For any company that relies on its assets and equipment for production, work orders are essential to the business. But first, what is a work order? A work order is a document that provides information on approved maintenance work, including a description of the problem, repair needed, and any other supporting information. They are necessary to plan and schedule maintenance, but also to track maintenance metrics and usage of parts or resources. Detailed work orders are important if you want to optimize your maintenance strategy. Also, the document is not limited to being paper-based. In fact, to optimize the process, it is recommended that you go digital. You can streamline everything from work request submission and approval to work order creation and scheduling with a digital solution.
What are the Different Kinds?
It’s easy to feel overwhelmed by work orders, especially deciding which ones to prioritize in the budget and schedule. So, a key step is identifying the different types of work orders:
- Inspection – for testing or inspecting equipment and its performance or components.
- Preventive Maintenance (PM)– recurring or regularly scheduled maintenance tasks that are either recommended by the manufacturer or part of your own PM plan.
- Corrective Maintenance – if a technician discovers an issue during inspection or preventive maintenance, the work order to perform that repair would be for corrective maintenance.
- Emergency – for top priority maintenance due to unplanned downtime of mission-critical assets.
- Safety – for high priority maintenance to remove or prevent hazards that threaten employee safety.
- Special Project – for tasks that don’t fall into any of the above categories, such as installing new equipment or removing old equipment.
What is a Work Order vs. a Work Request?
Now that you know what is a work order, it is important to understand its difference from a work request. For example, a crane operator performing a pre-op inspection may discover that the crane needs maintenance. The operator can submit a work request that would describe the issue. Next, a maintenance manager would review this work request and either approve or deny the work. They may deny a work request depending on the maintenance budget, planned maintenance for that asset, level of severity, asset necessity, or even asset age. Once approved, they add the necessary detailed information to convert it to a work order. Finally, the manager can schedule and assign it to a maintenance technician to complete.
The Importance of Details
Detailed work orders enable your maintenance technicians to complete the tasks more efficiently. For instance, a simple preventive maintenance work order for an oil change. A basic work order may say, “Change oil in truck #32”. The technician doesn’t have any information about the amount of oil or the type of oil. So, they would have to go to the truck to determine those details. Then, they would have to go back to the storeroom to gather the oil. Instead, a detailed work order could provide all of that information! If the technician starts in the storeroom and brings all the necessary oil and parts, it saves wasted time that really adds up after performing maintenance all day.
What Details to Include?
This is a great list to start with, but we recommend creating a work order template based on your specific needs.
- Asset Description – This is especially important if you have more than one of a particular asset, so include details on which asset and even the location.
- What is the Problem – While preventive maintenance won’t always have a problem, most other work orders will. This information would come from the work request, as it is a detailed account of the issue that needs attention.
- Name and Date of Work Request and Order – These may or may not be the same person, but it can be helpful for a technician to know who first identified or experienced the problem.
- Scope of Work – Things like any special skills that are needed, if production must be shut down to perform the task, if you have to schedule a third-party contractor, and any other details about the work.
- Health and Safety – Safety regulations, mandatory personal protective equipment (PPE), or any notes about potential risks or hazards to be aware of while performing the work.
- Required Tools and Parts – This saves your technician trips back and forth from the storeroom!
- Checklist – Outlining specific processes for maintenance tasks can increase efficiency and ensure technicians don’t miss anything.
- Supporting Documents – Give your technician everything they need to perform the task, including manuals, videos, or asset history.
- Priority – Ranking the priority of maintenance work is vital to the scheduling process.
- Planned Completion Date and Hours – The due date for maintenance and how long it should take.
- Actual Completion Date and Hours – The actual date a technician completes the maintenance and how long it took them.
- Notes – This can be a general category of helpful tips or notes from past technicians to assist with the maintenance.
Benefits of Digital Work Orders
While there are a variety of ways to handle work orders from paper or whiteboards to spreadsheets, digital work orders offer the most benefits. Paper-based work orders don’t have the flexibility of easily attaching supporting checklists, manuals, or photos and videos of how to do the repair. Whiteboards face the same problem, but also are even more difficult to create asset history files from. Spreadsheets are a step up from paper and whiteboards because at least they are digital. However, some spreadsheets are only accessible from a single computer and they are still limited in functionality. Additionally, all of these systems require hours of data entry and compilation to generate reports for your maintenance metrics. This is where the benefits of digital work orders come into play.
Going digital with an Enterprise Asset Management (EAM) software solves all of the problems with the other work order systems. It provides a centralized system that is cloud-based and accessible from anywhere on a mobile device for all of your maintenance tasks. You can even set up automated notifications and easily implement a preventive maintenance plan. If you record notes from the technician after they complete maintenance, the data entry from paper is eliminated. The technician can make notes that save automatically in the system with digital work orders. Moreover, this streamlines your reporting process and creates visibility into your asset health and performance that you likely didn’t have before. It can all integrate with your budgeting and scheduling to create a streamlined process from start to finish. Also, possibly the biggest benefit of all is the ease of tracking maintenance to maintain regulatory compliance.
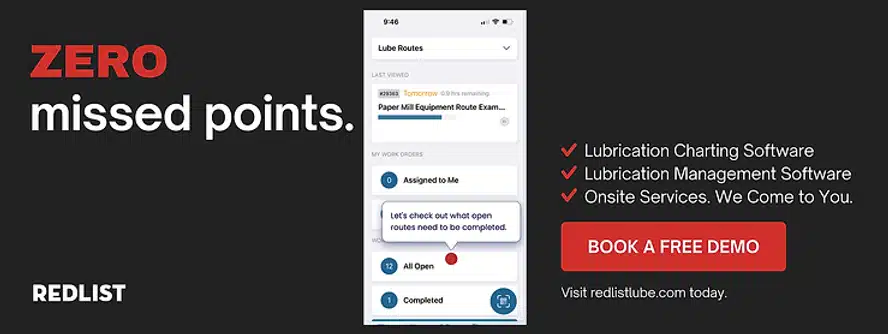
Optimize Work Orders to Optimize Maintenance
Work orders are the backbone of your maintenance operations. So, your work order process has the power to greatly impact your overall maintenance plan. Eliminating inefficiencies, automating more of the process, and, of course, going digital with your work orders will help you optimize maintenance. This makes it easier and more efficient for you, your maintenance managers, and your maintenance technicians. Furthermore, the better your maintenance operation, the better your asset health and performance. If you’d like to learn more about how Redlist’s Enterprise Asset Management software could optimize your work orders, schedule a demo today.