When it comes to maintenance, the conversation typically focuses on under-maintained assets. Understandably so, as downtime costs can be excessive. For example, manufacturers in the automotive industry have an average downtime cost of $22,000 per minute. That’s where preventive maintenance (PM) comes in to reduce equipment failures and downtime. However, an effective preventive maintenance plan must adapt to your use of the assets. While over-maintaining your assets likely won’t cost as much as downtime, it still has an impact on your bottom line. To stay competitive, profitable, and to optimize your maintenance budget, you can implement a usage-based maintenance (UBM) strategy.
What is Usage-Based Maintenance?
There are assets that you use frequently and assets that you use less frequently. Depending on where you are in your preventive maintenance plan, you may be over-maintaining those less-used assets. A recent study determined that 30% of maintenance activities are scheduled too often and contribute to waste in the maintenance budget.
Usage-based maintenance takes into account actual equipment usage to strike the optimal balance of preventive maintenance. It allows you to decrease costs on labor and parts and free up resources to better maintain your more critical assets. UBM is based on the number of miles driven, hours used, number of parts produced, or even an operating condition.
Benefits of Usage-Based Maintenance
Whether your goal is to hone your preventive maintenance plan or to reduce maintenance backlog, usage-based maintenance can help. We already mentioned the obvious benefit of saving money, but there are more benefits:
- Relieves team members to perform other maintenance, such as reducing your backlog.
- Optimizes maintenance planning to more easily integrate PMs into the workflow.
- Allows you to prioritize the PMs and assets that have a higher chance of preventing failure.
- Reduces unnecessary spare parts.
Where to Begin
When implementing usage-based maintenance, a great place to begin is identifying PMs you created from manufacturer recommendations. The manufacturer makes a general maintenance recommendation for optimal performance, which is often too frequent. Alternatively, you can run certain assets to failure. For example, a PM to change a lightbulb every 1,000 days based on the average LED lifespan of 10,000 hours would be wasteful if the lightbulb is still operational. So, start with any PMs from manufacturers or for assets that can safely run to failure.
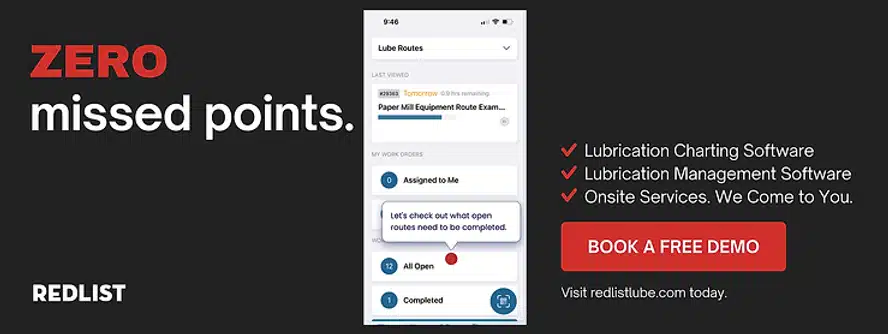
How Does Enterprise Asset Management Software Help with UBM
With Redlist’s Enterprise Asset Management (EAM) software, you can manage every aspect of your assets in one place. It is a key tool in creating a successful preventive maintenance strategy. Whether you base your UBM plan on manual meter readings or sensor data, you can configure each asset’s threshold to automatically trigger a maintenance work order. Finally, the best maintenance plan includes regular review and adjustment. Redlist makes this easy with reports that are auto-populated, so you can analyze and make decisions based on accurate, real-time maintenance data.
Using an EAM to automate your maintenance process frees up even more time and resources. One Redlist user, one of the largest privately-owned oil and natural gas producers in the U.S., was able to eliminate 25 hours per week of administrative work for their lead mechanic. The lead mechanic digitally recorded machine hours and used that information to drive and automate their PMs. If you’re taking the time to implement a preventive maintenance plan and looking at usage-based maintenance, then an EAM is a worthwhile investment. It’s the piece that takes your maintenance strategy to the next level.