Today’s technology enables you to automate the completion of the reports required by the Occupational Safety and Health Administration (OSHA). The OSHA 300 series forms include the 300, 300A, and 301 forms. The problem so many companies face is that the OSHA forms are very high level and aren’t industry-specific. For starters, they don’t ask helpful questions, such as how long has the injured person been employed? Where did the incident occur? Or, what team the person is on? For example, are they a mechanic, operator, or part of your sanitation team? Furthermore, the OSHA forms don’t allow you to truly understand why incidents are happening or how often. And, the big one, if there is any commonality between events that you can possibly prevent.
The OSHA forms are just capturing basic information, not actionable data. So, you create your own incident reporting forms. Now you have the issue of duplicate data entry and getting buried in paperwork filling out multiple forms. With the potential of increasing OSHA fines, this is the perfect time to automate this process.
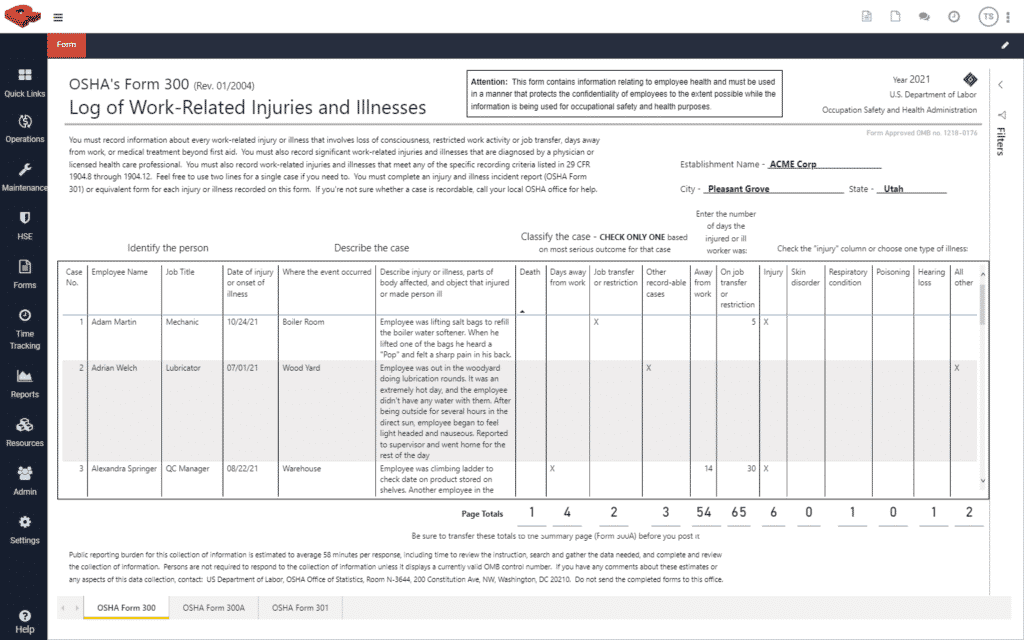
How to Automate Your OSHA 300 Form with Redlist
The first step is to create a digital Incident Investigation Form using Redlist. This combines all the required OSHA 300 information with any company-specific information into a single form, eliminating double entry. Then, the form is available to employees through the cloud-based Redlist app, which they can access from any mobile device. You can configure the form and its settings to fit your company’s specific needs.
Also, you can set permissions for employees so that they only see the questions and information that is relevant to them. For example, the injured employee can enter their personal information and record how the incident happened. Using the same form, their manager can review what they submitted, add additional notes, and sign off on the report. All in a section that is not visible to the employee that initially submitted the report.
This creates an incident reporting process that enables the employee and manager to quickly and easily complete the digital form.Once completed, you even have the option for the form submission to trigger a notification. This is excellent for companies with multiple locations that want a review and approval step. Redlist can automatically notify the safety director whenever an incident report is submitted. Not only alerting them that an incident happened, but also providing all of the details of the incident.
