If you’re a business owner, manager, or maintenance technician, then you know how important it is to keep your machinery running properly. But did you know that proper lubrication is one of the most important factors in maintaining machine health? A study by MIT (the Massachusetts Institute of Technology) found that 70% of machine failure is due to surface degradation. Further, the same study determined that 79% of surface degradation is caused by mechanical wear that you can reduce with proper lubrication. So, in this blog post, we’ll discuss the importance of machinery lubrication and outline some tips for achieving optimal results.
What is Machinery Lubrication?
Machinery lubrication is a preventive maintenance strategy of applying and maintaining a lubricating agent, such as oil, to machinery and its components. By doing so, you are doing more than simply reducing friction. When done well, machinery lubrication will reduce machine operating temperatures, slow the rate of surface degradation, and prolong the life of your asset. Additionally, improving lubrication at any point in the asset’s lifecycle will help increase the length of time between failures.
How Does it Work?
Let’s start with understanding the impact of friction on your assets. When two components rub, move, or rotate against each other, friction is the force that turns the movement into heat. For example, when you put your hands together and rub them back and forth, they start to get warm. That’s because friction is converting your kinetic energy (the movement of your hands) into thermal energy (the heat). While this may be helpful to take the edge off on a chilly day, this is not ideal for machinery. Your equipment operates at a higher speed and frequency, which means there is an exponentially higher amount of friction. That means you can end up with a considerable amount of heat the longer your asset runs. However, machinery lubrication can reduce this by lowering the friction and transferring the heat away from your moving components.
Why is Machinery Lubrication Important?
It’s not only important, it is vital for moving or rotating parts within your assets. Machinery lubrication is more than just a simple, menial task recommended by the OEM (original equipment manufacturer). It serves several purposes, including:
- Prevent premature component or machine failure – If your parts are wearing out quickly, you’re not getting the full expected life out of them or your machine.
- Reduce unplanned maintenance and equipment downtime – Fewer component failures or replacements means less unexpected maintenance.
- Avoid overheating of equipment – Reducing friction means you’re reducing heat. This keeps your machines at a safe operating temperature.
- Reduce component wear and tear – Lubricant creates a buffer between parts to reduce contact points.
- Decrease the impact of vibration – Machinery lubrication acts as a shock absorber, which reduces the wear caused by vibration.
- Reduce corrosion – The remaining 21% of surface degradation is due to corrosive wear. Lubricant can reduce this wear as well by protecting metal from environmental factors.
- Protect from debris or contaminants – With surface erosion comes debris that further increases friction and erosion of parts. Lubrication will draw particles or contaminants away from moving components.
Misconceptions About Lubrication
While you can and may be getting by with little to no strategy around your machinery lubrication, you will be missing out on a few key things. First, your assets may not reach their full lifespan. Second, your costs are likely higher due to using more lubricant than you need, increased downtime, and regular replacement of worn parts. This is all typically due to the misconception that lubrication is optional and doesn’t require a strategy. Alternatively, if you shift your perspective on machinery lubrication and think of it as a technical process, you can reap some massive benefits. However, that requires a shift from it being optional to being mandatory as well.
Tips to Implement a Lubrication Management Plan
When it comes to lubrication management, you may feel overwhelmed. After all, there is a lot to consider when planning and executing a successful lubrication management plan. From selecting the right lubricants and creating a schedule to implementing it all, there are several pieces to the puzzle of machinery lubrication. Redlist’s software can help you implement and carry out your lubrication management plan, but that is only one piece. So, these are a few tips to help you with the rest.
Audit Lubricant Needs and Stock
Many companies find they can actually reduce the number of lubricants they have on hand. That’s because it is far too easy to acquire a new asset and order the lubricant it needs, without realizing that you have one in the storeroom that would work. Any machinery lubrication plan has to begin with understanding what you need and what you have.
Create a Lubrication Schedule
This step alone can be complex, as you have to determine every component that needs lubricant and how often. Then, you have to assign those tasks to technicians on a recurring basis. It is helpful to group the tasks to make your lubrication plan more efficient. For example, if assets A, B, and C all take a different lubricant, your technician may spend extra time going back and forth to the storeroom for the proper supplies. But, if assets A, D, and H all take the same lubricant, grouping those lubrication tasks will allow your technicians to be more efficient and productive with their time.
Organize, Label, and Store Lubricants to Avoid Contamination
Your lubrication management plan will not be as successful if your lubricants are contaminated or the wrong lubricant is used on an asset. This is why organization, labeling, and proper storage are crucial. Labeling systems can include color-coded labels on storage containers, delivery tools, and even on the assets themselves. Furthermore, storing your lubricants correctly will reduce the amount of dirt, water, or other contaminants that you introduce to your machine when using that lubricant.
Analyze and Adjust Regularly
As with any preventive maintenance strategy, it is essential to analyze results and adjust your plan after implementation. With machinery lubrication, this may include in-line oil analysis sensors and regular oil samples sent to an oil analysis lab for more in-depth results. This gives you the opportunity to catch issues before they cause equipment failure. Additionally, oil analysis can help you extend the life of your oil. For example, instead of changing the oil at the OEM-recommended 500 hours, oil analysis could show that you can stretch that to 750 hours and still have good quality oil.
Machinery lubrication planning can be overwhelming. But, with the right resources and strategy, you’ll keep your equipment running smoothly for even longer than before. Even though we’re only a small portion of a lubrication management plan, we’re happy to partner with you in increasing your equipment reliability. Contact us for more information on how we can help or for lubrication management resources.
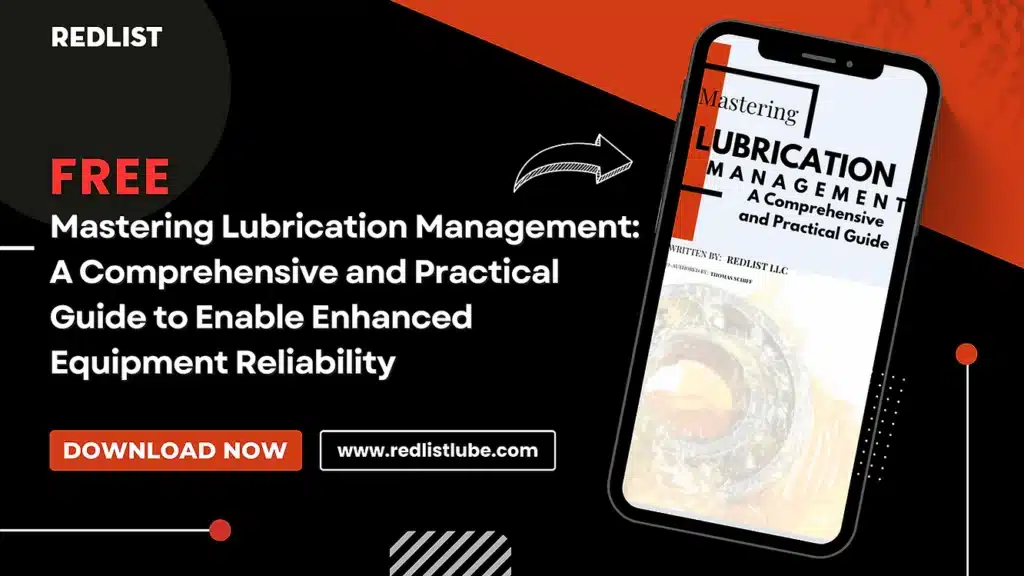