There is a lot of confusion about the difference between viscosity and viscosity index. Some people use these terms interchangeably, and it is often unclear which rating you’re looking at when choosing a lubricant. But, considering lubricant viscosity is its most important attribute, it is critical to understand the difference between these two versions of viscosity. In this blog post, we’re going to clear up the confusion and explain what each term means.
What is Viscosity?
For starters, viscosity is your lubricant’s resistance to flow. An example of a high viscosity substance is honey, as it doesn’t flow easily. Alternatively, water is a low viscosity fluid. When it comes to lubrication, every lubricant has a viscosity rating called the ISO Viscosity Grade (VG). To provide a consistent rating system, the VG for a lubricant is always established at a temperature of 40°C.
What is Viscosity Index?
To understand viscosity index (VI), think about the oil you use for cooking. At room temperature, cooking oil has a higher viscosity, meaning it resists flow. When you heat cooking oil in a pan, its viscosity changes as it becomes more fluid and reaches a low viscosity. The lubricant in your equipment functions in a similar way! Its viscosity changes as your equipment warms up and reaches operating temperature. So, viscosity index measures how much your lubricant viscosity will change as temperature increases or decreases. Furthermore, the formula and quality of each ingredient in your lubricant affects its VI.
Why is Viscosity Index Important?
If you’re choosing a lubricant with the right viscosity for your equipment, that’s great. However, checking the lubricant’s VI for your equipment’s operating temperature range is even better. Ensuring that the lubricant’s viscosity will be where you want it to be at all operating temperatures means you’re even closer to optimizing your lubrication management. Moreover, these are some of the equipment issues caused by viscosity changes:
- High viscosity = Low oil flow. This can result in oil starvation or a dry startup.
- Low viscosity = Loss of oil film strength. This can result in an increase in friction, heavier loads, and more mechanical wear.
The wrong viscosity in either direction can create more wear and tear and equipment failure.
A Lubricant Viscosity Index Comparison
To demonstrate how different two lubricants with the same viscosity grade can perform at various temperatures, here’s an example. Oil #1 has a VG of 150 and VI of 95, while oil #2 has a VG of 150 and VI of 150. As you can see in the chart below, oil #2 with a higher viscosity index does not fluctuate as extremely as oil #1 does. If you only look at viscosity grade, these lubricants are the same. But, it’s clear that their viscosity index can make a big difference in how they perform in your equipment.
Temperature | -20°C / -4°F | 20°C / 68°F | 40°C / 104°F | 60°C / 140°F | 80°C / 176°F | 100°C / 212°F |
Oil #1 (VG = 150 / VI = 95) Viscosity in cSt | 37,000 | 550 | 150 | 56 | 26 | 15 |
Oil #2 (VG = 150 / VI = 150) Viscosity in cSt | 11,000 | 435 | 150 | 65 | 34 | 20 |
Viscosity Difference in % | +236% | +26% | 0% | -14% | -23% | -25% |
The VI of Common Lubricants
A lubricant’s VI can range from -60 to over 400. However, most lubricants will be in the 90 to 160 range. Traditional mineral oil typically has a VI of 95 to 100. More refined mineral oils will have a VI of 120. Finally, synthetic oils can have a VI of up to 250. The higher the VI number, the less a lubricant will change viscosity as temperature changes. Additionally, this provides more stability and reliability for your equipment for a wider temperature range.
Some lubricants will have a VI-improver additive, which can help stabilize changes in viscosity. But, it’s important to note that additives are depleted over time. So, a lubricant that relies on an additive to help maintain viscosity will eventually lose that quality as the additive is used up.
How to Know What VI You Need
To determine the optimal VI of your lubricant, look at the operating conditions of your equipment.
A higher VI lubricant is best for equipment with:
- Fluctuating Loads
- Variable Speeds
- Shifting Temperatures
- Volatile Environmental Variables
- Unknown Viscosity Needs (if you’re unsure about viscosity, go with a higher VI).
Alternatively, you can choose a lubricant with a lower VI if your equipment has:
- Consistent Speed
- Constant Load
- Steady Temperature
- Known Viscosity Needs
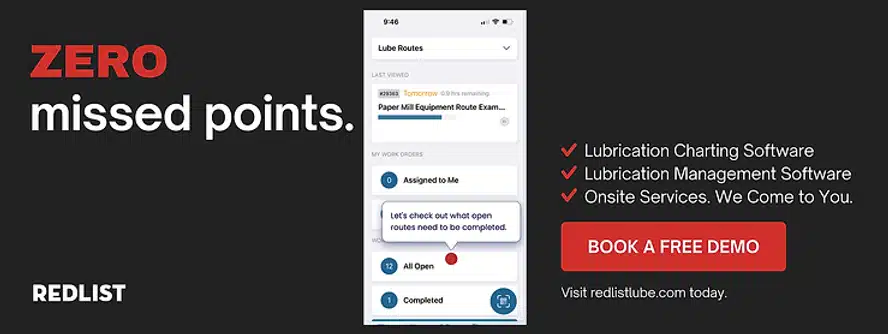
The Bottom Line on VI
Every machine will have different needs and various operating environments to factor in. So, don’t be afraid of trial and error. Maybe the first lubricant you choose doesn’t work out. You can explore using a higher VI lubricant next time. The key is to monitor your asset’s health and reliability after you make a change. Furthermore, that data will give you the insight to know if a higher VI was a good change, or if there is something else causing the problem. If you’d like to continue learning, click here to explore more of our lubrication management blogs.