Particle contamination is a major issue in lubrication management. If unmanaged, particle contamination can be detrimental to machinery performance and longevity. This post provides all the necessary information on particle contamination, helping you achieve effective and successful lubrication management.
What is Particle Contamination?
In lubrication, particle contamination refers to the presence of foreign solid particles in lubricants or oils used in machinery and other assets. These solid particles or contaminants can come from various sources including:
- Normal wear and tear of machine components
- Debris from the environment
- Produced when operating or maintaining the machine
These solid contaminants in lubricants can act as abrasives, causing faster wear of bearings, gears, cylinders, and other components. Furthermore, this increased wear on machines reduces their efficiency by increasing friction and heat generation. Lastly, increased wear decreases reliability, leading to expensive repairs and more downtime.
The Characteristics of Particle Contamination
Preventing particle contamination starts with understanding the characteristics of solid contaminants:
Size
Defined as a particle contaminant’s effective spherical diameter, size is usually measured in microns or micrometers. A contaminant’s size determines its ability to enter machine gaps and cause abrasion on surfaces. Particle contaminant sizes range from macroscopic (visible to the naked eye) to microscopic (visible under the microscope) to submicron (less than 1 micron and too small to be seen under the microscope).
Lubrication filtration systems are effective in eliminating contaminants of different sizes, with different filters that can remove specific size ranges. Additionally, regular oil analysis can help monitor contaminants and identify size ranges, helping prevent major issues stemming from contaminated lubricants.
Shape
A particle contaminant’s shape determines its abrasive ability. A spherical contaminant is less likely to indent, cut, or rub a surface than a contaminant with angular or sharp edges. Angular particles are often the products of crushed or broken-down large particles.
Understanding particle shapes helps in predicting contaminant behavior and preventing their related issues. The presence of spherical contaminants, for example, may not cause too much abrasion but they tend to block and reduce flow. Similar to particle size control, effective lubricant monitoring and filtration help manage particles of various shapes.
Surface Area
The surface area of a particle contaminant is the total external surface that is exposed and in contact with the lubricant. When larger particles break into smaller particles, the effective surface area increases, allowing for more friction, wear, and chemical interaction between the particle and lubricant.
Control of increased contaminant surface area includes using effective filtration systems, practicing proper maintenance procedures, and using high-quality lubricants.
Particle Count
The particle count of contaminants refers to the total number of particles for a given amount of lubricant. Contaminant particle count determines the cleanliness and quality of lubricants. It also determines lubricant performance and the likelihood of wear and machine damage.
Assessing and keeping particle counts below critical levels is essential for minimizing wear, optimizing machine performance, and extending asset life. Effective and regular filtration and oil analysis, proper lubricant handling and storage, and maintenance best practices are major ways to control increased particle count in lubricants.
Hardness
A particle’s hardness determines its ability to cause wear and fatigue. Hardness is the resistance to being deformed through compression or fragmentation. Harder particles can cause more abrasion and surface damage. They are also more difficult to capture by filtration systems, especially if these systems are not equipped to handle such hard contaminants.
Common sources of hard lubricant contaminants include metal wear debris from components like gears, bearings, and seals, as well as abrasive contaminants from external sources such as dirt, sand, or grit. Aside from effective filtration, the best control for hard contaminants is the identification of their likely sources. Regular monitoring and analysis of their presence are also helpful control measures.
Density
Density refers to a particle’s mass per unit volume. It influences a solid contaminant’s behavior when present in lubricants. High-density particles are prone to settling, causing sediment buildup and a decrease in lubricant effectiveness. Also, high-density particles require centrifugal separators or filters while low-density particles call for more sophisticated techniques.
The use of appropriate filtration techniques is critical to address density-related contamination issues. In addition, it is also crucial to use lubricants with the appropriate additives and properties that can minimize these issues.
Chemistry
A particle’s chemistry or chemical composition determines its ability to interact with the lubricant. Furthermore, a particle’s chemistry dictates its solubility, reactivity, and potential chemical reactions with the lubricant. For example, even a small and non-abrasive particle can pose a major threat to lubrication success for having reactive chemical properties.
Controlling a contaminant with reactive chemistry starts with effective filtration. However, not all particles can achieve 100% removal with filters, especially smaller particles. Regular monitoring and oil analysis help detect chemical interactions early and prevent major lubrication issues.
Polarity
Polarity refers to a particle having negative or positive ionic charges that influence its affinity with other particles or chemicals. The polarity of a contaminant determines its tendency to interact with lubricant molecules and machine surfaces. Polar contaminants, for example, can interact with polar oil components, such as rust inhibitors or antiwear agents, leading to the depletion of these components and a decline in lubricant performance.
