There’s no doubt that lubrication is a critical step to having long-lasting and reliable assets. Lubrication, however, is not as simple as applying lubricants and expecting beneficial results. Instead, lubrication or lube management is a technical and complicated process to ensure that lubrication achieves its expected results. One of the essential processes in lube management is lubricant health monitoring.
In this post, we discuss lubricant health monitoring and how a better understanding of this essential process is a step closer to better lube management and optimal lubrication. You will also learn about Redlist, a modern tool in lube management you can use to implement efficient and cost-effective lubricant health monitoring.
What is Lubricant Health Monitoring?
Lubricant health monitoring is the process of determining whether the lubricant in use remains effective in fulfilling its functions. That is, whether the lubricant is reducing friction on machine parts, improving efficiency, and reducing total operational costs.
Lubricant health monitoring is most often used synonymously with oil analysis. However, lubricant monitoring or assessing lubricant health is more than just performing lube oil analysis. Although it is the most common, lubricating oil analysis is only one of the methods used in lubricant health monitoring.
Why is Lubricant Health Monitoring Important?
Maintenance teams can use different methods and strategies to implement lubricant health monitoring and achieve the following benefits:
- Extend Asset Lifespan – Maintaining proper lubrication extends the lifespan of machines and similar assets. Without proper lubrication, assets’ surfaces experience friction that leads to damage and shorter lifespan.
- Reduce Maintenance Costs – Regular and consistent monitoring of lubricant health allows for timely reapplication or replenishment of ineffective lubricants. This helps prevent future issues that often require more serious and costly maintenance.
- Operational Efficiency – Lubricants reduce friction, in turn reducing the heat output and energy requirement of machines. Thus, maintaining lubricant health is beneficial in achieving optimum operational efficiency.
Areas of Lubrication Health Monitoring
Complete and effective lubricant health monitoring involves methods that look into the following critical areas of lubrication:
1. Intrinsic properties
The specific properties of the lubricant as a result of its formula dictate how the lubricant benefits an asset. Lubricant health monitoring must consider the intrinsic properties of the lubricant and how these change over time. Some examples of intrinsic properties monitored are the lubricant’s viscosity changes or additive depletion.
2. Lubricant contamination
Contaminants like fluids, dirt, debris, and other foreign materials mix or interact with the lubricant, affecting its properties and total performance. Lubricant health monitoring must consider all the types, sources, and modes of entry of contaminants into the lubricant or lubricating systems. Examples of monitoring for contamination include testing for water, impurities, and other particles.
3. Machine wear
The surfaces of machine part degrade and lead to machine failure when lubrication is ineffective. Lubricant health monitoring must consider all signs of machine wear caused by inappropriate, inadequate, or excessive lubricant use. Examples of machine wear monitoring include the presence of wear debris or particles, energy input, temperature or heat generation, etc.
Lubricant Health Monitoring Methods
The following are the methods used to implement effective lubricant health monitoring:
Oil Analysis
Routine oil analysis involves the laboratory testing of the oil lubricant’s properties, contaminants, and wear debris. This periodic testing can monitor the three critical areas of lubrication effectively. This method can be costly, requiring testing fees, lubricant samples, and considerable downtime. Additional testing may also be needed to confirm or investigate the initial oil analysis results. Furthermore, oil analysis results require expert interpretation to identify the necessary actions and make decisions.
Field Test
Field testing involves testing lubricant health on-site. The tests are more or less similar to regular oil analysis but often involve laboratory test kits, devices, and visual inspection by technical laboratory personnel. Depending on the type of testing performed, field-testing may be as costly as routine oil analysis. Field tests provide quick results and allow for fast decision-making.
Sensor Detection
Oil lubricant health can also be monitored with the use of sensors installed in the machine’s lubrication system. These sensors provide continuous or frequent data on the properties of the lube while in use. This monitoring method requires investing in the sensor system but can save on other costs of downtime and maintenance. Detection with sensors offers instant and actionable oil health results, but sensor precision can fail. Thus, this method is not meant to replace routine oil analysis. However, it can be beneficial for minimizing the need for frequent oil analysis and implementing predictive maintenance strategies.
Custom Analytics
Maintenance strategies may require additional lubricant health analysis to collect specific information. Lubricant conditions may be analyzed to provide information for root cause analysis, product characterization, and other maintenance management purposes. The cost of custom analytics can vary depending on the type and extent of testing involved.
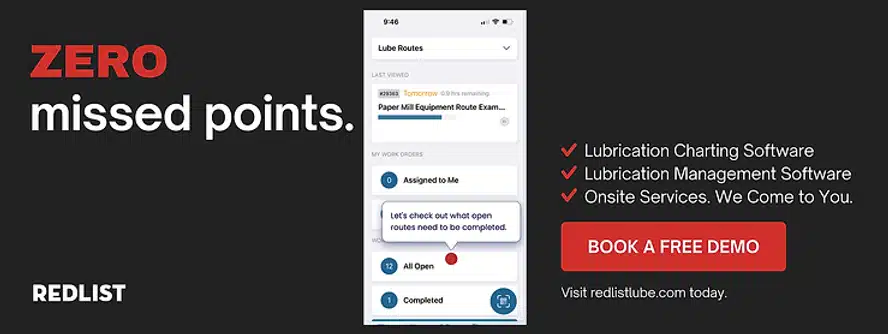
Redlist Lubrication Management Software Solutions
Lubricant health monitoring acts as an early warning system and diagnostic step for machine failures. Redlist is a valuable tool for a robust and beneficial lubricant health monitoring program. With our Lubrication Management Software, you can streamline your lube condition monitoring and gain actionable insights for better decision-making. To achieve these goals, Redlist comes with the following features:
Real-Time Monitoring
Redlist digitizes information for real-time data on everything lubrication-related. Thus, lubricant health monitoring is more straightforward, empowering you to take timely actions to prevent equipment failure.
User-Friendly Interface
Redlist offers a simple, user-friendly interface that even people without technical expertise can navigate effortlessly. Thus, users can better collaborate and share information from multiple perspectives, achieving efficient lube management.
Data Analytics
Redlist’s powerful analytics are useful for predicting future lubricant behaviors and machinery health. Redlist can let you gather data from multiple sources, such as oil analysis results and sensors, and organize these into easy-to-interpret and actionable reports.
Cloud-Based
Redlist’s digitized database lets users access lubrication monitoring data anytime, anywhere. This can be useful when you need to check for historical oil analysis results while field-testing, for example. You can report oil conditions faster, receive lubrication instructions in the field, and many more.
With these features, Redlist can become an indispensable partner in your journey toward better lubricant health management. Don’t take our word for it. Book a free demo today and experience how Redlist can revolutionize your lubrication management strategy.