Maximizing return on investment (ROI) is a critical goal for any organization, and the maintenance department is no exception. By optimizing your lubrication management program, you can improve equipment reliability and decrease downtime, while also reducing your overall maintenance costs. Considering that lubricants are 1-3% of a maintenance budget on average, it may seem like a trivial amount to find savings in. However, the impact of poor lubrication can be as high as 40% of the maintenance budget due to wear of components and equipment downtime. Read on for some tips on how you can improve the bottom line with lubrication management.
Why is Lubrication Management Important?
In many cases, lubrication improvements alone can greatly reduce unplanned downtime. A poorly maintained lubrication program will likely result in significant unplanned downtime that will have a major impact on your bottom line and, potentially, your customers. In contrast, proper lubrication can enhance profitability by cutting costs, improving reliability, extending equipment life cycles, and operating at an optimized rate.
How Lubrication Management Saves Money
While investing in lubrication management costs time and money, it also saves money. Every business will see different savings, but these are some common examples:
- The elimination of motor failure due to lack of lubrication.
- Improved gearbox performance due to cleaner oil.
- Average annual savings of 30% on bearing costs.
- Increasing the lifespan of all hydraulic systems and pumps twofold.
Lubricant Consolidation
To reduce costs and minimize the chance of misapplication, most facilities stock and use few lubricants. There are, however, various factors to consider when selecting the appropriate lubricant for a machine, such as the environment, temperature, speed, bearing type, manual or automatic lubrication, etc. With a well-designed lubrication management program, lubricant selection can be optimized and lubricants can be utilized within a plant more efficiently.
This doesn’t mean you will run your entire business with only one type of oil and one type of grease. It’s about striking the balance between stocking the least variety possible, while still meeting the needs of your equipment. For instance, if you use multiple general-purpose greases, you might be able to consolidate to just one. You can probably reduce the number of greases you use to two, one general purpose, and one high-temperature grease. This provides savings for companies, but it requires knowledge of your lubrication management needs and a strategic supply decision.
How Lubrication Management Can Make Money
The ROI of lubrication management isn’t just about saving money. Alternatively, it can actually increase production and profitability by:
- Increasing production time, speed, or output with optimized maintenance intervals.
- Maintaining a low and known operation cost once you reach a steady state.
- Maximized uptime with low to no cost increase.
The Essential Components of a Lubrication Management Program
Supply Chain and Logistics
Consider suppliers who can provide a full range of goods and services for your lubrication management program, including lubricants, lubricating systems, lubricant analysis, failure analysis, and more. This will provide you with the best support for your ongoing lubrication management program.
Lubricant Handling and Storage
The lubricant storage room should, of course, be a secure, controlled environment that meets all health and safety requirements, including spill control and fire suppression equipment. However, you must also implement best practices to minimize lubricant contamination of dirt, dust, and debris, as well as cross-contamination of other lubricants. To prevent cross-contamination, lubricants and tools should be appropriately labeled.
Lubricant Selection and Application
You must ensure that your lubrication technicians have the necessary tools, safety gear, and written protocols for each lubrication task. With the support of your labeling system and appropriate training, they should be able to select the right lubricants for the job and apply them correctly.
Lubricant Analysis
Next, specify your lubricant sampling policies, practices, and analysis for each important asset, including primary and secondary testing. It is important to monitor the findings and look for trends. Samples should be taken in a consistent, contamination-free way. To do so, it is essential to create written guidelines and procedures for the location of sampling ports, the temperature of samples, and other best practices.
Contamination and Cleanliness Control
Machines should only use clean lubricants. That means you must have a method for filtering new oil before use, preventing contamination, and removing contaminants from in-service oil.
Planning and Scheduling Lube Routes
Planning and scheduling are necessary for all maintenance tasks, but even more so for lubrication management. The plan should be laid out and include the locations, the lubricants needed, the frequency and quantity needed for relubrication, replenishing, or changing the lubricant, as well as the persons and processes needed to carry out and record the particular lubrication task.
Lubricant Disposal
A defined procedure for handling and disposing of used lubricants is necessary to ensure compliance with environmental regulations.
Training
The physical activity of applying the lubricant, the implications of improper application, and effective inspections are all specialized training topics that must be covered for a lubrication management program to be effective. Additionally, training should be an ongoing tool for any continuous improvement of the lubrication management program. An important piece of training is tracking employee training and ensuring that only qualified employees perform lubrication tasks.
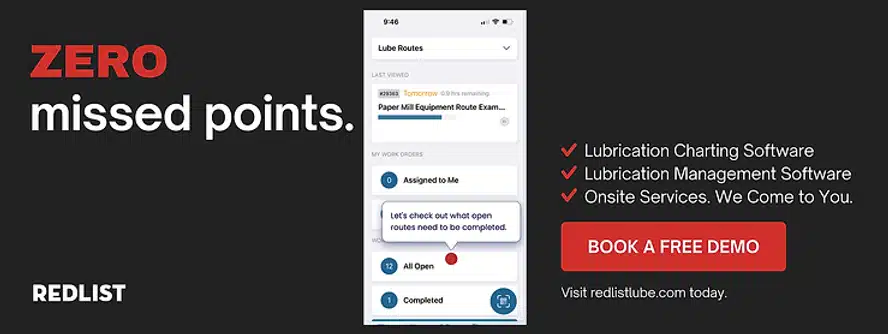
Time to Maximize Your ROI
The total life cycle of your equipment can be considerably improved by utilizing suitable lubrication practices, which can also increase machine uptime, lengthen service intervals, and reduce maintenance and operating expenses. Maximizing potential bottom-line benefits from appropriate lubrication procedures can be achieved by implementing a well-defined lubrication management program. In fact, one facility saved an estimated $480,000 per year by optimizing its lubrication management with Redlist. Click here to read more of their story.