Equipment reliability, or the ability of equipment and other assets to perform as intended, relies on the effective implementation of programs consisting of complex processes. The success of these programs, in turn, depends on effective management and leadership. Although both management and leadership skills are critical, leadership behaviors are often neglected. In this post, we look into key leadership behaviors managers and leaders must exhibit to effectively implement equipment reliability programs.
Leadership Benefits for Equipment Reliability Programs
Management means directing and controlling people and other resources, while leadership means influencing and guiding people to achieve set goals. Although both skills are equally valuable for unstoppable equipment reliability programs, leadership has the following distinct benefits over management:
Inspiration vs. Instruction
Managers focus on achieving set equipment reliability goals by instructing people. Leaders, on the other hand, create a shared vision and inspire people to work towards that vision. Thus, leaders are more likely to energize and motivate their teams than managers.
Innovation vs. Stability
Managers focus on the correct implementation of existing equipment reliability programs, while leaders encourage creativity and innovation. Leaders welcome change, take calculated risks, and are always improving on existing processes. Thus, leaders help programs and processes evolve and stay relevant.
Empowerment vs. Assignment
Managers assign tasks and ensure people follow them. Leaders seek to empower people by helping and supporting their personal growth and development. Thus, leadership provides autonomy and a sense of ownership over the equipment reliability program, which are critical traits for technicians to have.
Long-term vs. Short-term Goals
Managers focus on the correct implementation of day-to-day activities and achieving short-term goals. Leaders look at the bigger picture and strategize about reaching the company’s long-term equipment reliability goals. Thus, leadership helps propel the organization forward and support its growth.
Relationship Building vs. Coordination
Managers help meet deadlines by coordinating people, materials, and other resources. Leaders, however, are focused on building strong relationships with team members, other leaders, and stakeholders. Thus, leadership promotes collaboration, trust, and loyalty within the organization.
Critical Thinking vs. Troubleshooting
Managers follow set instructions when dealing with failures and unexpected disruptions. Leaders can employ critical thinking to identify better solutions that deal with equipment reliability setbacks. Thus, leadership helps an organization be more adaptive and resilient against future problems and challenges.
Leadership Behaviors for Equipment Reliability Programs
For equipment reliability programs that meet an organization’s bottom line, the following are the key leadership behaviors that managers and leaders must exhibit:
1. Resolve
Leaders demonstrate resolve when executing and improving against expectations. Without such determination or firmness of purpose in their leader, team members are more likely to entertain doubt and second-guess their actions, thus preventing them from reaching their full potential.
2. Motivation
Leaders motivate others, using rewards and other means, to achieve desired results. Leaders must know the many ways to effectively motivate someone and know when to use them.
3. Recognition
Leaders recognize those doing the work, thus motivating them to carry on and encouraging others to do the same. By doing so, leaders direct everyone to contribute to the achievement of the common equipment reliability goal.
4. Inclusiveness
Leaders promote teamwork by including employees across all levels of the organization when implementing equipment reliability programs and work standards. By including everyone, a leader strengthens the team and increases the chance of success.
5. Innovation
Leaders provide a climate of innovation by pushing for continuous improvement and promoting engineered risk-taking. In addition, they promote a culture where the “human factor” is essential and that mistakes are learning opportunities rather than a reason to punish people.
6. Communication
Leaders guarantee the success of any equipment reliability program by ensuring that the right information reaches the right person. Recognizing that there is always a risk of miscommunication along the line, leaders minimize this risk by maintaining continuous and direct information transfer.
7. Development
Leaders are committed to people development. They are always open to sharing their knowledge and other resources to ensure that people grow and keep improving themselves.
8. Observation
Leaders are keen observers and can analyze current conditions to identify appropriate actions to achieve their equipment reliability goals. They know that decisions and actions must be based on actual data to be effective.
9. Failure Analysis
Leaders seek to understand the main cause of failure instead of creating a culture of blame. They promote failure analytical methods like root cause analysis that look into failures objectively and maximize improvements.
10. Proactive
Leaders focus on proactive actions against equipment or asset failures. They do not wait for a failure or negative situation to happen. Leaders implement preventive actions and prepare for any eventualities in case they happen.
11. Presence
Leaders lead by example. This is only possible if they maintain a constant presence in the workplace. Through constant contact with employees, leaders show their commitment to achieving the shared goal.
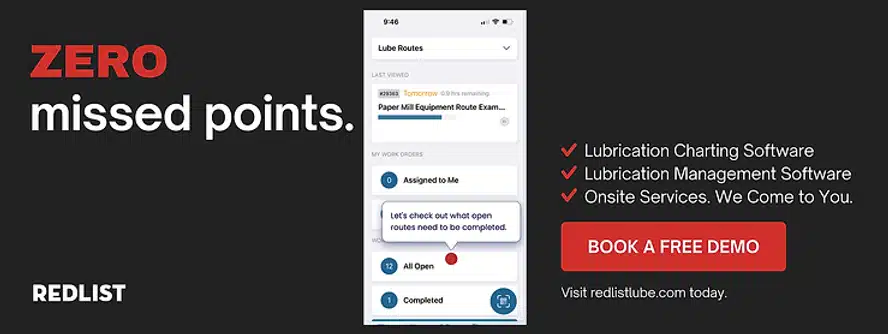
Redlist: Software to Optimize Your Equipment Reliability Program and Support Your Leaders
Reinforce your leadership skills with Redlist, a powerful computerized maintenance management system (CMMS). With Redlist, leaders have the ideal platform to connect and interact with team members along with these benefits:
- This software works for both desktop and mobile devices, helping leaders connect with team members anytime, anywhere.
- Redlist is user-friendly and intuitive, so employees from every level can use it and easily access essential information.
- Leaders can achieve better information transfer and communication with real-time updates and notifications on maintenance tasks, inventories, and other areas.
- The accurate recording of maintenance processes helps leaders track employee performance easily and access historical data on assets. These data help leaders identify the appropriate actions and make decisions faster.
- Finally, Redlist’s powerful analytics let leaders evaluate current processes or understand failures. By generating useful and insightful metrics, Redlist helps leaders identify further improvements. This ultimately promotes continuous innovation of people and processes.
Redlist is a must-have for all your management, leadership, and equipment reliability program requirements. Schedule a demo with Redlist and boost your leadership today!