The OSHA (Occupational Safety and Health Administration) hierarchy of controls is an excellent safety strategy to improve workplace safety. For the most benefit, you should use the OSHA hierarchy of controls before work begins. When you identify and attempt to eliminate or reduce exposure to hazards as part of the planning process, you are far less likely to have a safety incident. The hierarchy begins with the controls that make the biggest impact on safety and goes down from there.
Why Should You Start Before Work Begins?
As the saying goes, “An ounce of prevention is worth a pound of cure.” It is still important to address hazards after work begins, but it is most effective to address them beforehand. While it may delay the start of production, completing a thorough safety analysis before work begins is essential. If you can identify hazards ahead of time, you can design and implement safety controls. This goes a long way in preventing accidents, incidents, and near misses.
The 5 Parts of the OSHA Hierarchy of Controls
The goal is to manage a hazard with a control method as close to the top of the hierarchy as possible. These are the five controls ranked from most to least effective:
- Elimination
- Substitution
- Engineering Controls
- Administrative Controls
- Personal Protective Equipment (PPE)
Understandably, elimination is the number one goal. However, that’s not achievable for every hazard. Employees will still have to climb ladders, putting them at risk of a fall. You still need machines for manufacturing, putting operators at risk of various injuries. There are several more examples like that. In those cases, you look to lower-level controls to manage the risk the best that you can.
Elimination
The best method of hazard control is to completely remove it. For example, if an employee can do 80% of their work at ground level and save 20% for moving and installing the piece at height, then you can eliminate the majority of the fall hazard. You may see this in construction where employees can assemble a roof on the ground instead of at height. Other examples of elimination include removing or replacing tools or assets that are faulty or dangerous.
Substitution
Substitution is a great second option if you can’t eliminate a hazard. This involves replacing the original hazard with a less dangerous one. You still reduce risk even though you don’t eliminate it. For example, you could look at the hazardous chemicals you use in processing and substitute them with a less hazardous or non-toxic alternative.
Engineering Controls
When elimination and substitution aren’t an option, engineering controls are incredibly important to explore. In fact, it’s such a critical step that the National Institute for Occupational Safety and Health (NIOSH) has a searchable database to give you control ideas for various workplace hazards. Engineering controls involve adjustments to the work environment to decrease hazard exposure. Some examples of engineering controls are installing exhaust ventilation to reduce fumes or machine guarding to reduce operator injury.
Administrative Controls
Being fourth in the OSHA hierarchy of controls means administrative controls are less effective. However, they are better than nothing if you cannot implement the first three controls to manage a hazard. Administrative controls create processes, procedures, and rules to limit employee exposure. You can do this by arranging tasks and schedules to limit exposure time or ensure employees use the buddy system for tasks like confined space entry. Also, you can even implement ways to warn employees of hazards. This may include alarms, signs, or Health Safety & Environmental (HSE) software with custom safety checklists and reminders.
Personal Protective Equipment (PPE)
The final level of the OSHA hierarchy of controls is likely the most well-known and widely used. PPE comes in all shapes and sizes to protect against hazards, from eye protection and fall protection to fire-resistant clothing. While PPE is often considered the last line of defense, it is a hazard control method you can combine with the other methods. Actually, OSHA has several regulations requiring PPE for your employees.
Combining OSHA Hierarchy of Controls
The hierarchy is simply a guideline, and you’re not limited to using only one control method. In the case of hazardous chemicals, you may do the following:
- Substitution – Substitute a less hazardous chemical to reduce overall risk
- Engineering Controls – Install proper exhaust ventilation to reduce fumes
- Administrative Controls – Create a policy that puts a time limit on chemical exposure
- Personal Protective Equipment – Require the use of PPE when handling chemicals
As you can see with this example, you may not eliminate the hazard, but you can reduce the risk as much as possible.
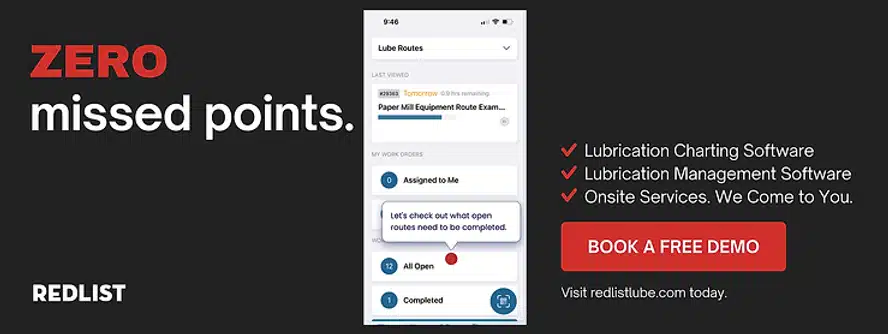
Get the Support of HSE Software
Your hazard controls are not something to create once and never touch again. It is essential to monitor the effectiveness and make adjustments. Redlist’s HSE software supports you in managing risk and streamlining your safety program. One Redlist user was able to reduce their overall incident occurrence by an average of 50% after implementing the HSE software in their process. To explore how our HSE software can support your safety program, schedule a demo today.