As we shared in the recent webinar with reliability expert Tim Dunton, lubricant selection is the first step in maintaining a successful lubrication program. All efforts to store, apply or reapply lubricants properly are only useful if the lubricant is right for the machine or machine parts. Tim discussed the main lubricant properties you need to consider when choosing lubricants. In this post, we also look into the other factors that affect the success of your selection of lubricants.
What is a Lubricant?
But first, let’s define a lubricant and what it does. Knowing the purpose of lubrication is the best place to start when selecting lubricants for your specific needs. A lubricant or lubricating oil, often called lube in short, is any substance applied to protect machine parts from wear and tear. Lubricants form a thin film between machine parts, thus reducing friction and prolonging the machine’s service life.e
The majority of lubricants perform the following functions:
- Reduce heat by absorbing and transferring it
- Reduce energy needed to move machine parts
- Reduce wear from physical contact with surfaces
- Prevent chemical reactions that can damage surfaces
- Promote transfer and removal of contaminants
Essential Factors in the Selection of Lubricants
When selecting the ideal lubricants for your machines and other assets, it is critical to consider the following factors:
Lubricant Chemistry
As discussed by Tim in the webinar, the chemical properties of the lubricant have a significant influence on your selection. Such properties as viscosity, viscosity index, oxidative resistance, etc. result from the lubricant’s base stock, or base oil, and its additives.
The lubricant’s base oil is its main foundational ingredient. The base oils used for lubricants can belong to Groups I to V, as defined by the American Petroleum Institute (API). Each of the five base oil categories is identified by the source of the oil, manufacturing process, and chemical properties.
The addition of other components, called additives, into the base oil changes or improves its performance as a lubricant. The type, amount, and combination of additives depend on the initial properties of the base oil and the intended purpose of the lubricant.
Varying base oil and additive combinations result in unique lubricants with specific applications. Finding the ideal lubricant is easier if you first understand base oil and additive properties as individual components and as part of the whole lubricant product.
Machine Requirements
Next to understanding lubricant chemistry is knowing the lubrication requirements of your machine. Every machine has its ideal lubrication amount, type, and frequency. Machine manufacturers can set lubrication specifications for their products, but these can change depending on varying production environments:
- Operational intensity – Machines used more frequently and at intense workloads often have higher lubrication requirements than low-intensity machines.
- Exposure to elements – Exposure to wet or dry, hot or cold, and clean or dirty environments can also dictate the type of lubricant a machine needs.
- Safety – Machines for specific industries may require specific lubricant types. For example, machines used in making food products require food-safe lubricants.
Application or Use
When selecting the lubricants for your assets, you should also consider the process of applying or using these lubricants. Your lubricant choice depends on the accessibility of the machine parts. Some machine parts are easy to reach, while some need machine dismantling or special lubricating tools or systems to lubricate. Different application methods require varying lubricant types.
Maintenance Strategy
Considering your facility’s machine maintenance strategies is also critical to your selection of lubricants. The machine maintenance protocols and standard operating procedures (SOPs) already in place should allow the optimization of lubricants.
Expensive high-performance lubricants are ideal if your machine maintenance allows for lubrication-optimizing technologies such as automated filtration, filter connections, embedded sampling ports, etc. Otherwise, lubricants that are cheaper and easier to change or replenish are a better option.
Lubrication Costs
When selecting lubricants for your assets, it’s not enough to look at the cost of the lubricants. There are other costs to be considered, which include:
- Downtime costs – Includes money lost when stopping operations to replenish or replace lubricants or repair machines that break down due to poor lubrication
- Machine maintenance costs – Includes the cost of machine parts, tools, and other maintenance materials, as well as the salary of maintenance staff or expenses in hiring third-party technicians.
- Storage costs – Includes the overhead cost of storing lubricants, hiring staff to manage inventories, and loss due to expiration, contamination, or spillage.
- Workplace accidents – Using inappropriate lubricants promotes unsafe working conditions that can lead to costly accidents and loss of productivity.
Disregarding the costs listed above leads to choosing cheap lubricants that are actually costly. It helps to gather and compare these cost data with the lubricant cost. Saving on the lubricant cost may lead to more expenses for your facility.
Optimize the Selection of Lubricants with Lubrication Management Software
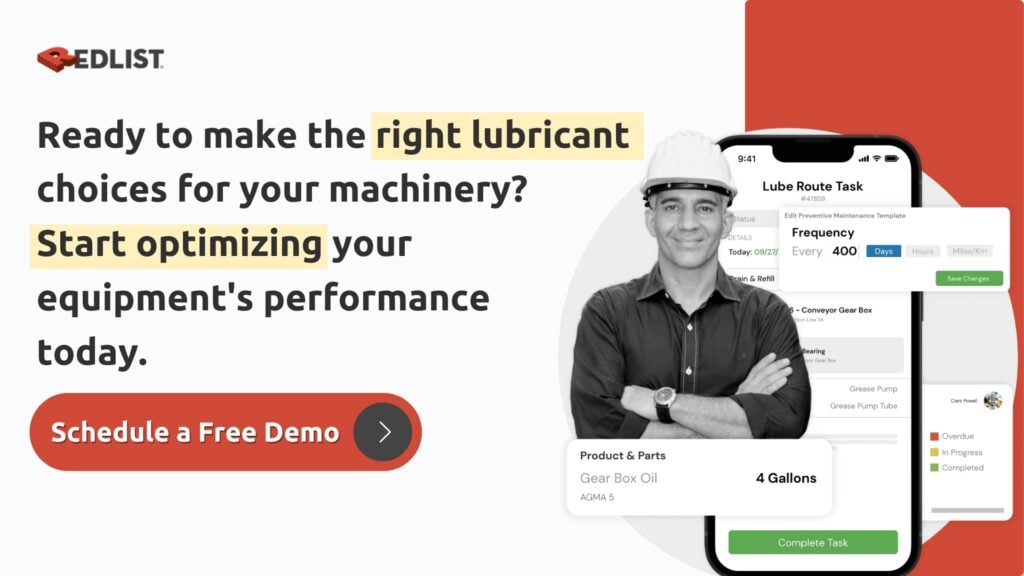
The selection of lubricants is the starting point of lubrication management, but it’s not a one-time-only step. Initially, you identify the ideal lubricants by considering the essential factors above. Next, you monitor the performance of your selection, and finally, you use these results to improve your lubricant selection and so on. This cycle is continuous because lubrication requirements will continue to change as machines age over time. A lubrication management software like Redlist is a valuable help in keeping up with this continuous cycle of selection, monitoring, and analyzing results. With digital recording and data entry, lubrication monitoring is fast, accurate, and has real-time results. With cloud-based storage, lubricant specifications and other essential data are available whenever needed. Redlist’s powerful computing technology also makes results analysis easier and selection decisions faster. To learn more about Redlist, schedule a free demo today!