Since the COVID-19 pandemic, businesses have new challenges: How do you ensure the safety of your employees? In addition, how can you manage your maintenance operations more efficiently and affordably, given the backlog of maintenance issues? After all, maintenance and safety go hand in hand.
Even before and during the pandemic, facility managers must keep the company’s facilities and assets in good condition. And as we transition into this new normal way of life, the facility managers are additionally tasked to ensure that facilities, surroundings, and equipment are safe for their employees and customers. Add to that the new standards and regulatory requirements that facilities must meet to resume and maintain operations.
How can you control the environment so that there is more space between desks, hand sanitizers are stocked and strategically placed, and so on? How can you be sure that every process and procedure is followed, documented, and complies with all company, state, and government regulations?
The Answer to These Questions: CMMS Software
CMMS stands for Computerized Maintenance Management System, but you may also know Enterprise Asset Management (EAM) software. (They’re similar but different systems.) This software provides facilities and maintenance managers with the means to manage a company’s database for:
- Maintenance Operations
- Work Orders
- Equipment
- Assets
- Inventory
- Workflows
- Preventive Maintenance
- Safety Compliance
- Teams
- Expenses
- And More
The benefits of implementing a CMMS include reduction of maintenance cost, enhanced productivity, increased asset life, minimized downtime, and decreased overall cost of asset ownership.
How CMMS Helps Resolve Maintenance Issues
Improved Workflows
CMMS helps resolve maintenance issues by streamlining workflows. With improved workflows, adding tasks to your list is less challenging. And CMMS can significantly improve how you manage your facilities and perform maintenance operations. Additionally, a CMMS can come with useful features that help facility managers handle their everyday duties and responsibilities.
CMMS Work Order Management
Managing and prioritizing work orders using a CMMS can prevent the backlog of maintenance work. Users of CMMS software can quickly generate work orders to set tasks, describe the work, schedule completion dates, and provide specific instructions.
In addition, CMMS work order management software can also assist in managing and maintaining data on assets, costs, resources, and labor. As a result, organizations can manage and schedule existing and future work, evaluate data to make improvements, manage spending, regulate labor costs, and maintain compliance.
Streamlined Service Requests
By streamlining service requests, CMMS prevents maintenance errors and miscommunications resulting from mismanaged service requests. Digitizing information in place of using spreadsheets and pieces of paper prevents disastrous results. With CMMS, you can reduce and streamline the hundreds of service request phone calls, emails, and in-person visits.
The CMMS service request site is also easy to access for everyone on your team. Team members can submit service requests, view the request’s status, and be alerted when the request has been completed. With real-time notification, the service request is issued a tracking number and sent to the appropriate maintenance personnel for rapid response.
Asset and Equipment Management
CMMS can facilitate maintenance decisions on assets and equipment management by keeping detailed and updated files for each asset. With CMMS, every asset has its record containing information on repair history, the parts used, labor hours expended, reliability, and downtime.
Keeping accessible records provides information on the asset or equipment, which can directly influence daily operations. It also allows organizations to take a proactive approach to maintaining or retiring the equipment.
Effective CMMS Preventive Maintenance Scheduling
Implementing a CMMS increases the productivity and effectiveness of maintenance by allowing you to store all information in a central area accessible from anywhere. With CMMS, it is easier for users to initiate any form of maintenance activity, such as equipment repairs, interior and exterior building repairs, and more. Once initiated, maintenance activities will automatically be scheduled, and work orders will be generated for that specific time. These work orders will also come with complete details, including any additional information, components, and instructions required to conduct the maintenance.
Expense Management and Cost Monitoring
CMMS also helps resolve maintenance issues by making it easy to manage expenses and monitor costs. For example, even with many maintenance work orders being produced and performed, CMMS makes it simple to keep track of components, labor, and other related expenses. Also, users have the option to generate reports and view and manage spending at any time.
Tool for Safety, Audits, and Compliance
As you conduct business in this new normal way of life, the number one maintenance priority is compliance with safety and related regulations. CMMS can be a valuable help in storing and organizing the necessary information as you complete and document your compliance.
With CMMS, you can ensure that all processes and procedures are defined and documented and that technicians and workers are aware of and adhere to these modifications and rules. For regulatory and insurance requirements or visitors who use the facility, keeping track of all safety-related tasks associated with the facility and its equipment is essential.
Measurements of Success: KPI Dashboards and Reports
CMMS further improves your maintenance system by providing insights into areas of improvement, strengths, and other trends that can help improve productivity, efficiency, and cost savings. This is by having all your data in one place, which results in faster generation of analysis, reports, and recommendations.
Additionally, CMMS can come with customized dashboards that give you real-time data and a more detailed picture of how well your operations are performing. This allows you to react to increase productivity and continue to improve operations.
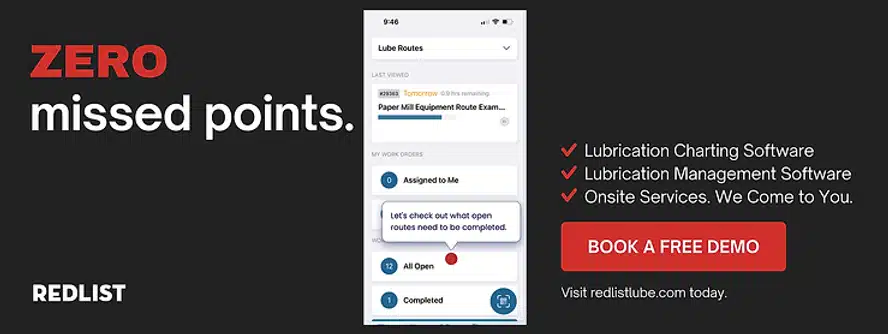
Make CMMS Software Part of Your New Normal
CMMS becomes an essential tool as we conduct business in a new normal environment. CMMS can help you meet the demands of clean and safe facilities and equipment with ease, efficiency, and lower cost. No matter your industry or business size, there is a CMMS solution that is the right fit for you. And a CMMS software like Redlist might be the one for you. Contact us to find solutions to your CMMS queries and problems, or schedule a demo today!