Traditionally, you have to perform machine monitoring manually. Your technicians have to check equipment and collect readings regularly. Then, enter that data in a spreadsheet to later generate reports or perform a strategic analysis of the data. However, as machines get more complex and technology offers more support, you can greatly improve your machine monitoring practices. Implementing IoT (Internet of Things) sensors that integrate with Enterprise Asset Management (EAM) software is the biggest step you can take to advance your machine monitoring.
Why Should You Improve Machine Monitoring?
For starters, machine monitoring drives preventive maintenance, which benefits production. This connected cycle of actions and reactions leads to greater efficiency, decreased downtime, improved equipment safety, and a positive impact on the bottom line.
If you’re transitioning from manual machine monitoring to digital, then there are even more benefits. Your technicians save time collecting and entering data, as well as generating reports. When you need to make a decision, you can quickly look at your reporting dashboard to see real-time equipment information presented in an easy-to-read chart. Additionally, your data will be more consistent and accurate due to the constant stream of data from your sensors.
Sensors integrated with an EAM allow you to configure automatic notifications to maintenance managers in case of an abnormal reading. So, you can catch an equipment issue at the first sign of trouble, instead of later when collecting a manual reading. For example, a sudden and unexpected temperature increase can trigger a notification to your maintenance manager. As this is a sign of friction and a lack of lubrication, the manager can immediately send a technician to handle it before it causes equipment failure.
You can put all of this to work to adjust maintenance, change production setup, or forecast future equipment needs and design.
What Data Can You Monitor?
Every piece of equipment and every business will have different machine monitoring needs. Determining your needs is an essential step in improving machine monitoring. These are a few of the data points that you can track:
- Maintenance data, such as planned and unplanned downtime.
- Reliability data, such as energization time, standby time, failures, and utilization rate.
- Machine status, such as speed, cycle start and stop, and run rate.
- Product data, such as humidity, temperature, pressure, or vibrations of the product managed by the machine.
- Quality performance data, such as scrap rate and first-pass yield.
- Electricity usage data, such as energy consumption and savings.
How to Implement IoT Machine Monitoring
Going digital with your machine monitoring will require both hardware (i.e. sensors) and software (i.e. EAM). The hardware and software can work together to seamlessly manage data retrieval, transfer, and analysis. So, the two must integrate in order to work effectively and provide you with the greatest benefit. Without integration, the automation of data collection, processing, and reporting is limited. Once you put sensors on your machines, the amount of data is overwhelming without a system to manage it. Redlist integrates with sensors, so your real-time data can auto-populate your reports. This puts machine monitoring information at your fingertips at all times.
Now that you know your basic IoT machine monitoring needs, the next step is to determine your specific needs. What is your machine monitoring goal? What machines do you want to monitor, and what are their parameters? Next, you can use this information to decide what hardware and software would be a good fit for you. If you’d like to test the solution on a single machine or one area of a plant, you can do that. It’s an excellent way to ensure that the sensors and software meet your needs before you make a plant-wide investment. Finally, you would have a regular review of your machine monitoring process to identify any areas for improvement.
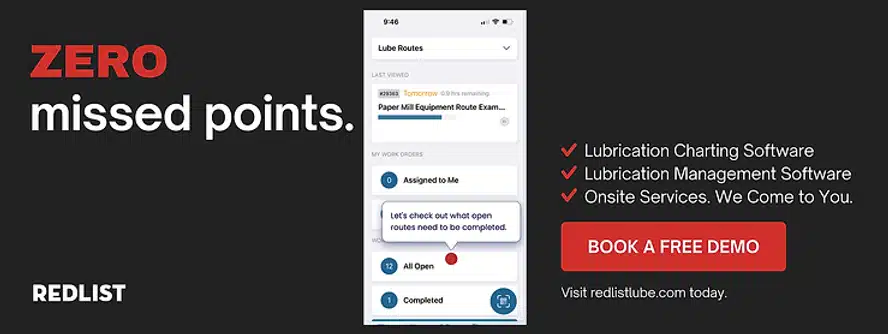
Digitize Your Machine Monitoring with Redlist
In most cases, machine monitoring is something you already do. However, implementing technology will save you time and streamline the data collection and reporting process. Not only will you reap the benefits outlined above, but also you will find it becomes an essential part of your decision-making.