is a transition period while the equipment is increasing velocity up to full operating speed. During this transition, only some of the surfaces separate, while others still have contact between asperities. This is known as mixed lubrication.
Finally, when your equipment reaches a sufficient velocity, your lubricant will form a sufficient layer to separate the asperities between the two surfaces. Additionally, your lubricant will reach optimal viscosity to provide a film strength that supports the load. This is known as elastohydrodynamic lubrication.
How Lubricant Analysis Can Help
Tracking viscosity is essential to improving your lubrication management. And, no lubricant analysis program is complete without monitoring and trending viscosity.
Whenever viscosity changes significantly, it is always necessary to investigate and correct the root cause. There can be changes in viscosity due to changes in the base oil chemistry, contamination, or other factors. Because of its impact on the lubricant and its impact on equipment life, viscosity is an essential physical property to monitor and carefully control. Lubricant analysis not only helps you track viscosity changes, but also can help you confirm the root cause. Additional tests can identify incipient oxidation, contaminant ingress, or base oil chemistry changes.
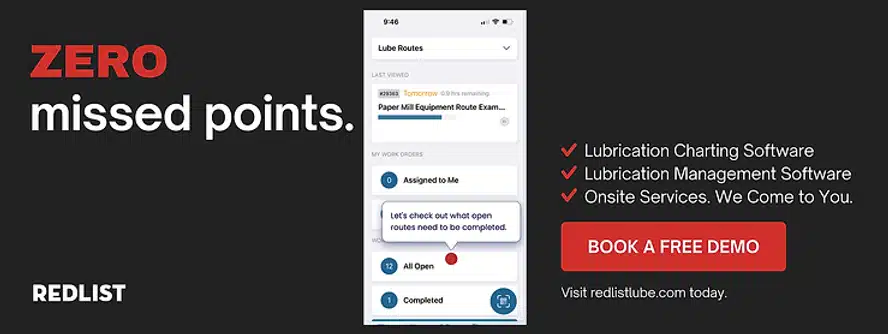
Lubrication Management Software and Oil Viscosity Explained
Lubrication management software can help with tracking lubricant analysis results and oil viscosity in a number of ways. For example, you can use the software to track the lubricant levels in each lubrication point, as well as the lubricant types and grades that you are using. Then, you can use this information to generate reports that compare the performance of different lubricants and identify potential problems. In addition, you can use the software to monitor the viscosity of lubricants over time. Furthermore, you can apply this information to assess the condition of lubricants and identify any trends that may indicate a need for further investigation. Ultimately, lubrication management software can help to improve the efficiency of lubrication systems and prevent equipment failures. Schedule a demo with our team to see how Redlist’s Lubrication Management Software could support your lubrication goals.