The success of a business depends on the effective implementation of departmental policies and procedures. The maintenance department’s policies and procedures are critical in ensuring compliance and safety for all employees. This article lists tips or steps the maintenance department can take to ensure compliance and safety within its operations.
1. Document All Maintenance Department Policies and Procedures
Recording and analyzing historical data is fundamental to any maintenance department’s decision-making process. With adequate documentation, you consider actual data from maintenance tasks and employee feedback. As a result, you can draft policies and procedures that fit into your current or unique maintenance operations, ensuring a higher degree of compliance and safety.
Putting all your processes down in writing also promotes accessibility and standardization. Written communications provide clearer and more consistent instructions for your employees than verbal ones. In addition, employees find it easier to recall and follow instructions if they have read them in black and white. Documents allow less room for misinterpretation or errors, and employees can review them easily to refresh or confirm any missed information.
2. Create Detailed Maintenance Programs
Compliance depends on clear maintenance plans that provide as many details as possible. Employees need to know the whys and the hows before they can fully comply with these programs. Low compliance and unsafe environments happen when employees are not fully aware of the essential details of maintenance policies and procedures.
Ensure compliance and maintenance safety by including these details in your maintenance program:
- Scope of tasks and responsibilities involved
- Hazards or the risks associated with such tasks
- Resources or the materials, tools, labor, etc. needed for implementation
- Safety requirements or the necessary precautions to prevent accidents
- Communication or the flow of information transfer and decision-making
- Trouble-shooting or the process of identifying issues and resolving them
3. Maintain Consistent Implementation
Inconsistent implementation of policies and procedures results in low compliance and safety risks in the maintenance department. All instructions you issue should apply to everyone and for all position levels. Allowing exemptions and special considerations lowers the credibility and usefulness of your policies and procedures.
To maintain consistent implementation of policies, you must review them regularly with your staff. This way, you can discuss and troubleshoot issues together and devise revisions everyone can support. You improve employee compliance and cooperation by involving them in the decision-making process.
4. Provide Adequate Resources
Unavailable or inadequate resources also result in non-compliance and safety risks in the maintenance department. Employees are more likely to ignore safety rules if they do not have the materials or equipment to follow them.
When evaluating maintenance resources, the task-specificity of tools and materials is critical. Every task and work order requires a particular set of resources to complete. The maintenance department must have a standard list of these requirements and keep them available to ensure employee compliance and safety.
5. Provide Regular Training
Training reinforces your policies and procedures by letting employees understand or discuss them. Training is the best way to improve familiarity, gather feedback, and provide regular updates. It is also the best venue to draw out and address any negative issues that otherwise lead to increased non-compliance or safety risks.
Conduct regular training to refresh information and increase retention of your policies and procedures. Although training is the best place to address negative issues, dwelling on them and blaming employees is not beneficial. You must focus on the positive and create a training environment that is not fault-finding but solution-seeking.
6. Keep Up with Current Laws and Regulations
Laws and regulations on maintenance and facility safety are continuously changing. Thus, your policies and procedures must keep up to ensure compliance and safety for all employees. You must regularly review applicable rules, evaluate your facility’s compliance, and update your policies accordingly. Don’t wait to revise and implement these updates until you are audited, or you risk getting fined for non-compliance.
7. Monitor Compliance
Establishing policies and procedures is not an instant process. Employees require time to understand and adapt to routine or workflow changes. Monitoring compliance is the best way to assess employees’ reception of these instructions and ensure compliance. This way, you can take the necessary actions or process revisions to improve compliance and safety.
Monitoring compliance should be easy and take a short time to complete. Lengthy and complicated checklists only add to the workload of employees. Inefficient monitoring often results in reduced productivity, erroneous reporting, and employees feeling mistrusted. These results ultimately lead to non-compliance.
CMMS for Compliance and Safety in the Maintenance Department
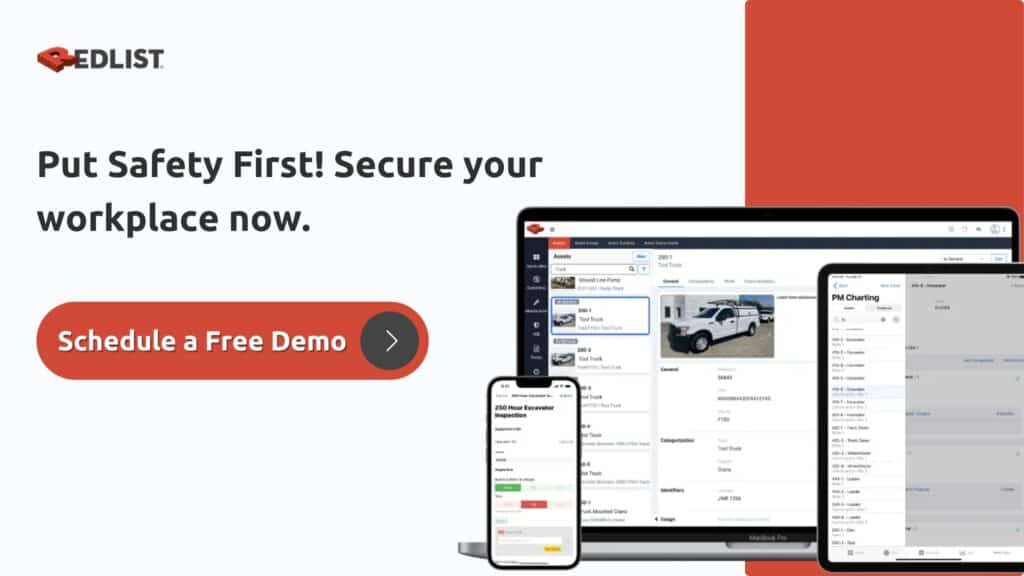
The maintenance department is involved in the upkeep of the whole facility. The implementation of its policies and procedures spans multiple departments. Thus, keeping employees compliant and safe can be a daunting task. Using a CMMS or computerized maintenance management system provides an easier way to manage all maintenance tasks across all departments.
Redlist is a next-level CMMS that allows you to manage all maintenance-related information in easy-to-use and portable software. Redlist lets you create, implement, and monitor maintenance programs, resulting in improved compliance and lower safety risk. With digitized information and cloud-based storage, critical data is accessible yet protected from loss or errors. Redlist also allows for clearer and faster updating of policies, further improving compliance and safety. To learn more about how Redlist supports compliance and safety in your maintenance department, contact us to schedule a demo today!