Work orders are the bread and butter of your maintenance department. In fact, an average maintenance team handles over 2,300 work orders per year, which is about 45 per week. This means that work orders have a huge impact on your business. Taking steps to improve your work order processes can increase efficiency, reduce downtime, eliminate maintenance backlog, and save money.
Go Digital
If you’re still using paper work orders, then going digital is the first and most important step to improve your work order process. Your technicians are spending precious time writing notes out by hand. Then, they have an additional step of submitting the work order to the office, either in-person or digitally. Entering notes into digital work orders is far more efficient than handwritten notes. And, digital work orders completely eliminate the second step of sending completed orders to the office. This results in an increase in productivity, so your technicians can spend more time on maintenance and less on paperwork. Multiply that time savings across your entire maintenance department, and you’re looking at enough time to significantly reduce your maintenance backlog, perform more preventive maintenance, and hit your maintenance goals.
Automate Work Order Flow
Digital work orders enable you to automate parts of the process that required manual input before. With Redlist’s Enterprise Asset Management (EAM) software, you can configure automated notifications for work order review, approval, and assigning tasks to technicians. Paper processes can create bottlenecks in your work order flow. Automating the work order process closes communication gaps and improves your mean time to repair (MTTR) metric. Basically, this means that important maintenance no longer falls through the cracks or gets delayed due to unreliable paper processes. Additionally, this improves your maintenance reporting process as well. When technicians complete work orders, the information auto-populates any reports you have set up in your Redlist dashboard. So, you can see real-time accurate maintenance information.
Give Technicians More Details
At this point, you’ve already saved a considerable amount of time from going digital and automating the work order process. Giving technicians more details in your work orders can save even more time, as well as improve health and safety. These are some of the details you can easily add to your work orders in Redlist, which includes having them automatically included on recurring work orders.
- Specific Description of the Problem and Repair – Maintenance can be done faster if the technician doesn’t have to troubleshoot or find the location of the problem. This takes you from just saying there’s a leak to including how bad, where it is in the asset, etc.
- Identification of the Asset – For example, if you have several forklifts, then your work orders need clear identification of which one needs maintenance.
- Comprehensive Task List – Redlist enables you to attach manuals, images, and all the specs for any maintenance task. Your maintenance will be more consistent. For example, different technicians might use a different lubrication type or amount when completing a task to lubricate bearings. Instead, your work order can include those details.
- List of Necessary Parts and Tools – Technicians will save time going to the storeroom for forgotten parts or tools they didn’t know they would need.
- Health and Safety Requirements – Including reminders about required personal protective equipment (PPE), safety procedures, or even common risks can go a long way for your safety compliance and avoiding incidents.
Standardize Work Orders Company-Wide
If you have more than one location, implementing these changes will standardize your work orders company-wide. This simplifies the hiring and training of maintenance technicians. New employees trained in the standardized company process can be dropped into any location and hit the ground running. This allows for greater flexibility in scheduling maintenance staff to fill in at different locations if needed. Furthermore, corporate-level management can confidently base decisions on the information and reports from all the branches, as everything is tracked and reported consistently.
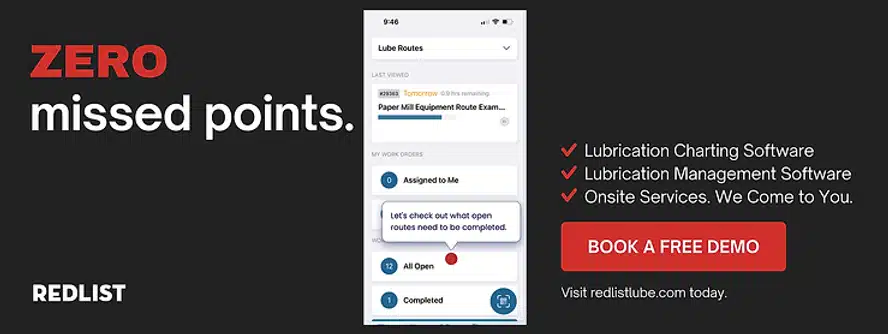
Big Improvement Can Start with Small Changes
The journey to better work order processes is a marathon, not a sprint. You don’t have to overhaul everything overnight to create a perfect process. These four steps will get you started, but your work order process will always be evolving and improving as your business grows. So, don’t get overwhelmed or overwhelm your maintenance team by trying to do it all at once. Start small and build in a culture of regularly reviewing and adjusting as needed. Redlist provides you a greater opportunity for data reporting and analysis, so you will likely identify even more things you can improve with time.