In our recent webinar with reliability expert Tim Dunton, we discussed how lubrication depends on lubricant characteristics such as additive content. Additives constitute a small portion of the lubricant formula, but they play a major role in lubrication success. There are several types of additives, as we’ve discussed in our past blog post. And the correct way of using lubricants starts with understanding additive types. This post focuses on surface additives or additives specially formulated to protect surfaces from wear and tear.
Types of Surface Additives
The additives that protect metal surfaces include anti-wear agents, anti-corrosion additives, detergents, dispersants, and friction modifiers.
Anti-wear Additives
These are polar additives that attach to metal surfaces and react chemically during metal-to-metal contact. Anti-wear additives form a protective film that protects surfaces such as loaded metal parts from mechanical wear including adhesive wear, abrasive wear, pitting, and spalling. The most common anti-wear additives also have anti-rust and anti-oxidant properties that further protect surfaces from oxidation or rusting.
Anti-corrosion Additives
Corrosion is the result of chemical or electrochemical reactions between metal surfaces and their surroundings. Corrosion changes and weakens the chemistry of surfaces. Anti-corrosion chemicals inhibit the process of corrosion by passivation and neutralization. Passivation means blocking out water or air from getting in contact with metal surfaces. Neutralization means reacting with corrosive materials by reducing their alkalinity or acidity.
Detergents
These are alkaline or basic chemicals that protect surfaces by keeping them clean from metal deposits and by neutralizing acids formed over time. The most common detergents used as lubricant additives are metal compounds of calcium, magnesium, phosphates, and sulfonates. The metal components in detergent-based additives can react at high temperatures, leaving ash deposits that promote surface degradation. Thus, low-ash detergent additives are recommended for equipment operating at high temperatures.
Dispersants
Dispersant additives act similarly to detergents, protecting metal surfaces by keeping them clean of debris. They are commonly used in engine oils. Dispersants ensure that any insoluble particle of diesel engine soot is kept away from the surfaces by suspending them in the lubricating oil. Also, dispersants are typically ashless and often added to detergents for better surface protective effects.
Friction Modifiers
Also mostly used in engine oils and automatic transmission fluids, friction modifiers alter the friction between the engine and transmission parts. By reducing friction, friction modifiers increase fuel economy in engines and boost clutch engagement in transmission systems.
Surface Additives and Viscosity
The effectiveness of surface additives relies on viscosity. As Tim said in the webinar, surface additives do not matter if you don’t get the viscosity right. Surface additives fail to form a protective film on metal surfaces at low viscosities. Too high viscosity, on the other hand, promotes the deposition of contaminants and increases the risk of surface damage.
Furthermore, the amount and types of surface additives can increase or decrease the viscosity of lubricants. Surface additives can also react and reduce the effect of viscosity modifiers, or additive types that are intentionally added to improve the viscosity performance of a lubricant surface. Changes in viscosity can result from the chemical reaction and subsequent effects of wear and tear, affecting the performance of the surface additives.
Like all additives, surface additives degrade, and their amounts are depleted as the lubricant is used. The lubricant profile, or a lubricant’s overall additive content and viscosity, changes, increasing the risk of surface damage. The depletion of additives and change in viscosity often signal that lubricants need to be changed.
Optimize Surface Additives
The following are the ways to get the most out of your lubricant’s surface additives:
Consider the equipment operating conditions when selecting lubricants.
Exposure to contaminants like heat, water, and debris will affect the effectiveness of surface additives. Always choose lubricants with surface additives that are recommended for high-temperature or extreme-pressure usage, for example.
Follow manufacturer-recommended application methods and frequencies.
Surface additives are at their most effective if applied or reapplied correctly. Deviating from recommendations can result in damage to your machine or equipment surfaces.
Monitor and analyze lubrication performance.
A lubrication program will help you monitor lubrication properties and prevent early signs of lubricant issues such as viscosity increase, sludge formation, surface corrosion, and increased wear rates.
Use a lubrication management system.
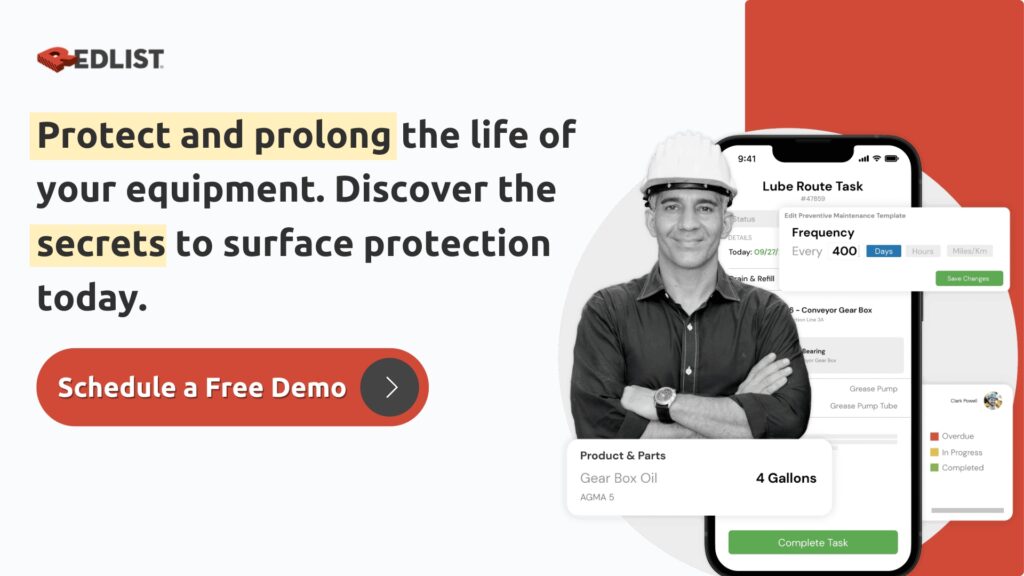
A lubrication management software like Redlist is an automated lubrication inspection and analytical tool. Designed for the efficient and effective implementation of lubrication management programs, Redlist can help select, monitor, and optimize lubricant performance for any industry. For more information, schedule a free Redlist demo today!