Furthermore, polar particles are more likely to clump together, forming clusters that cause blockages and reduced oil flow. Polar contaminants also call for specific filtration methods, such as polar filters or chemical treatments. Understanding contaminant polarity helps identify the ideal lubricant type, filtration methods, and other strategies for the effective lubrication of machines and equipment.
Magnetic Reaction
The magnetic reaction of particles refers to their ability to be attracted to or influenced by a magnetic field. Particles containing iron react to magnet-equipped filters and sensors, thus removing and controlling these contaminants.
However, if these magnetic filters and sensors are used on particles having low-magnetic reactions, these particles get magnetized and cause negative effects on lubrication. Thus, understanding the magnetic reaction properties of particle contaminants helps in implementing appropriate contamination control measures.
Conductivity
Conductivity refers to a particle’s ability to conduct electric current. Conductive particles can help dissipate the electric charges generated within a flowing lubricant. Having conductive contaminants can thus result in positive effects on lubricants.
Although not a common parameter when analyzing particle contamination, the conductivity of particles provides valuable insights into lubricant conditions and contamination levels.
Protect Oil from Particle Contamination
When protecting oil from particle contamination, there are five critical steps or areas you must consider:
1. Receiving New Oil
New lubricants are not 100% contaminant-free. Implementing proper practices when receiving new lubricants aims to maintain the low contaminant levels necessary for optimal lubrication. These practices include maintaining a dry and clean receiving location, employing the FIFO (first in, first out) policy, and using well-ventilated and accessible holding facilities.
2. Storage and Conditioning
Proper lubricant storage, like keeping conditions dry, clean, and well-ventilated, minimizes contamination as lubricants wait to be used. Also, implementing conditioning methods like filtering the lubricant before use further controls contaminant levels. Conditioning by filtration can be done over storage containers or when transferring the oil to the dispensing container.
3. Dispensing and Application
Using dispensing containers that are not fully sealed and using specifically dedicated containers are two of the most effective ways to prevent contamination. Ensuring that the right lubricant is applied to the right machine further prevents contamination. Using a color-coded system where one color is assigned for each lubricant type is standard practice for preventing contamination at this lubrication step.
4. Preventing Entry of Contaminants
Airborne contaminants can enter the lubricant or lubricating areas when oil reservoirs are allowed to ‘breathe’. Fitting oil lubricating systems with ‘air breathers’ prevents water, dust, and dirt from entering the system. Mechanical methods such as the use of seals and coverings further prevent the entry of contaminants.
5. Removing Machine-Generated Contaminants
Filtration is the best method of removing any wear debris and other contaminants generated from within the machine. Contaminants produced from chemical reactions such as oxidation can also be controlled through filtration. Additionally, regular oil analysis helps monitor and detect any unfiltered or newly-developed contaminants.
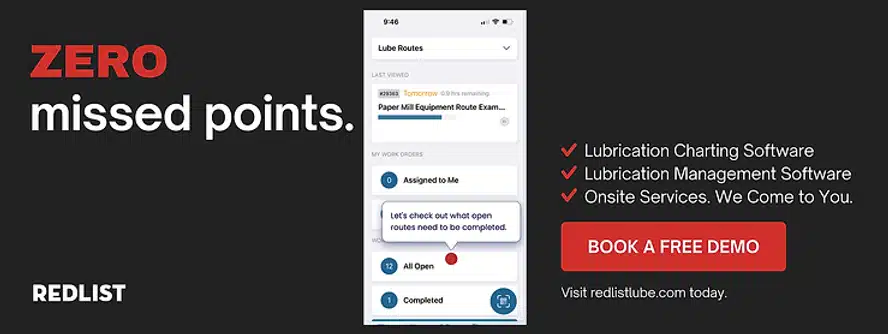
Manage Particle Contamination with Redlist
Redlist is a must-have tool for keeping particle contamination under control. Your lubrication management can benefit through:
- Scheduled Maintenance – Redlist helps ensure timely detection and mitigation of particle contamination by scheduled oil sampling, filter replacement, inspections, and other critical monitoring and maintenance tasks.
- Data Recording and Analysis – Redlist can store comprehensive historical data on machine maintenance, oil analysis results, contamination levels, etc. These data help you track contamination trends, identify critical contamination sources, and develop effective contamination control strategies.
- Inventory Management – Redlist lets you track inventory levels of lubricants, filters, and other lubrication materials. Thus, you can maintain the availability of these materials and track their usage rates for forecasting, budgeting, and other management purposes.
- Integration – Redlist can integrate with condition monitoring systems such as online particle counters, contamination sensors, and oil analysis testing. Integration allows faster and more seamless data exchange, thus enabling real-time monitoring of contamination levels and immediate maintenance actions.
For more of Redlist’s benefits for your lubrication and maintenance programs, schedule a free demo with our experts today!