Vibration in machinery is a common issue that can be caused by a number of factors. As most manufacturers design equipment to avoid or minimize vibration, abnormal or excessive vibration can cause other problems or be a symptom of a problem. That’s why vibration analysis is a common tool for monitoring asset health. Tracking vibration patterns and catching anomalies means you can detect problems earlier and lessen unplanned downtime. In this blog post, we’ll discuss some of the most common causes of machine vibration, and how to troubleshoot and fix them. We’ll also cover some tips for preventing vibration in the first place.
Good vs. Bad Vibration in Machinery
While some vibration in machinery is expected and normal, that is not true for all vibrations. It takes some practice and monitoring for a length of time to gain an understanding of what is normal vibration for a piece of equipment. But, determining the threshold and noticeable difference between normal operation and early signs of problems is an essential step.
Why is Vibration so Important?
Not only is vibration in machinery an indicator of potential issues, but it can also cause other problems, including:
- Increase Component Wear Rates
- Decrease Bearing Life
- Equipment Damage
- Increase Operating Noise
- Safety Hazards
- Inefficient Power Consumption
- Decrease Quality Control of Products
- Equipment Failure and Unplanned Downtime
With the right tracking and analysis, vibration can be a critical resource as an asset health and reliability data point and a driver of preventive maintenance. Instead of discovering equipment problems after a catastrophic failure, your maintenance team can catch them early.
Common Causes of Vibration in Machinery
Wear
Deterioration of rotating components, such as drive belts, gears, and ball or roller bearings, can cause vibration in machinery. For example, pitting of a roller bearing race will create abnormal vibration every time they pass over the deteriorated area. Vibration from component wear will show up as an increase and a pattern change in your vibration analysis.
Imbalance
Another common cause is imbalance, either due to a maintenance issue or possibly a manufacturing defect. When it comes to rotating components, an imbalance will create a “heavy spot”. Then, as you turn on your equipment and get it up to operating speed, the impact of the heavy spot is more noticeable. Additionally, beyond causing vibration in machinery, an imbalance greatly increases bearing wear.
Misalignment
Different from imbalance, misalignment occurs when machine shafts are out of alignment. Misalignment may be from the assembly of equipment, inaccurate reassembly after maintenance, shifting components, thermal expansion, or it may simply develop with time. However, misalignment doesn’t only cause vibration in machinery. It also can lead to bearing failure or damage to couplings, shafts, and seals.
Looseness
Looseness may be the cause of your vibration if you have loose bearings or a component is not properly attached to its mounts. This is another condition that can develop over time, causing an increase in vibration in machinery. But, it’s also caused by improper assembly or reassembly after maintenance, similar to misalignment. Loose components accelerate wear rates and can cause even more damage as vibration increases.
Corrective and Preventive Methods for Vibration in Machinery
Implementing various best practices for preventive methods is always the best route. However, you may already have or still end up with vibration in machinery, which means you need to take corrective action. These are some of the best methods:
- Optimize your lubrication management – This will reduce component wear and lower operating temperatures, which helps prevent misalignment from thermal expansion.
- Replace worn bearings – As a critical component of rotating and moving parts, the health of your machinery is directly linked to the health of your bearings!
- Practice precision balancing and alignment – These are essential details at the first assembly and at every reassembly when your team performs maintenance.
- Regular inspections – This helps you identify any worn components that need replacement before they cause vibration in machinery.
- Last resort: Disassemble and reassemble – While you must be careful not to create a new problem or introduce contaminants, disassembling machinery can help you detect more challenging issues by visually inspecting and cleaning each part.
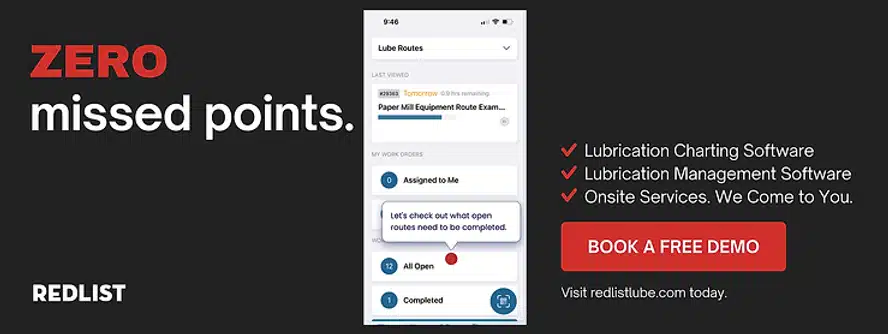
Vibration Drives Continuous Improvement
Machinery vibration is a serious issue that can cause extensive damage if left unchecked. By understanding the most common causes of vibration in machinery, you can take steps to prevent any issues before they start and extend the life of your equipment. Regular vibration analysis is key to keeping your machines running smoothly for longer, detecting problems before they become dangerous, lowering maintenance and repair costs, and decreasing equipment downtime. Additionally, vibration data can fuel the continuous improvement of your maintenance and lubrication management plans.