Then during the review process, if the event qualifies as a recordable incident, the approver marks the report as such, and all the data auto-populates the OSHA 300, 300A, and 301 forms. It’s as simple as creating your form, filling it out, and reviewing if you include that step.
The Benefits of Automating Your OSHA 300 Series Forms
There’s the benefit we already touched on of eliminating duplicate data entry, but there are plenty more:
- Avoid OSHA Fines – If a paper form gets lost or forgotten, you’re facing a fine. With Redlist, it’s digital, real-time and nothing gets lost.
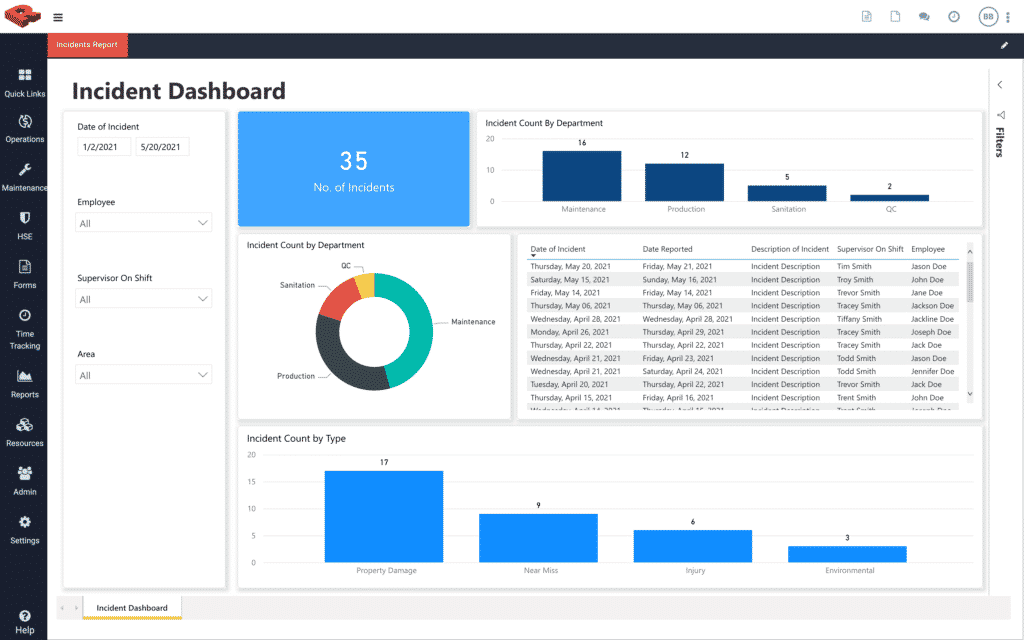
- Auto-populate Internal Reports – The incident report data not only auto-populates your OSHA 300 series forms, but also any internal reports. You get immediate, actionable data that allows you to find trends in your incidents and take corrective action to drive your overall number of incidents down.
- Track Everything in One Place – Whether you have one location or several, you can access all of the incident data from anywhere because it’s all saved digitally in one location.
- Improve Report Accuracy – Digital forms mean you no longer have to decipher handwritten forms from the field stained by grease or lubricants on employees’ hands.
- Easily Change and Update Forms – Updating paper forms is a slow process and, inevitably, there will always be someone working with an old form. Redlist forms rollout updates to everyone, immediately, and remove any old versions of the forms so all new forms include the new information.
- Multiple Language Options – If you want to provide a Spanish form to a Spanish-speaking employee, you can do that easily with Redlist.
- Automatically Calculate Your Total Recordable Case and DART Incidence Rates – Take the work out of manually calculating these metrics by pairing Redlist’s HSE (Health, Safety, and Environment) module with its Field Service and Dispatch module. Or, create a simple form to capture the total number of hours worked by all employees, and let the system take care of the rest.
Automated Incident Reporting for a Safer Workplace
This level of control and ease just doesn’t exist with paper forms. When it comes to OSHA fines, it is a worthy investment to make your incident reporting as strong and accurate as possible. Redlist’s implementation team works with you to configure the forms to your needs. So, together, we can create a safer, more efficient, and more productive workplace.