Whether you use CMMS or EAM software or still run old school with spreadsheets and binders, bad maintenance data has a big impact on your organization. You rely on this data to make decisions, create your maintenance strategy, and understand how your assets are doing. But, how do you ensure that your data is as accurate and complete as possible?
Why is Bad Maintenance Data a Big Deal?
The answer to that question is found by looking at what decisions you base on your maintenance data. Most often, it is considered when deciding everything from purchasing new assets and hiring more technicians to scheduling work orders and planning preventive maintenance. Each one of those areas is incredibly important to your organization! Bad maintenance data can lead you to make the wrong decision, resulting in a trickle-down effect that hits every part of your business. Furthermore, if you’re a maintenance manager, then you need solid maintenance data to support your maintenance budget requests or push back on budget cuts.
Additionally, the trickle-down effect can turn into a safety hazard. Yes, it’s a big jump from bad data to safety hazards, but it happens. For example, it starts with a work order. The technician waits until the end of the day to record their work. Unless they have perfect recall, this typically translates into less accurate data. In this example, they forget precisely how long it took them to perform the work, and the time they record is rounded down. The next time a similar work order is scheduled, less time is set aside for the technician. They now have to rush to finish the job, and that increases the possibility of error. This puts the technician at risk, the asset at risk, and future operators at risk if the error causes the asset to break down or malfunction while in use.
How to Find Bad Maintenance Data
You’re probably thinking, “My maintenance team is already spread thin, how am I going to sort through data? And, how will I know if the data is good or not?” The easiest way is to start with the assets or areas that you are having problems. For an asset that is constantly breaking down, or one that breaks down periodically and you don’t know why, look at its data. Are there any gaps? Any anomalies? Talk to your team and see if your data matches what’s really going on. Here are some other places you often find bad maintenance data:
- Preventive Maintenance Schedule
- Work Orders
- Asset Maintenance History
- Storeroom/Parts Inventory
- Anomalies in Reports
How to Improve Your Maintenance Data
There isn’t a one size fits all solution to improving your maintenance data. It all depends on where your bad data is and its root cause. But, these are our top tips to improve the quality of your maintenance data.
Streamline the Process for Your Technicians
Streamlining the process can look a few different ways all with the same goal: Enabling technicians to easily record data immediately after the work is completed. For some organizations, this is a scheduling shift. When you schedule a work order, are you including time for the administrative tasks needed to support it? For others, streamlining requires a review of your system. Is a spreadsheet or binder creating obstacles to collecting accurate data? Redlist solves this problem for clients by providing an easy system that allows technicians to complete work orders on any mobile device, even when offline.
Get Clear on What Data Matters Most
You’ve likely heard the phrase, “Jack of all trades, master of none.” Well, it can apply to your maintenance data. If you’re overwhelmed with data or asking your team to track and record a hundred different things, then you’re less likely to reap the benefits. It may take some trial and error to determine what data matters most to your organization, but it is worth it. Once you get clear on that, you can communicate to your team the importance of those data points. Then, it will truly be a group effort to ensure that your most important data is recorded accurately. Your overall maintenance strategy comes first, and the data and metrics will follow.
Check Your Inventory
Bad maintenance data from your inventory affects your budget and your ability to complete repairs. A regular inventory checkup allows you to liquidate parts you no longer need and ensures you have what you need. The last thing you want is a surprise bill for a part you thought was in your storeroom but actually wasn’t.
Review Your Preventive Maintenance Plan
When was the last time you reviewed your preventive maintenance plan? It is possible for your PMs to go stale. For example, a previous maintenance manager sets a PM to inspect an asset regularly after a breakdown. Maybe that asset was fixed or replaced, but the new maintenance manager inherits the PM that is no longer needed. Eliminating this PM that is no longer needed frees up your technicians’ time and terminates the unnecessary inspection data. However, this isn’t the case with every PM, so do your due diligence and keep what is required.
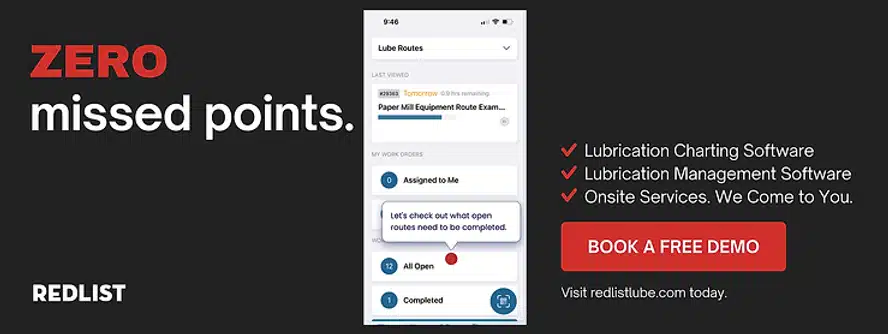
Good data turns into good decisions that lead to impactful changes.
Now, bad maintenance data isn’t an issue if you don’t have data! That’s why so many organizations are turning to technology to support their maintenance team. Redlist’s mobile app allows you to digitize your data collection and can be configured to your specific needs. Once you collect your data, it auto-populates a dashboard with the reports and metrics you want to see for your business. Then, you have everything at your fingertips to make the best decisions for your team. That is how solving your bad maintenance data problem leads to impactful changes.