Lubrication is essential for maintaining the performance and longevity of many mechanical systems. By reducing friction and wear, lubricants can help to keep moving parts operating smoothly. However, in order for lubrication to be effective, it must be applied evenly and in the correct amount. This is where lubrication guns come in. Lubrication guns are a necessary piece of equipment for any business that performs lubrication tasks. However, it is important to properly calibrate and use your lubrication gun to achieve the best results.
Why Do You Need to Calibrate a Lubrication Gun?
It is important to use the correct lubricant for the job and to apply it in the correct amount. Too much lubricant can be just as problematic as too little, and it can even cause dangerous buildup or leaks. Lubrication guns are designed to dispense lubricant in a controlled manner, making it easy to apply the correct amount of lubricant to a machine. Calibrating a lubrication gun ensures that it dispenses the right amount of lubricant each time, making it an essential part of lubrication maintenance. Through calibration, you can fine-tune your lubrication guns to deliver the precise amount of lubricant needed for a particular application. As a result, regular calibration can help to extend the life of machinery and prevent costly downtime.
How to Calibrate a Lubrication Gun
Here are the steps for how to calibrate a lubrication gun:
- Fill the lubrication gun with lubricant.
- Using something like a piece of scrap metal as your surface, slowly pump 10 strokes onto a postal scale.
- Divide the total volume weighed by 10 to determine your lubrication gun’s average flow rate.
By following these steps, you can be sure that your lubrication gun is dispensing the correct amount of lubricant. Every grease gun varies, so it is critical to perform this calibration with each individual gun to determine its volume per pump. This will help to prolong the life of your machinery and prevent potential damage caused by too much or too little lubrication.
How to Determine the Correct Lubricant Amount
Lubrication is essential, but too much lubricant can cause problems. Excess lubricant can build up on surfaces, attracting dirt and debris that can lead to clogs and jams. It can also seep into sensitive areas, causing electrical shorts or other damage. As a result, it is important to carefully monitor lubricant levels and only apply the amount that you need. There are a few different ways to determine the correct lubricant amount. First, there are a few factors to consider, including the size of the equipment, the operating conditions, and the type of lubricant you are using. As a general rule, you should start with the manufacturer’s recommendations and then make adjustments based on your specific needs. In some cases, it may be helpful to use a lubrication calculator or chart. These tools can give you a more accurate idea of how much lubricant you need for your equipment.
Quick Tips for Checking Your Lubricant Amount or Frequency
- Keep in mind that lubricant calculations may be measured in ounces or grams. Make sure you’re using the right one.
- Consider all the factors, including operating speed, reservoir volume, design, and the seals used in the application.
- Bearings that operate at a higher RPM (revolutions per minute) typically need grease equal to ⅓ the volume of space between the inside and outside races.
- Bearings that operate at a lower RPM typically need grease equal to ½ the volume of space between the inside and outside races.
- Check the bearing operating temperature before lubrication, then compare it to the bearing temperature five to ten minutes after lubrication. If the after temperature is considerably lower, your bearing was under-lubricated, and you may want to increase lubrication frequency.
- You can lubricate rolling element bearings while they are moving to allow them to purge excess lubricant. If it has a relief port, make sure it is open and clear. However, if there isn’t a relief port, you can remove the grease zero for five to ten minutes after lubrication.
- For bearing lubrication, use this equation: 0.114 x Bearing Outside Diameter (in inches) x Bearing Width (in inches) = Grease (in ounces).
- To convert your grease amount in ounces to pumps of your lubrication gun, use this equation: Grease (in ounces) x # of pumps per ounce (determined by your calibration) = Total Pumps Needed.
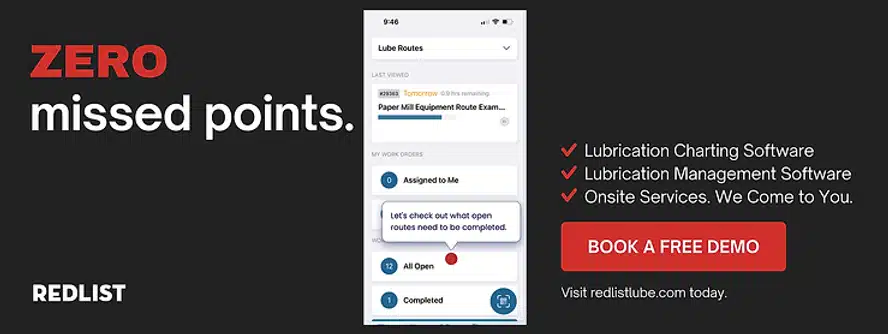
Lubrication Gun Best Practices Pay Off
Lubrication is important in many industrial and manufacturing settings. It can reduce friction, heat, and wear on machinery. As a result, lubricated machinery typically runs more smoothly and with less wear and tear. In order to ensure that lubrication is effective, it is important to calibrate lubrication guns regularly. Doing so will help to ensure that the lubricant is being applied properly and in the correct amount. This results in savings on equipment downtime, reduced maintenance costs, and even fewer lubricant expenses. Proper calibration and use of lubrication guns are just one of the many ways you can optimize your lubrication management.