Deferred maintenance, also called backlog maintenance, is any canceled or postponed maintenance task. Deferring tasks is a common practice in any industry. One of the critical responsibilities of the maintenance department is to maintain these tasks at manageable levels. Otherwise, the delay in the completion of these tasks can lead to negative consequences such as high maintenance and operations costs, poor asset performance, and risks to employees’ health and safety.
The success of maintenance in achieving optimum asset reliability depends on its ability to control the amount of deferred maintenance. This post will discuss the essential steps in reducing deferred maintenance and keeping its level under control.
Understanding Deferred Maintenance
Before you execute the necessary steps to decrease the amount of deferred maintenance, you need to understand several things when dealing with the tasks involved. Here are essential notes to remember when dealing with deferred maintenance:
Identifying the root cause of deferral is crucial.
You can limit deferred tasks only when you address the main reason for postponing them. Recurring asset failures or problems mean that there is a failure to address the root cause of these problems.
Inadequate time or lack of personnel are never the root cause of deferred maintenance.
If you find that your maintenance keeps deferring tasks because you are short on time and people to do them, you must investigate further. The lack of time and manpower can be a result of other factors that you can control. Factors such as time and personnel mismanagement, overscheduling of tasks, lack of preventive maintenance, etc. can be the root cause of the lack of time and manpower.
Effective inventory management can make a big difference.
Tasks are often deferred due to a shortage of maintenance parts or materials. Tasks are less likely to be deferred if these parts and materials are always on hand and available.
Prolonged deferral of tasks results in more costs.
The longer you wait to address an issue or complete a repair, the worse they become and more expensive to deal with. The costs of downtime and repair will also be higher the longer you defer these tasks.
Decrease Deferred Maintenance in 5 Steps
Follow the following steps to decrease the number of deferred maintenance in your facility:
1. Create a log of maintenance activities.
Any maintenance activity you perform on an asset provides valuable information for decreasing deferred maintenance tasks. A log or record helps track the progress of these activities, making it easy to resolve the completed tasks and follow up on the pending ones.
A log of maintenance activities also provides details such as completion time and date, costs to complete, specific findings, recommendations, and many more. These details are critical for developing effective maintenance plans and efficient work schedules. These effective plans and achievable schedules are the foundation of a low number of deferred maintenance. The easiest way to achieve this step is to implement a CMMS, or computerized maintenance management system. It can automate and streamline much of the data collection and reporting necessary to draw conclusions from your log of maintenance activities.
2. Assess and audit current processes.
Before you can decrease a long list of deferred maintenance tasks, you must have a firm grasp of the current state of your maintenance processes. By answering the following questions, you can gauge the status and scale of your current maintenance operations:
- What are the warranties in effect on your assets? Are there expired or about-to-expire warranties?
- Are there assets that experience frequent failures? At what frequency? Are these failures often unpredictable or unexpected?
- Which asset failures are a threat to employee health and safety? Are any asset failures impacting staff schedules and availability? Which asset failures are affecting the quality and quantity of your products and services?
- With an unlimited budget, personnel, and time, which tasks or activities do you want your maintenance team to accomplish?
3. Organize and prioritize tasks.
If you have executed steps one and two properly, you will have a list of tasks with varying impact, importance, and criticality. In a perfect world, you would have an unlimited budget and resources to complete them. Sadly, that is not the case. Thus, you must sort these tasks and prioritize accordingly to stay within your department’s budget and capability.
One of the more useful ways of categorizing maintenance tasks is by these two types:
- Tasks that need immediate attention – The tasks that need immediate attention are those that you need to complete to resume the normal operations of a facility. Other tasks under this type include those that cause irreparable damages or unsafe conditions if not resolved immediately.
- Tasks that can be delayed – These tasks are not as critical or impactful as those of the first type, but they still require action within a specific timeframe. If these tasks are not addressed within the set time, they can get worse and increase in criticality, demanding more immediate attention.
Other ways to sort and prioritize maintenance tasks are by cost requirements, time and location, logistics and dependencies, asset life cycle, and maintenance provider (whether in-house or third party). By considering different ways to categorize these tasks, you can devise more options to prioritize and complete them.
4. Develop or improve preventive maintenance (PM).
An ounce of prevention, as the saying goes, is worth a pound of cure. Developing an effective PM program or improving on your current one can result in a significant reduction of your emergency or unexpected tasks. PM tasks are also easier to schedule and reschedule, resulting in a much more flexible timeframe for your maintenance activities.
Start by reviewing your log of completed and backlogged tasks for each asset. Group the tasks that are related to each other and identify the PM tasks to address them. Implement the PM task and monitor its effects on the recurrence of failures or additional maintenance or repairs. Record all notes and findings for future reference.
5. Create a new budget and secure additional funding if necessary.
Plan your maintenance tasks and create your budget accordingly. Use the information you gathered from each of the above steps to allocate your resources and justify any additional funding you may need. The maintenance budget is rarely considered a top priority and is almost always the first to suffer from budget cuts. You can convince your company to increase your budget if you can show them results-based data proving a significant return on their investment (ROI) if they invest in a higher maintenance budget.
The most common ROI of a higher maintenance budget are increased productivity, higher revenue, reduced long-term maintenance costs, capital savings through a longer asset life span, and many more. Adequate funds and resources, and consequently, less deferred maintenance, await if you present a budget with the potential ROIs included.
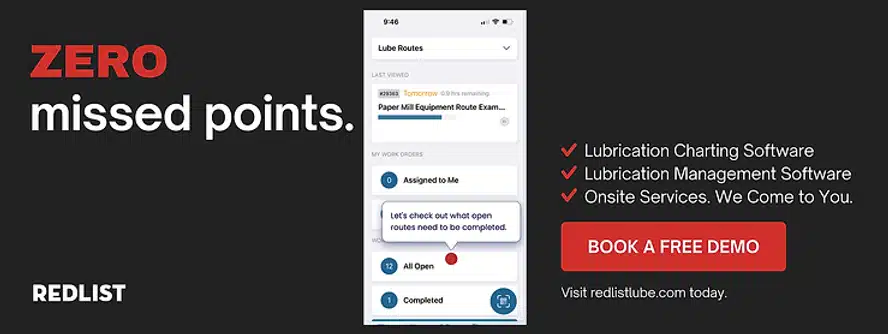
Deferred Maintenance Support From Redlist’s CMMS
Controlling deferred maintenance requires modern solutions. Manual and spreadsheet-based maintenance methods are no longer enough. Redlist’s CMMS is the ultimate support you need when dealing with backlog and deferred tasks. Redlist provides support through fast and accurate data collection, real-time task planning and scheduling, digitized and automated resources management, and intelligent analysis and reporting.
With Redlist, the complex steps we discussed above become the five easy and guaranteed steps to keep your maintenance backlog under control. Learn more about how CMMS can help you decrease deferred maintenance by scheduling a demo today!