Any company in an asset-reliant industry has to dedicate a large portion of its budget to maintenance. Without maintenance, the assets fall into disrepair, and production slows or comes to a halt. Despite the importance of maintenance, most companies have a limited budget. This is why cost management for maintenance is a key practice for every maintenance manager. So, what counts as a maintenance cost? What is the best way to keep track of it all? And, how do you reduce maintenance expenses without negatively impacting your asset reliability and productivity?
What Qualifies as a Maintenance Cost?
When calculating your total maintenance costs, it is important to understand and break it down into the different line items, including:
- Spare Parts and Materials
- Labor
- Third-Party Vendors
- Energy
- Overhead
Breaking your maintenance costs into these five categories ensures you have clear data to identify areas for improvement. Knowing where your budget is going is the key to cost management for maintenance.
Other Important Maintenance-Related Costs to Track
There are two essential costs you will want to track but not include in your total maintenance cost calculation.
First, the cost of downtime. It’s easy for the accounting department or management to lose sight of the impact of maintenance. Maintenance costs are often thought of as just costs without the perspective of how much value they add to the business. Without maintenance, there would eventually be no profit. Thus, tracking the cost of downtime puts the value of maintenance in perspective and helps you measure the effectiveness of your maintenance strategy.
Second, you should track major upgrades and asset purchases as capital expenditures. These come with a much larger price tag, but also have long-term benefits. When it comes to accounting, these are separate from total maintenance costs. Capital expenditures can typically be depreciated over the years, as they are an investment instead of simply an expense. However, it is still necessary to track this with your maintenance data. As an asset ages, understanding the initial investment and the total cost of ownership will help you decide when to replace it.
How to Track Your Budget Data
While it is tempting to start a simple spreadsheet or keep a file with paper receipts, there are many reasons not to. In a perfect world, everything would get turned in and there wouldn’t be any errors in your data entry. But, even then, paper and spreadsheet-based processes are tedious, slow, and don’t provide you a real-time look at your data. They are usually limited to a single computer or file, which means you don’t have easy access to your data either.
Alternatively, using Enterprise Asset Management (EAM) software will solve these problems. Redlist’s EAM makes your data accessible on any computer or mobile device by storing data in the cloud. It integrates with other platforms to sync data, like asset sensors or accounting software. Additionally, all of your reports are auto-populated with your accurate, real-time data. This creates visibility into your data, so you can recognize trends and better manage expenses. Using an EAM also saves a lot of time on data entry. Whenever a technician is closing a preventive maintenance task or a work order, they will enter the time spent, parts used, and other necessary data right in the EAM system. This replaces the need for them to write that information on a paper work order, hold onto the paper until they turn it in, and have another employee enter that data into your spreadsheet or paper file.
The Bonus of Using EAM Software
You can configure your reports to be as big picture or as specific and granular as you want. For example, instead of only having a report that totals your maintenance costs, you can also have reports that break it down by type of asset, individual asset, or specific parts or components. When it comes to cost management for maintenance, this provides a huge opportunity to optimize your budget and your maintenance. Your report may show that you’re spending an unexpectedly high amount of money on bearings. This information could lead you to look at your lubrication routes and make improvements that result in fewer bearing replacements. With an EAM, reporting is faster, easier, and can be far more detailed to support your cost management for maintenance.
9 Tips to Reduce Maintenance Expenses
We’ve established what qualifies as a maintenance cost and how to track them, but how do you cut costs when you’re facing budget pressure? These are our top maintenance budget tips:
- Implement an EAM to streamline your maintenance and accurately track your expenses
- Set thresholds in your EAM to notify you of high spending, such as a sudden increase in your fluids costs, that may alert you of a leak in an asset.
- Digitize your inventory management
- Analyze inventory data for improvement, such as negotiating a bulk deal with a parts’ vendor.
- Monitor maintenance data for trends, such as poor lubrication or improper use by machine operators.
- Increase operator training for better operation and autonomous maintenance
- Consider adding IoT (Internet of Things) technology to automate data collection, such as temperature readings or oil analysis, saving your technicians’ time.
- Shift your maintenance strategy to follow the 80/20 rule of 80% preventive maintenance and 20% reactive maintenance.
- Always perform a root cause analysis to make sure you’re repairing the root of the problem and not just putting a bandage on a symptom. (E.g. more lubrication isn’t a fix for a bearing wear problem if the real issue is friction caused by misalignment.)
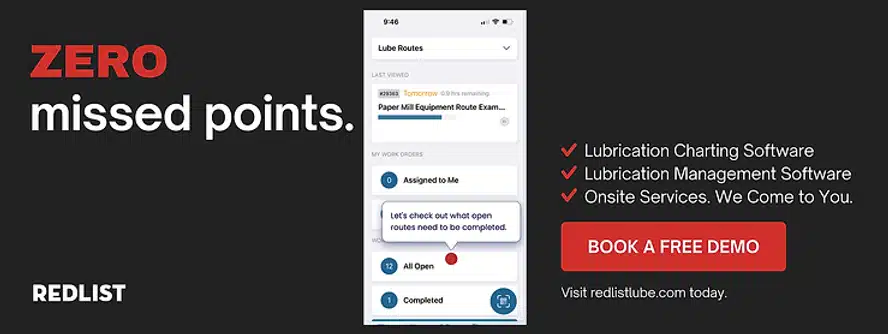
Improve Your Cost Management for Maintenance with Redlist
Managing your maintenance costs can feel like an overwhelming task, especially when faced with unplanned breakdowns that require expensive repairs. The only way to efficiently cut costs without negatively impacting asset health is to gain more clarity around your maintenance data. Redlist’s EAM supports you with maintenance, inventory, expenses, and even scheduling your work orders. You have to optimize all aspects of maintenance to optimize your maintenance budget. Book an EAM software demo today!