Some organizations spend money on a lubricant analysis program but lack the systems and processes to interpret the oil sample analysis results. To get the greatest benefit from your oil analysis, this is an essential step that you cannot skip. Your oil sample analysis results can provide important insights into the health and condition of your equipment. By taking the time to interpret your results, you can make informed decisions about how best to maintain your assets. In this blog post, we’ll discuss some tips for interpreting your oil sample analysis results.
Why is Interpreting Oil Sample Analysis Results Important?
Interpreting the results of oil sample analysis is important for a number of reasons. First, it can help to identify lubricant-related problems before they cause equipment failure. Second, it can help to optimize lubricant performance and extend lubricant life. Finally, it can help to improve equipment reliability and reduce maintenance costs.
Oil analysis is a key tool for preventive maintenance programs. By interpreting the results of oil sample analysis, you can diagnose lubricant-related problems and take corrective action to prevent equipment failure. Your test results can become the data that fuels your preventive maintenance tasks.
In addition to predicting lubricant-related problems, interpreting oil sample analysis results can also help to optimize lubricant performance. For example, if an oil sample shows that a lubricant is breaking down prematurely, changes can be made to the lubricant formulation or application methods to improve its performance. Conversely, if an oil sample shows that a lubricant is performing well, you can make changes to extend its life. Either way, interpreting oil sample analysis results is essential for optimizing lubricant performance.
Finally, interpreting oil sample analysis results can also help to improve equipment reliability and reduce maintenance costs. For example, if an oil sample indicates that a lubricant is contaminated, steps can be taken to clean or replace the lubricant before it causes equipment damage. Fewer breakdowns and early detection of issues mean that repairs will be smaller and less expensive. As a result, interpreting oil sample analysis results is an essential part of maintaining reliable equipment and reducing maintenance costs.
The Lubricant Analysis Problems Many Companies Face
A company finds a lab and sets up a lubricant analysis program. This includes tasking technicians with collecting samples. However, there are two major problems that often come next.
First, the lab is not integrated with the company’s internal systems in any way. So, the company receives a piece of paper or an email with the results. Multiply that paper or email across every piece of equipment you’re testing, and suddenly you have a backlog of oil sample analysis results to read. The administrative time required to process the information, decide on corrective actions and/or adjustments to preventive maintenance, and create the necessary work orders could be cut down considerably with integration to their CMMS (Computerized Maintenance Management System) or Lubrication Management software. This kind of integration includes automated alerts you can configure based on result thresholds, as well as easy work order creation right from the oil analysis report.
Second, nobody is fully prepared to analyze the results. One way to explain this is to compare it to getting bloodwork done at the doctor’s office. Your doctor doesn’t just hand you the results from the lab and expect you to know how to interpret them. Instead, your doctor, the trained expert, interprets the results and explains the findings to you. If you set up an oil analysis program and don’t either hire an expert to interpret the results or get training for employees to become experts, then you may have trouble reaping the full benefits of oil analysis. The training and certifications for this skill are a relatively minimal investment, especially compared to the potential financial impact of not interpreting your results.
Oil Sample Analysis Interpretation Tips
Make Sure You’re Reading the Right Report
Clerical errors can happen and samples or results are mixed up or sent to the wrong people. The last thing you want to do with a high-dollar value asset is change its preventive maintenance plan, only to find out you had somebody else’s oil analysis results. For good measure, take a couple of seconds to confirm the clerical data on your report.
Prioritize Your Oil Sample Analysis Results with the Most Critical First
Most labs typically mark the results with a rating system. Before interpreting any results, you must sort them by the level of criticality, especially if you have limited time to spend reviewing. Handle your critical results first, then the abnormal ones second. Any results with marginal changes likely don’t require much attention, so you can review those last.
Use Your CMMS or Lubrication Management Software to Pull Asset Maintenance History
When you’re interpreting the results for an asset, it’s helpful to compare the results to the maintenance history. This information may correlate with changes in the oil sample analysis, or it will at least help you understand that asset’s recent changes (including filter changes or top-offs).
Collaborate with Your Oil Analysis Lab
Your lab may provide a lab analyst who delivers your results with their recommendations. This is a great service, but keep in mind that the analyst is focusing on the chemical and physical tests and the potential problems they diagnose. You and your team are the ones who understand the operation and application of this equipment. Sharing this on-the-job knowledge of your assets with your lab analyst can help them better understand your needs and result thresholds.
Look to Your Condition Monitoring to Confirm Findings
If your oil sample analysis signals a problem with your equipment, check your other condition monitoring data to confirm. Vibration analysis and thermography may confirm the findings of the oil analysis. In that case, multiple feedback systems are alerting you of an issue in need of corrective action. Furthermore, performing root cause analysis would be the final step to ensure that you not only correct the surface issue, but you resolve the underlying cause.
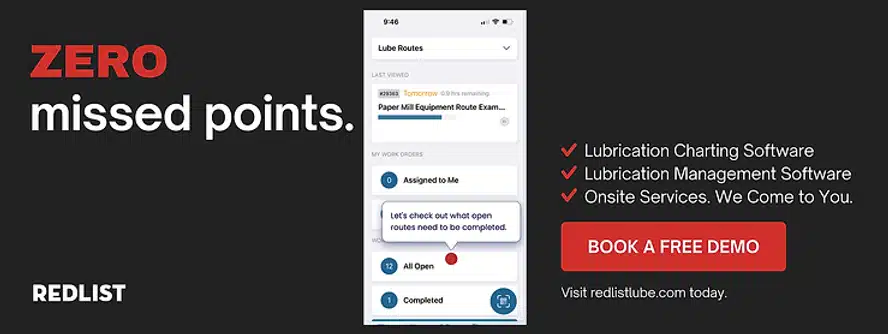
Timing of Oil Sample Analysis for the Best Lubrication Management
Lubricant analysis is meant to help you through the early detection of issues. When you optimize your lubrication management, your oil sample analysis results will typically still allow you plenty of time to put a plan of corrective action in place before equipment failure. But, it is difficult to tackle a backlog of reports, so don’t allow yourself to get complacent about interpreting your reports in a timely manner. Instead, create a routine of reading your reports regularly to stay on top of things. Doing so will enable you to be better equipped to keep your equipment running smoothly and prevent costly breakdowns.