In the world of maintenance management, work orders serve as the backbone of operations, ensuring seamless coordination and asset reliability. However, managing these work orders manually can be a labyrinth of paperwork and administrative burdens. Enter automation—the game-changer that promises efficiency, accuracy, and productivity.
Dive into our guide on Automating Maintenance Work Orders: Benefits and Steps, where we unravel the essentials of streamlining your maintenance processes with innovative solutions like Computerized Maintenance Management System (CMMS). Discover the transformative power of automation and embark on a journey toward enhanced operational excellence.
Maintenance Work Order Basics
First, what is a work order? Work order is the general term for the formal documents that initiate, track, and record all the maintenance activities in an organization. Work orders communicate information among managers, technicians, and other relevant personnel involved in the maintenance process. The information in a work order must include the following:
Work Description
A work order must describe the maintenance task to be performed. A work description must also come with specific information such as the machine or equipment involved, type of maintenance (whether preventive, corrective, etc.), and other special instructions.
Asset Details and Location
A work order must include relevant information on the asset to be maintained including the model, serial or identification number, and maintenance history. The location of the asset and the maintenance location (if the asset is to be relocated for maintenance) must also be identified.
Technicians Assigned
A work order must contain the name or ID of the technician or maintenance personnel responsible for completing it. Assigning technicians to work orders ensures task accountability and makes progress tracking easier.
Date and Time
A work order must specify the planned date and time for the completion of the task. This information is critical for securing the required resources, scheduling operations, minimizing downtime, and meeting service-level agreements (SLAs).
Resources Required
A work order must specify the required time, labor, materials, tools, external services, and other resources to complete the task. Doing so minimizes delays and guarantees the efficient completion of the said task.
Priority Level and Authorization
A work order must identify the priority level of the task at hand and come with the approval of relevant authorities. Assigning priority levels helps in the effective allocation of resources and work scheduling. On the other hand, securing authorization for each task helps manage tasks that require significant costs, operational impacts, or safety risks.
Safety Considerations
A work order must include relevant safety precautions or instructions for the technician or involved personnel to follow while completing the task. This is to ensure the well-being of anyone involved and to comply with occupational health and safety regulations.
Completion Notes
A work order must allow the technician to report on the details of the completed maintenance task. After the completion of a maintenance task, the technician writes notes on the work order detailing the task performed, any issues encountered, and recommendations for future tasks. The completion notes serve as records of the task and provide valuable insights for improvements and future planning.
Benefits of Automating Work Orders
Work orders may seem a simple part of the maintenance process, but creating, completing, and filing these documents is a time-consuming process. In fact, work order management takes up the bulk of the total hours spent on maintenance administrative tasks. Freeing up some of these hours lets technicians complete more maintenance tasks and allows managers to focus their time on maintenance planning and strategizing.
Work order automation leverages technologies such as software applications and AI (artificial intelligence) or machine learning to streamline work order processes and improve efficiency. Automating work orders shortens completion time, improves reporting accuracy, and increases productivity.
Let’s face it. The manual system just doesn’t work. If you can essentially eliminate the manual data entry and all the hours that go with it, then you’re on the right track to getting the most benefit from your data sources.
The benefits of automating work orders include:
- Easier to collect the information you need
- Improved data accuracy
- Effortless reporting process
- More reliable reporting that you can actually use for decision-making
- Higher efficiency and productivity
- Increased uptime
- Decreased costs from eliminated data entry hours and the decrease in downtime
Steps to Automate Your Work Orders
Now that you know why you should do it, below are the essential steps to automate your entire system:
1. Select a software solution.
The type of software you choose depends on the functionalities you need and budget restrictions. Choose an affordable and customizable CMMS like Redlist that can conform to your present needs but can easily be modified for potential changes in the future as your business evolves.
2. Create work order templates.
Identify the maintenance tasks you need and create standard templates for these on the system. These standard templates must include the necessary information in a work order as discussed above. Redlist’s CMMS comes with standard templates that can be modified to suit your specific processes and requirements.
3. Integrate with relevant asset management systems.
Integrate your chosen work order management software to get a seamless asset management system. Redlist can integrate with a variety of software systems. It can also accommodate integrations with sensors, laboratory, and field inspection systems to facilitate the auto-generation of work orders.
4. Set up mobile access.
Equip mobile devices with software applications to allow technicians remote access to the system. This will allow field technicians to access work orders, update statuses, submit reports, and communicate in real-time. Redlist’s CMMS and all its maintenance management solutions are set up for mobile access.
5. Enable automatic work order generation.
Identify the criteria that will automatically generate work orders without the need for manual input. These criteria depend on your specific processes, but the most common triggers include calendar schedules, sensor data, and equipment readings.
6. Implement a system for prioritizing work orders.
An effective prioritization system helps you allocate resources effectively and tackle urgent tasks immediately. You can prioritize work orders based on operational needs or impact, resource availability, safety, and regulatory compliance.
7. Allow a self-service function.
A self-service function lets a user issue and resolve maintenance requests directly. This minimizes administrative overhead and promotes faster issue resolution.
8. Record and analyze performance.
Automating work orders also comes with automated data capturing and reporting. Redlist, for instance, comes with key performance indicator (KPI) tracking and other metrics. Use this data to identify trends, improve processes, and make data-based decisions.
9. Review and improve.
Conduct a regular review of current maintenance processes to refine and improve them. Identify these areas of improvement from work order feedback and the generated performance data. By implementing continuous improvement, you ensure that your automated systems remain effective and relevant to your current goals.
10. Train and maintain support.
Automated software systems undergo continuous evolution due to changing business demands and technological advancements. Ensure that users of your CMMS or similar software remain competent in using the software through training and ongoing support.
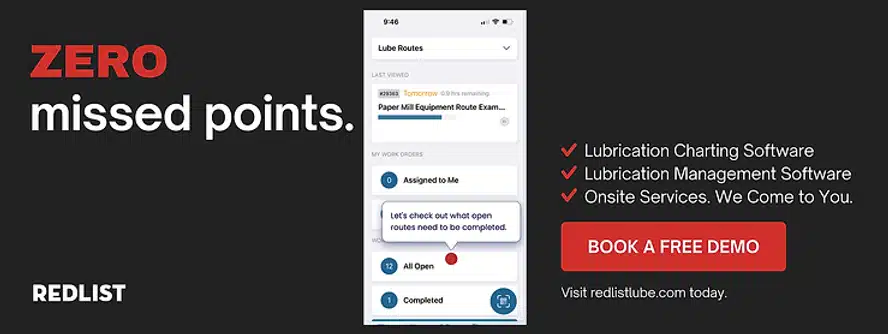
Manage Maintenance Work Orders with Redlist’s CMMS
Choosing Redlist to automate your work orders comes with the above benefits and more! Enjoy the benefits to your organization through reduced costs and downtime, and most importantly, happier employees due to their more efficient workflow. Propel your maintenance and business processes forward and automate with Redlist today! Book a free demo to learn more.