Improving machine reliability is an excellent way to reduce downtime, but knowing where to begin or what to improve can be overwhelming. While many factors contribute to machine reliability, lubrication is one of the most essential. Lubricants help reduce wear and tear on parts, preventing damage that can lead to machine failure. In this blog post, we’ll discuss why lubrication is so important and how it can help you achieve improved machine reliability.
How Does Lubrication Impact Machine Reliability?
Lubrication management is one of many preventive maintenance strategies that impact machine reliability. Applying lubricants to machinery goes beyond simply reducing friction. Lubrication, when done correctly, will also:
- Lower the operating temperature of the machine
- Reduce the wear and tear on moving parts
- Absorb shock
- Reduce contamination
- Prevent corrosion on metal surfaces
- Ensure that all components are sealed and protected
- Enhance the lifespan of your assets
- Lower component and asset failures
We’ll dive deeper into the details of many of these impacts below.
Ways to Improve Machine Reliability
Completing lubrication tasks is about more than simply following the routine maintenance the OEM (original equipment manufacturer) recommends. You can improve machine reliability, reduce downtime, and lower your maintenance costs thanks to lubrication management. Here are the ways to improve machine reliability through the purposes that lubrication serves.
Reduce Friction
Moving parts come into contact with one another in mechanical systems. Machine parts could appear to be smooth to the unaided eye, but a different picture emerges under the microscope. Surfaces have tiny spikes called asperities that arise from them, and these asperities produce friction when moving parts come into contact with one another. This lowers the performance of the equipment by slowing down machine processes. Additionally, abrasive forces and intense heat experienced during this action wear down parts and destroy machinery, rendering it unreliable. Through excellent shock absorption, reduced friction, and reduced wear and tear caused by friction, lubricants allow parts to move freely without catching on one another.
Lower Operating Temperature
You reduce heat when you reduce friction. In addition to serving as a coolant, lubricants help lower operating temperatures when parts are operating, preventing harm from too much heat. Your machines will remain at a safe operating temperature, thereby increasing their reliability.
Reduce Shock
Lubrication can help to lessen the effect of vibration. It functions as a shock absorber and lessens the wear brought on by vibration. When you reduce this impact, you positively impact machine reliability.
Lower Your Component Wear Rate
Wearing out your machine’s parts quickly means your machine will not last as long. Not only will you have to take the machine offline for component repair or replacement, but also it will experience a shorter lifecycle. To reduce contact points between parts, lubricants create a buffer between them. You can increase machine reliability by properly lubricating components to prevent premature failure.
Minimize Corrosion of Metal Surfaces
After wearing from friction, corrosive wear is responsible for the remaining 21% of surface degradation. Rust, which is produced when iron alloys are exposed to moisture and oxygen, can make metal parts brittle and more likely to break down. Your machinery must function in a variety of environments that may expose it to corrosive elements. By shielding metal from the elements, lubricant can also lessen this wear.
Keep Contaminants and Debris Out
Contaminants such as dirt, debris, varnish, and water can damage machinery and reduce machine reliability. Debris produced by surface erosion increases friction and contributes to further erosion. Lubricants protect equipment by sealing against corrosion and removing contaminants. The presence of lubrication will prevent particles or contaminants from sticking to moving components. Keeping your machines clean and free of debris and contaminants goes a long way toward ensuring their reliability.
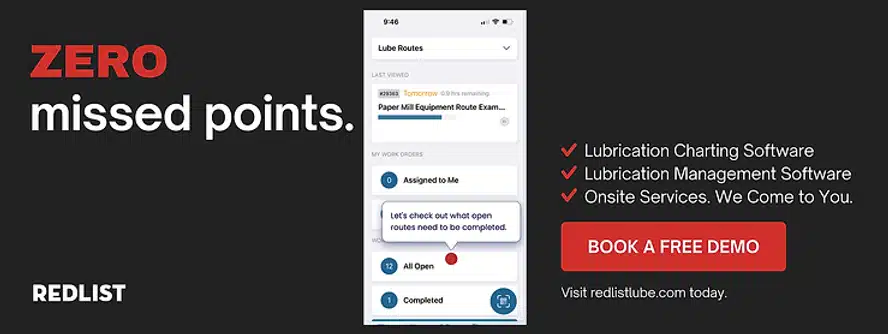
Lubrication Management: The Key to Machine Reliability
Without a lubrication strategy, your assets and components may not reach their full useful life. Secondly, you probably use more lubricant than you need, have more downtime, and must replace worn parts more frequently. However, lubrication-related mechanical failures are among the most preventable issues. Hence, proper lubrication is critical to ensuring you reach your machine reliability goals.