Choosing the right lubricant can make all the difference in the reliability and prevention of wear and tear in your machines. Of the many lubricant choices in the market, there are two major types to choose from: grease and oil. Both types serve the same purpose of reducing friction and wear between surfaces, but they have different properties and applications. In this blog post, we will compare grease vs. oil, their differences, their advantages and disadvantages, and their applications. Keep reading to find out which lubricant is right for your needs.
Grease vs. Oil: What is the Difference?
Despite the ongoing debate over which is better, both oil and grease can be useful in lubricating industrial equipment. In general, you will use oil more often than grease because it tends to work better in conditions of high temperatures, high speeds, and intense friction. On the other hand, grease works well in bearing applications that operate at moderate speeds and temperatures.
The effectiveness of either oil or grease lubricants depends on:
- Specific Lubricant Properties
- Machine Specifications
- Operational Requirements
For example, for machines that you can’t lubricate often, grease is more suitable because it adheres to metal surfaces better. Oil lubricants have heat-conducting properties and are better for machine parts that operate in high heat. The following sections discuss the benefits of using grease vs. oil lubricant. These benefits help you better understand their properties and suitable applications.
What are the Benefits of Grease Lubricants?
Overall, grease is an excellent choice for lubricating heavy-duty equipment, machinery, and other applications that require long-lasting and reliable lubrication. When comparing grease vs. oil, grease offers several benefits over oil-type lubricants, including:
- Improved leakage control – The viscosity of grease lubricants allows them to adhere to worn seals and connectors, providing better lubrication without leakage.
- Excellent for stop-start machines – For machines that need to be turned off and restarted constantly, grease retained on the components prevents dry start, which is a critical source of wear for such machines.
- Beneficial for contamination control – If carefully packed around seals and connectors, grease can act as a sealant that keeps debris and water out.
- No circulating lubrication system required – Unlike oil which requires a refilling system including equipment such as a pump, filter, sump, or piping, grease lubricants don’t because they stay in the equipment for a longer period.
- Less lubricant consumption – Grease lubricants do not need a continuous supply like oil lubricants.
What are the Benefits of Oil Lubricants?
Overall, oil is a good choice for lubricating parts that require low friction, cooling, and easy application. It is commonly used in engines, transmissions, and other machinery that operate at high speeds and temperatures. When it comes down to grease vs. oil, oil also offers several benefits as a lubricant, including:
- Controlled lubrication levels – Oil lubricants allow easy control and management of lubricant usage. The oil volume in machine components can be controlled with the use of level gauges and sight glasses.
- Heat transmission and cooling capacity – The property of oil lubricants to flow easily lets them transmit heat, thus cooling the machine parts while lubricating them.
- Contamination control – Unlike grease that adheres to the surface of machine parts, oil can flow and transport contaminants away from the machines.
- Has no thickeners – Thickeners in grease can be incompatible with machine parts and with other components within the lubricant. Fewer thickeners also mean better lubrication and stability.
- Lower energy consumption – Energy consumption is a big part of the grease vs. oil debate. Grease provides additional viscosity that increases the energy used to operate machines. Oil lubricants flow more easily and lubricate machines without adding friction from their inherent viscosity.
- Ease of testing for wear – Oil lubricants can be easily sampled to test for machine wear materials, contaminants, and other characteristics. This is a vital part of lubrication management.
- Easier application – Applying oil lubricants does not require removing the hardware from the machine. Grease, on the other hand, requires dismantling and reassembly, which can result in high costs in labor, materials, and downtime.
- Minimized environmental impact – Used oil lubricants are easier to handle and dispose of, so their negative impact on the environment is less than grease lubricants.
- Ease of extending oil life – The life of oil lubricants can be easily extended through proper monitoring and replenishment.
- Promote longer lifespan on bearings – Compared to grease-lubricated bearings, oil-filled bearings have a longer lifespan.
- Better cold-start characteristics – In operations where cold-start is an issue, oil lubricants are more suitable because grease is less stable in conditions with large temperature differences.
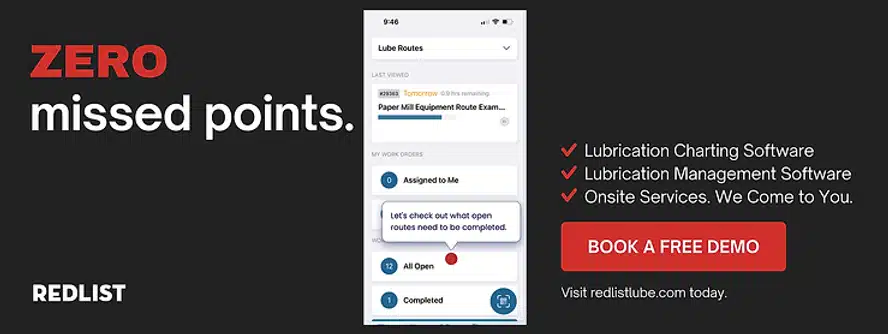
Grease vs. Oil: Lubricant Choice Crucial to Optimizing Lubrication Management
Choosing the ideal lubricant is a critical aspect of lubrication management. Lubrication management is a cycle of choosing lubricants, monitoring their performance, revising lubricant choices, and so on. Redlist’s Lubrication Management Software can be an essential help in accurately monitoring your lubricant choices and performance. With our user-friendly and intuitive software, you can rest assured that you can avoid lubrication errors and make the right lubrication decisions. To learn more about the features and support that Lubrication Management Software provides, request a demo today!