Quality control (QC) is a process for ensuring that a product meets the required standards. In other words, it is a way of making sure that the products produced by your company are of the correct quality. QC is important because it helps prevent manufacturing defects and ensure that the products produced are fit for their purpose. There are many different QC techniques that you can use. However, the most appropriate technique will depend on the products you manufacture and the nature of the manufacturing process.
The Importance of a Quality Control Process
When manufacturing plants receive raw materials on their dock, a strict quality control process is usually in place to check these materials before they go to the production lines. Companies pay a lot of money for these materials, and expect them to be in good shape so that there are no manufacturing flaws in the finished product. With high prices and expectations, shouldn’t lubricants also receive close attention to quality?
If a manufacturer receives raw materials in poor condition, it can create flawed products. Similarly, if you receive lubricants in less-than-ideal conditions, it can result in poor performance, damage to machinery, and reduce reliability. This increases the risk of machine failure, which will lead to an increase in cost. Not only will you experience time wasted on corrective action, but also missed production hours because productivity dropped during repairs.
How to Create a Quality Control Process
The first step when starting a quality control process is to list out the goals of the program:
- What are you trying to accomplish?
- What tests are you going to use to verify success?
- Is the program going to go as far as performing in-depth oil analysis on incoming lubricants?
- Or, are you just going to physically inspect the deliveries?
Once you have determined the scope of your quality control program, you need to establish how you will measure success. This may involve setting up standard operating procedures (SOPs) and methods for tracking and documenting results. Additionally, you will need to determine who will be responsible for carrying out the quality control tests and how often they will conduct them. By clearly defining the goals and methods of your quality control process from the outset, you can ensure that your program is effective and efficient.
Typical Steps in a Quality Control Process
When establishing your quality control process, consider these common steps and procedures.
Receiving Times
As any business owner knows, quality control is essential to ensuring that products meet customer expectations. In the case of lubricants, it is important to receive deliveries in a timely manner. This step doesn’t check the quality of the lubricants themselves but instead shows the quality of the supplier. If a single delivery is a bit late, you can probably excuse that. However, if deliveries are consistently late, you might want to consider switching suppliers.
Accompanying Documents
In order to establish quality control processes and document your findings, it is important to request specific accompanying documents from your lubricant supplier. A quality certificate or certificate of analysis will include details such as when the last sample date, the analysis of the additives, and the particle count. This information will help you verify that the product meets your standards and requirements. Additionally, you may also request a record of the last audit of the blending plant or supplier. This will ensure that you are working with a reputable and reliable source. By requesting these documents, you can be confident that you are receiving a high-quality product that meets your needs.
Visual Inspection
One of the steps in quality control is to ensure that you receive the correct lubricant in the right container. You should inspect the container for any points of possible contamination. Also, you must check the label to make sure that you have the correct lubricant. It is also important to confirm that the lubricant is not expired and that it falls in line with the shelf life of the quality control program.
If you order bulk lubricants, you should inspect all transfer equipment to ensure proper storage and that there will not be any contamination of the lubricant. Also, you should flush the equipment before delivering the lubricant to the bulk tank.
Oil Analysis
When it comes to maintaining the quality of your lubricants, oil analysis is a critical step. Depending on the volume of lubricants and how critical the machinery is, you may want to test all incoming lubricants. This can be done on-site or by sending them to a laboratory for more in-depth testing. There are a few on-site tests that you can perform, such as:
Viscosity
When it comes to lubricants, viscosity is king. This is the single most important property of a lubricant. If the delivered product is not the correct viscosity, you should return it for a replacement. Establishing quality control processes is key to ensuring that the delivered lubricant is up to par. Here are the steps to take:
- Get a visgage – This relatively inexpensive tool will help you test the viscosity of the lubricant on-site.
- Establish what range of viscosity is acceptable for your application.
- Use the visgage to test the delivered lubricant – If it falls outside of the acceptable range, send it back.
Particle Counting
Particle counting is a way of measuring how clean or dirty the tested lubricant is. Just because the oil is new doesn’t mean the oil is clean. Particle counters help you to know what is in the oil, and you can get a report within minutes. Having on-site particle counters helps you to save time and money while maintaining the quality of your lubrication program.
By performing these simple tests, you can establish a quality control process for your lubricants.
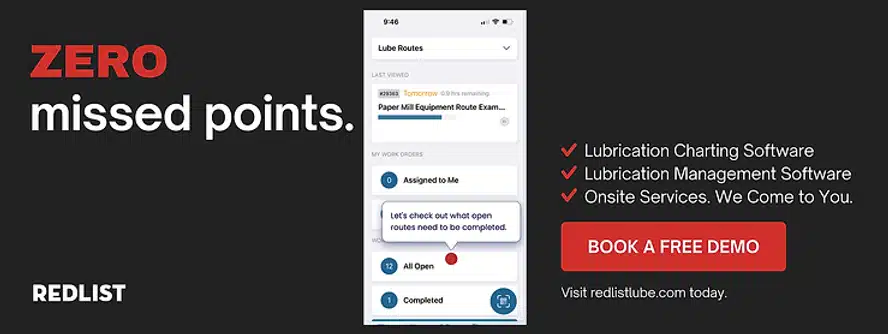
What To Do If Lubricants Fail?
In any manufacturing or industrial setting, quality control is key to ensuring that products meet the necessary standards. This is especially true for lubricants, which play a vital role in keeping machinery running smoothly. To ensure that lubricants meet the required standards, it is essential to establish quality control processes. These steps should be created in collaboration with your supplier and should be clearly defined based on the tests that the lubricant fails.
For example, if a lubricant fails a viscosity test, the steps for addressing this issue should be clearly defined. Once a lubricant is rejected, we should receive a replacement lubricant within a specified timeframe to help avoid using the failed product. By establishing clear quality control processes and steps, you can help ensure that only the highest-quality lubricants are used in your machinery.