Availability and reliability of assets is essential to your business. That’s why mean time between failures is a metric to track. It is where availability and reliability meet.
Mean time between failures or MTBF measures the operating time between one asset or component failure and the next.
That’s the basic definition, but that would lead you to believe that the metric goes from the point of failure number one to the point of failure number two. Actually, MTBF is from the point that the asset is repaired and operational again after failure number one to the point of failure number two. MTBF does not include the time that the asset is down for repair.
Why this is a Metric to Track
The knowledge of your asset’s runtime expectations before an unplanned breakdown is useful in understanding asset availability and reliability. Knowing the mean time between failures can help you plan inspections and preventive maintenance. You can use MTBF to expect an unexpected breakdown, which reduces your mean time to detect and mean time to repair. This leads to an overall reduction in unplanned downtime and a reduction of the costs associated with that.
How Do You Measure Mean Time Between Failures?
First of all, you have to get clear on what failures to include in the measurement. MTBF is only used for unexpected downtime of repairable systems. So, you will want to exclude any downtime for preventive maintenance. The calculation for MTBF is the total operational time divided by the total number of failures. For example, an asset has a total operational time of 3,000 hours in one year and broke down twice. Its mean time between failures is 1,500 hours. However, it is helpful to have a large amount of data to ensure that you have a relatively accurate MTBF.
What is a Good MTBF?
The higher the MTBF, the better. This is similar to mean time to failure (MTTF) because they are the opposite of most maintenance metrics where lower is better. A higher mean time between failures means the asset will operate for a longer period before failing. Your MTBF calculation will get more accurate for you and your organization as you collect more data on your assets. With time, you will learn what is a good MTBF for you. Some factors can throw off your MTBF, including mishandling the asset or a repair job that wasn’t executed properly.
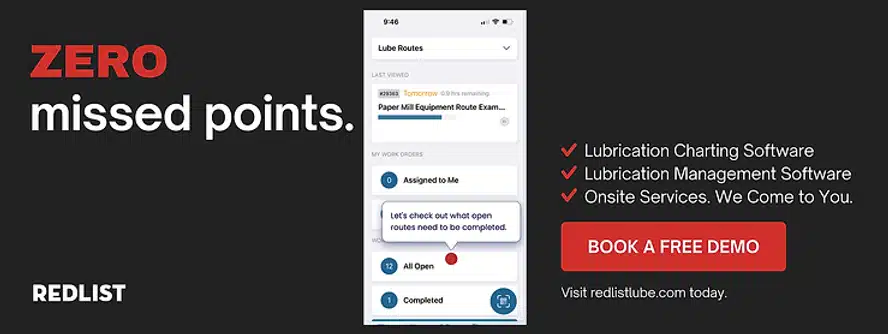
How Do You Improve Mean Time Between Failures?
By tracking this metric, you have an opportunity to take a deeper look at the assets with a short MTBF. These are some actions you can take to improve their mean time between failures:
- Increase the frequency of inspections — Your technicians may identify a soon-to-be failure before it happens to speed up detection, repair, and reduce the necessary downtime.
- Review and revise the preventive maintenance schedule — Is the asset failing often due to improper lubrication or a need for recalibration? Improving preventive maintenance can reduce the need for reactive maintenance.
- Make changes to inventory management — Not all replacement parts are created equal. Is there a component causing the repeated failure that you could improve the quality of to reduce the breakdowns?
- Check the operating conditions — An asset could be failing more than expected due to environmental conditions such as heat, pressure, and humidity. Or, other conditions like operating it beyond its parameters or human error that could be resolved with additional training.
If you would like to put your MTBF metric to work for you, Redlist can aid you in doing so every step of the way. Our software offers a highly efficient process for you to collect the mean time between failures data, auto-generate a report, and support you in the actions to improve your MTBF and reduce downtime events. Whether that means an automated preventive maintenance schedule, lubrication charting, employee training, or providing precise instructions on how to do repairs properly, you will be well on your way to improving MTBF with Redlist.