Inspections are vital to both lubrication and preventive maintenance, as they enable machinery to be kept in optimal condition. Every business is different, which means there isn’t one ‘right’ way to develop a perfect inspection route. However, there are many common mistakes that can lead to decreased efficiency and costly errors when designing your inspection program. In this article, we’ll discuss five potential pitfalls that you should avoid when creating an effective inspection route.
Why Should You Have Inspection Routes?
For starters, conducting regular inspections is vital for an effective maintenance strategy. It helps you identify issues before they become catastrophic failures, as well as enables technicians to keep machinery running optimally. However, developing a successful inspection route requires more than simply deciding on what is inspectable. The importance of an inspection route is that you clearly define the process to ensure that your technicians don’t miss anything. Some facilities have hundreds of assets, with several components to inspect on each asset. So, simply because your technicians follow the inspection route doesn’t guarantee that the inspections are effective.
The Problem with Undefined Inspection Routes
Handing your technicians a simple checklist of assets to inspect leaves a lot of open to interpretation. Depending on the knowledge, training, and experience of the technician, the results of the inspection can vary widely. Your most experienced technicians will likely have decent results following their intuition of what to inspect. But, less experienced technicians may only gather broad observations. Additionally, if your equipment doesn’t have a sight glass or some way to quickly inspect oil levels, your inspection route may overlook critical lubrication inspection points.
Common Inspection Route Mistakes
1. Incomplete Data or a Failure to Collect Data
This is a common error with inspection routes, since the data is quickly lost in the countless steps and repairs. The creation of a systematic process for recording and organizing inspection reports is necessary for inspection routes to be consistently successful. When making visual observations, it is extremely beneficial to also gather the data using images or videos. You can immediately determine the rate of change of an issue with a simple comparison to an earlier image. Additionally, this saves your technicians time, as it is far easier to take a photo or video than it is to explain an equipment issue in writing. Improving the efficiency and ease of recording data will ensure that your technicians record accurate, complete data every time. Lubrication management software makes this easy to do, as it is accessible on any mobile device (all of which have built-in cameras).
2. Not Placing Enough Value on Inspections
Because inspection routes are thought to be naturally simple, lube techs usually have just a vague understanding of the duties that they should be carrying out. Other condition monitoring procedures, however, come with high-quality training, credentials, and equipment. This is incorrect because human sense-based inspections are very important. If one is properly trained and outfitted with collection equipment, anyone passing by a machine, whether or not they are a lube tech, will be able to do a quick assessment.
3. Inaccessible Inspection Points
As mentioned earlier, it is easy to overlook the machines without sight glasses to check oil levels. An inspection route’s effectiveness is only as good as the quality of the individual inspections. It is essential to have visual accessibility to comprehend internal machine and oil conditions. If a machine is in operation, and it is entirely sealed on all ports without a sight glass, there isn’t much to inspect. You must modify your machines to have more effective inspection routes. While inspections don’t require as much detail as condition monitoring, they do require visual accessibility and some light modifications to support inspection route observations.
4. Lack of Training and Cross-Training
Inspections are sometimes thought of as simple tasks that don’t require extensive training or equipment, but there is plenty that the inexperienced eye can miss. However, you can easily fix this with proper training. For the most effective inspection routes, you can incorporate a method called cross-training. It’s as simple as bringing a team together and spending 20 minutes at each machine discussing the visual observations and possible issues. Because everyone has a different background and experience, this cross-training shares individual knowledge to improve the inspection process. Ideally, this is in addition to professional training on inspection routes.
5. Not Providing a Baseline to Compare Conditions to
While many of your technicians will have the knowledge and experience to know what is normal and abnormal, many may not. When building your inspection routes, you should define what is normal and what is abnormal for each inspection point. If possible, provide supporting documentation, such as a photo of the normal oil color and clarity. This will give your technicians an easy-to-understand and quick baseline to compare with current conditions.
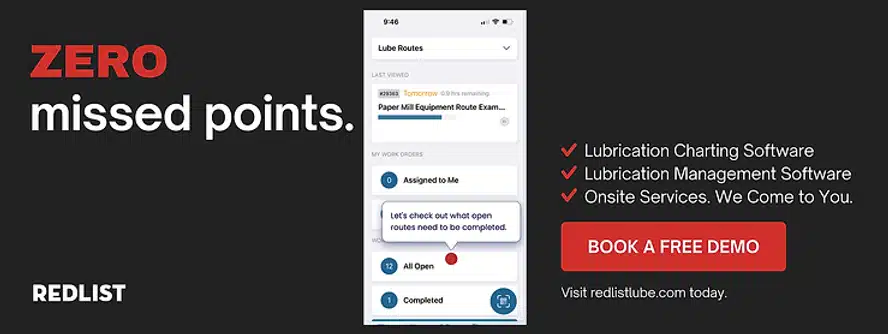
Next Steps to Optimize Your Inspection Routes
By taking these mistakes into account and making changes accordingly, you’ll be well on your way to optimizing your inspection route process. Implementing best practices for route creation and maintenance can help avoid many problems down the road. If you would like help fine-tune your inspection process or charting lubrication and inspection routes for your business, click here to learn more about our Lubrication Management Software.