If lubrication management is one of your key preventive maintenance strategies, then you’re likely tracking a lot of different lubricant characteristics. From viscosity and oxidation levels to contamination and the right additives for your assets, you have a long list of things to keep in mind. Another characteristic that you may have heard of is demulsibility. But, why is demulsibility important, and what exactly is it? This property is important because it can affect both lubricant performance and equipment reliability. Monitoring demulsibility and understanding what factors influence it are essential to the continuous improvement of your lubrication management.
What is Demulsibility?
Demulsibility is an attribute of lubricants that determines the ease with which water separates from the oil. In other words, it is a measure of how well the lubricant can resist emulsification. A high demulsibility rating means that the lubricant will resist forming an emulsion with water, while a low number indicates that it will not. Poor demulsibility can lead to fouling and decreased performance in the system. While it is common knowledge that oil and water don’t mix, large amounts of water contamination, or even certain polar contaminants, will decrease the demulsibility of your lubricant. Additionally, the more additives are in your lubricant, the lower the demulsibility rating will be. For example, anti-rust additives actually decrease demulsibility to prevent water from settling and breaking the anti-rust film.
Why is Demulsibility Important?
You have to pay extra attention to demulsibility for equipment with a higher potential for their lubricants to come in contact with water. This may be machinery operating in a humid environment or exposed to water-based processing fluids. Water emulsified in your lubricant can increase the collection of dust, dirt, and debris. This results in a depletion of additives, increase of wear and corrosion, faster fluid oxidation, and potential equipment breakdown. As demulsibility drops, you may have to condemn your lubricant sooner than necessary, or you may face lubrication problems with viscosity, varnish, and acid formation.
Understanding Water in Your Lubricants
There are two types of water you may find in a lubricant: dissolved water and free water. Dissolved water is water that is molecules that are evenly dispersed throughout the lubricant. Free water is water that has not been dissolved in the lubricant and typically collects at the bottom of the reservoir. If your lubricant’s demulsibility is good, you can drain the free water and avoid the impact of water contamination. However, dissolved water is harder to remove and is the main cause of poor demulsibility.
How to Test for Demulsibility
If you have a lubricant analysis program in place, your lab most likely tests for demulsibility. The test involves blending an equal amount of water and lubricant at a temperature comparable to the operating temperature of your sump. Then, the mixture is left to separate and you check it at 5-minute intervals. To measure demulsibility, record the amount of lubricant, water, and emulsion at each of those intervals. These are acceptable results:
- After 30 minutes, lubricants with a viscosity less than 90 cSt (centistokes) should have 3 mL (milliliter) or less emulsion.
- After 60 minutes, lubricants with a viscosity over 90 cSt should have 3 mL or less emulsion.
If you perform this test on your own, you can determine an appropriate benchmark by doing the test first with new lubricant and water. Then, repeat the test with a sample of your aged lubricant. If your aged lubricant takes over 20% longer for the oil and water to separate, then you should send a sample out for laboratory analysis.
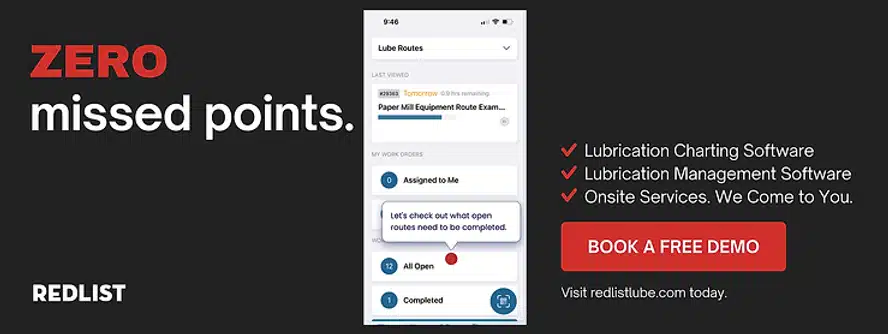
What Can You Do to Improve Demulsibility?
There isn’t an absolute standard for demulsibility, as its impact really depends on your system size and water exposure. For example, larger sumps can tolerate lower demulsibility better than small sumps. The key to improving demulsibility is to follow all the best practices to avoid water contamination, then monitor lubricant conditions on a regular basis. This can be done with in-line lubricant sensors that provide constant, real-time data, or with a lubricant analysis program. Finally, we recommend using Lubrication Management Software to integrate all of your lubricant data with your preventive maintenance tasks, work orders, and to trigger automatic threshold alerts for lubricant conditions that are important to you.
If you’re like most business owners, managers, and maintenance technicians, you may not think much about the demulsibility of lubricants. However, this characteristic is incredibly important, especially when it comes to preventing equipment failures and keeping your operations running smoothly. Furthermore, understanding what factors influence demulsibility can help you select the right lubricant for your needs.